0 care of valve prior to installation, 0 installation instructions, 1 receiving inspection – Flowserve Double-Disc Gate Valve Sizes 2.5 User Manual
Page 7: 2 handling, 3 storage, 1 rigging, 2 cleaning, 3 installing valve in line
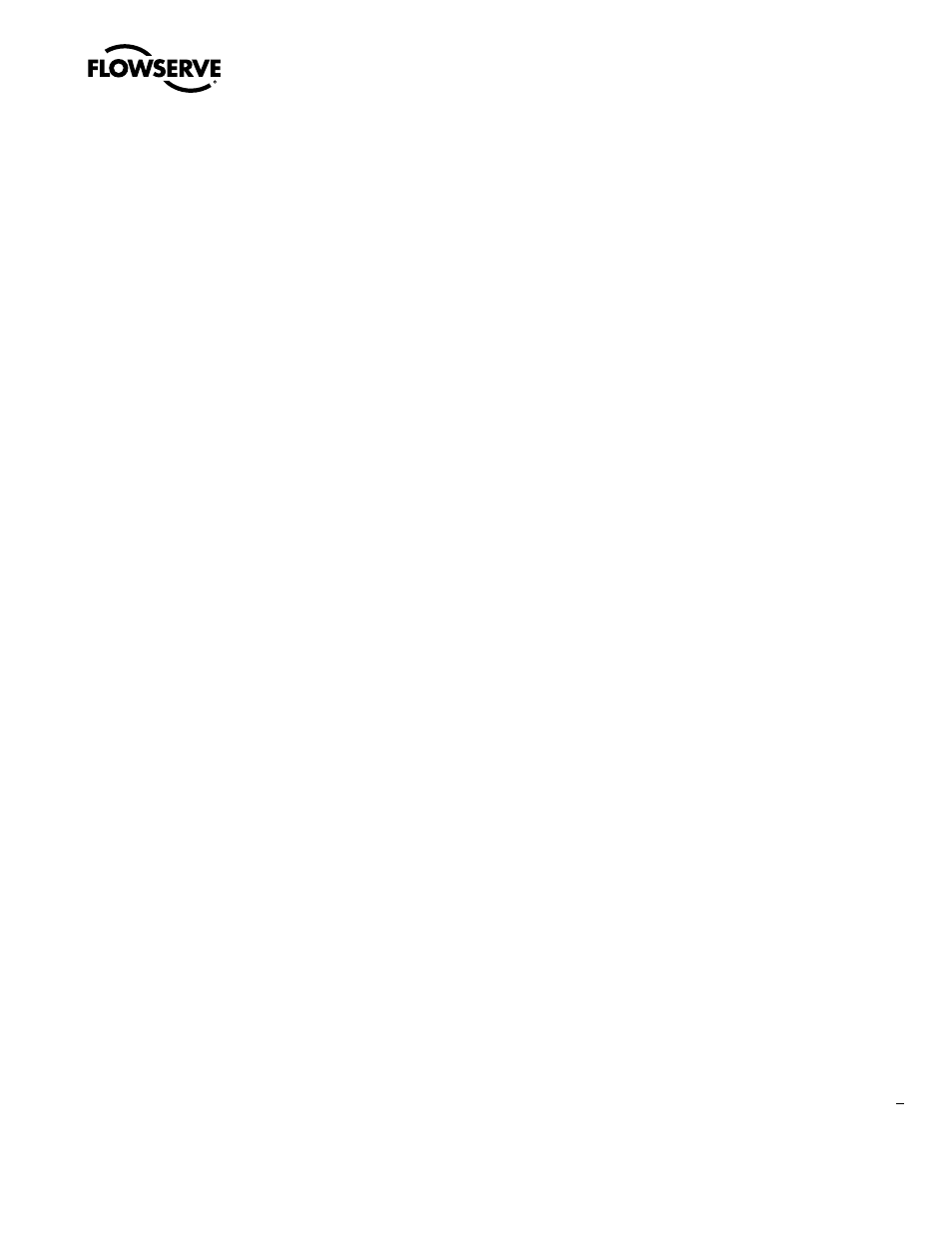
7
Anchor/Darling Double Disc Type Gate Valves FCD ADENIM0003-01 - 07/14
flowserve.com
the acme stem threads. The pneumatic and hydraulic cylinder actuators
provide direct linear motion to the stem. Always consult the mainte-
nance manual for the specific actuator or actuator accessory before
using or performing maintenance on these components.
Sealing of the bonnet-stem penetration is accomplished by a bolted
gland stuffing box containing ring type packing. An emergency back up
seal is provided in the form of a backseat rigidly mounted in the bonnet.
2.0 Care of Valve Prior to
Installation
2.1 Receiving inspection
Upon receipt of the valve, thoroughly inspect it for shipping damage.
As a minimum, the following items should be checked:
1. Handwheel and shaft - check for bending or impact damage.
2. Switches and actuating mechanisms - bent or broken parts?
3. Missing or loose bolting?
4. End covers in place?
5. Is valve securely fastened to shipping skid?
6. Are spare parts shipped with valve in place and secure?
2.2 Handling
The valves are shipped strapped to wooden skids designed to be
moved by forklift. It is recommended that when being handled prior
to installation, the valve be kept on its skids and a forklift truck be used
for moving. If an overhead crane is used, care must be exercised to
center the load. The slings should not lift the valve by the wooden skid
structure alone, but must pass under the valve.
2.3 Storage
Store valves on their shipping skids in a clean dry area protected from
the weather.
Valves are generally shipped without the permanent packing installed.
Experience indicates that stem corrosion pitting can result when
valves are stored with the packing in place. For this reason we do not
recommend installing the packing until valve is to be put in service.
The service packing is shipped with the valve, contained in a plastic
bag placed in the valve port or attached to the yoke. If the packing is
removed for storage elsewhere, reseal the valve end covers to protect
the internal cleanliness of the valve.
Motor actuated valves, if stored for more than a few months require
special care of the actuator. Motor and switch compartment heaters, if
supplied, should be connected. The major concern is condensation on
the internal parts of the actuator. For this reason, rapid and/or extreme
temperature and humidity changes should be avoided. Storage in a
temperature and humidity controlled environment is desirable. Long
term storage of motor actuators may affect the terms of the warrantee
and the manufacturer should be contacted for specific information.
3.0 Installation Instructions
3.1 Rigging
When lifting the valve for installation in the line, it is important that
slings of adequate size be used. The capacity of the sling must
exceed the weight of the valve. Slings should pass under the valve
body and through the yoke arms. Block carefully to prevent damage
or abrasion of component parts and finishes.
3.2 Cleaning
Prior to installation remove the valve end covers and inspect for
cleanliness. If any sign of foreign matter is observed in the valve
internals, open the valve and place it on its side (stem horizontal) and
flush thoroughly with water. Steam or air may be used if water is not
available but exercise caution that the high velocity does not drive
debris into clearance spaces.
3.3 Installing valve in line
3.3.1 The pipe must be properly supported and aligned with the valve.
Seat leakage in valves is frequently caused by seat misalign-
ment resulting from excessive end movements introduced in
the cold springing of the connecting pipe.
3.3.2 Before weld end valves are welded into the line, raise the disc
assembly off the seat a sufficient distance to prevent arcing.
3.3.3 The preferred installation of double disc gate valves is with the
lower wedge on the downstream side. The only exception is
that when in a vertical pipe with flow down, the lower wedge
should be on the upstream side. Although standard convention
at Flowserve locates the lower wedge on the right hand side of
the valve when facing the nameplate, it is recommended the
assembly drawing be checked to verify orientation.