0 inspection and maintenance, 1 discs – Flowserve Double-Disc Gate Valve Sizes 2.5 User Manual
Page 23
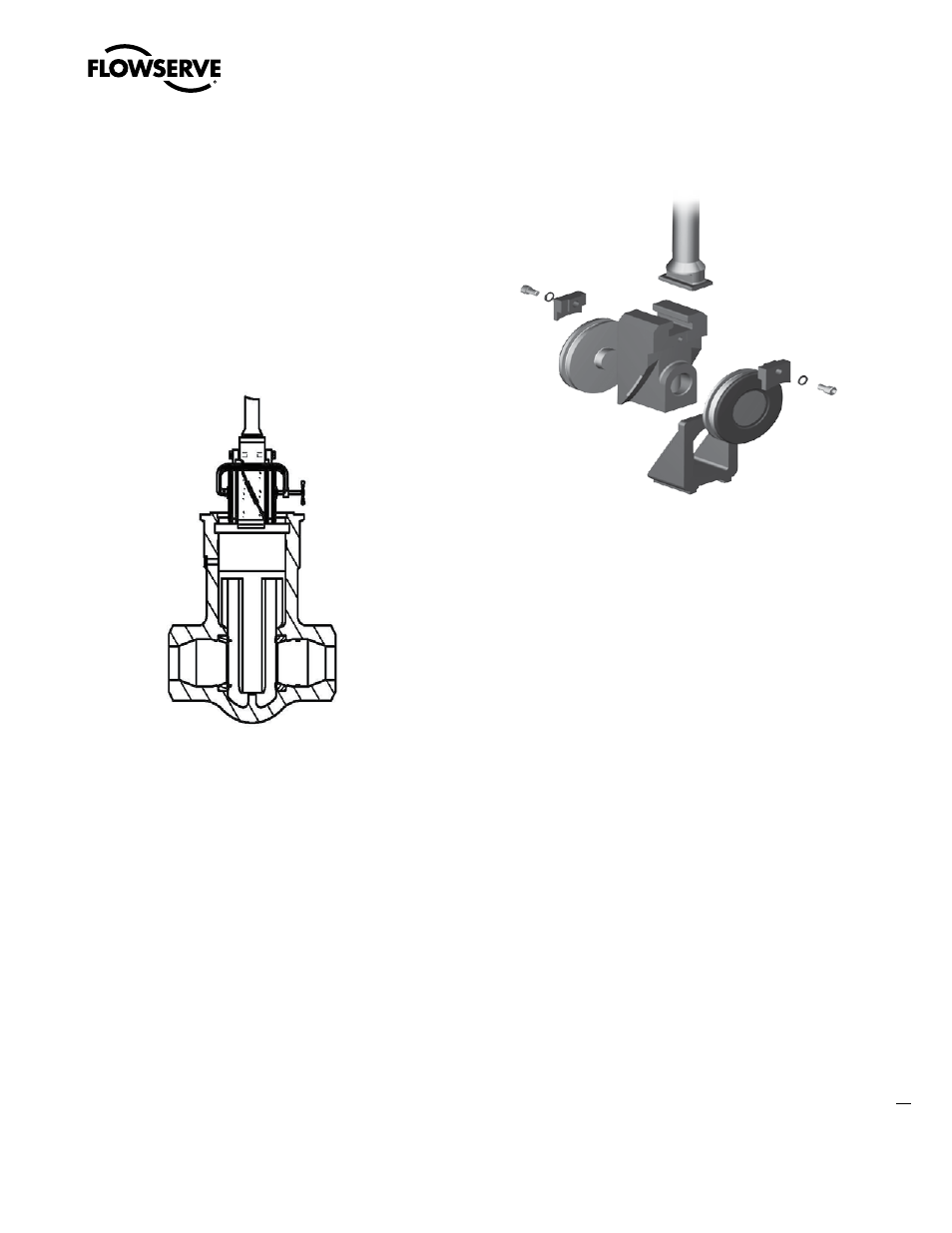
23
Anchor/Darling Double Disc Type Gate Valves FCD ADENIM0003-01 - 07/14
flowserve.com
6.4 Disc Pack & Stem Assembly
(Figs. 18 & 19)
a) The disc pack and stem assembly can be lifted out of the body
utilizing an eye-bolt threaded in the tapped hole provided in the end
of the stem.
b) As the stem to upper wedge interface is a T-head design, caution
must be applied to prevent the disc pack from disengaging from the
stem.
c) Before the disc pack is free of the body guides, C-clamps should
be installed as shown in Fig. 18. This will prevent the discs from
disengaging from the upper wedge and falling causing damage or
injury.
d) Once the assembly is safely laid down or supported, the stem can
be separated from the disc pack.
e) The discs can be removed from the upper wedge by first removing
the disc retainer fasteners and the disc retainer. At this point the
discs can be separated from the wedge assembly and set aside.
If they are in good condition and require no lapping, the seating
surfaces should be covered with protective material to prevent
scratching.
f) If further disassembly is required, the lower wedge (071) can now
be separated from the upper wedge (069). In most valves, a wedge
spring (269) is fitted between the upper and lower wedges in order
to prevent premature wedging if the valve is installed in a vertical
line. When separating the two wedges, care should be taken that
the spring is not allowed to fly out and possibly cause injury or
become lost.
7.0 INSPECTION AND
MAINTENANCE
Whenever a valve is disassembled, it should be inspected and deficien-
cies corrected as described in the following paragraphs.
7.1 DISCS
a) Inspect the hardfaced seating area to insure it is not nicked,
gouged, scratched or scared. The surface finish should be 16 RMS
or better. Machine and/or lap to obtain the necessary finish. After
lapping reestablish the radii on the hardfacing outside diameter and
inside diameter. This is a very important step necessary to assure
the seats don’t score when the valve is operated.
b) Liquid penetrant inspect the hardfacing to assure it is not cracked.
c) Blue check the faces to assure flatness. The preferred method is
to place a light coating of bluing on a flat plate, place the disc on
the plate, turn the disc about 20° and back once and then check
the disc for transfer of the bluing. An acceptable face shows an
uninterrupted trace of bluing for 360° near the center of the disc
face.
d) Inspect the hardfacing thickness. Hardfacing resistance to galling
starts to diminish when the hardfacing thickness is less than
1/8”. This is caused by the effect of mixing base material into
the hardfacing deposit when first welded. Although the rate of
wear, (i.e. scoring or galling) is dependent upon the actual service
Figure 18
Figure 19