Flowserve G4 Sleeveline Plug Valves User Manual
Page 14
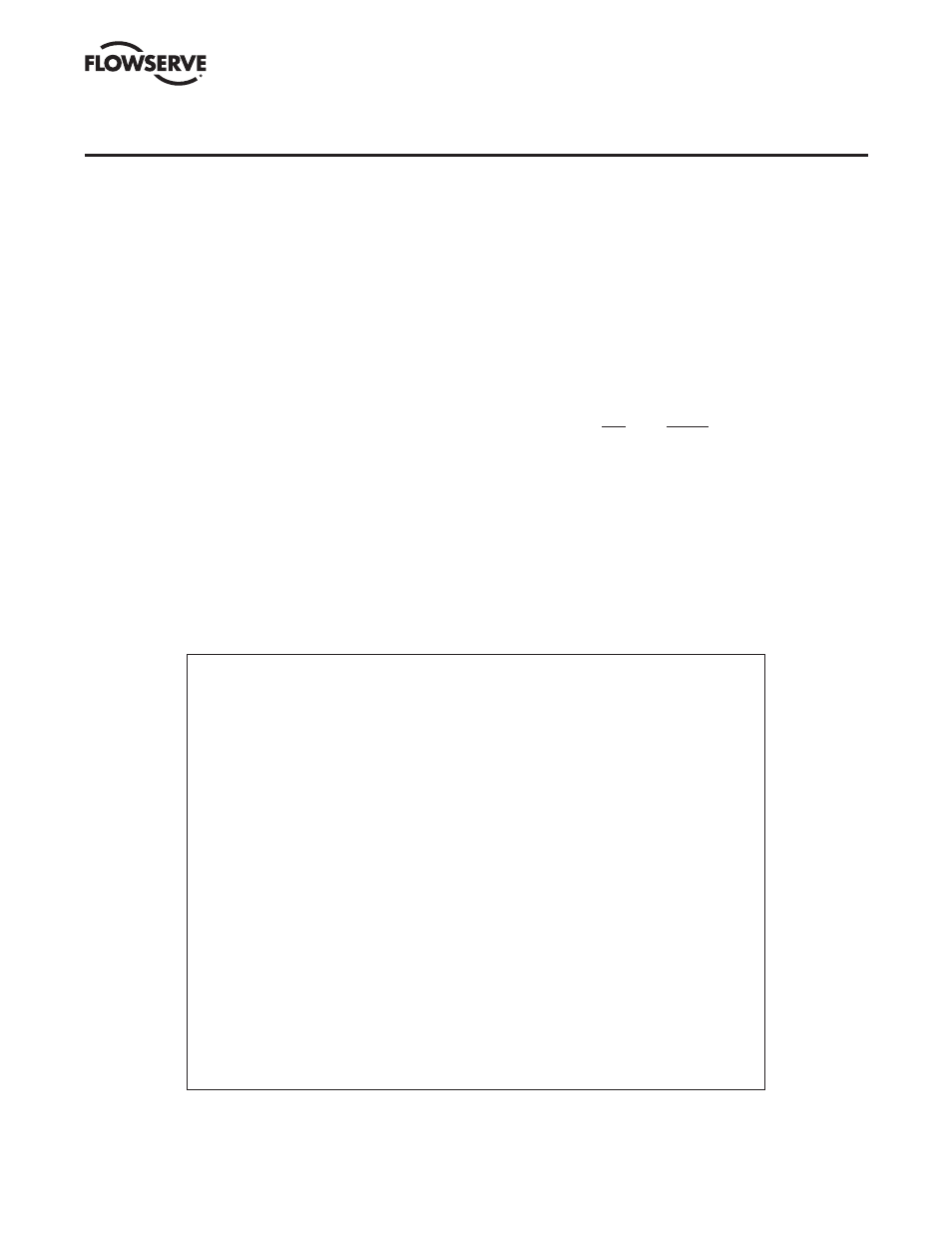
14
G4, G4ZHF AND G4R USER INSTRUCTIONS ENGLISH 5-14
15. Care must be taken when lifting the packing ring/metal
diaphragm as to prevent damage or wrinkling to the seal-
ing areas of the diaphragm. Should the metal diaphragm
be wrinkled in the sealing area, the top cap is to be
reworked for flatness and surface finish. The diaphragm
is to be replaced and repeat steps 11 through 13.
16. Slight flare up of
1
/
16
" on the outer diameter edge of the
metal diaphragm is permitted but if excess bending
occurs, the metal diaphragm must be custom fitted to
the body counterbore while located on the plug stem.
17. Uneven gasket compression to the Grafoil (Part 21) or
PFA diaphragm gasket (Part 6) is cause for rejection and
replacement of those parts.
18. Once it has been determined that the gaskets fit properly,
the top cap (Part 3), grounding spring (Part 17), and
thrust collar assembly (Part 11) are reinstalled and steps
11 through 13 are repeated. Continue to tighten the top
cap fasteners in 50 ft-lb increments in a crisscross fash-
ion to the levels found in Table #1a & 1b on page 11.
NOTE: All fastening torques are for Loctite
®
coated, corro-
sion-free fasteners and nuts. Extreme care must be taken
to prevent overstressing fasteners and sub sequent valve
parts by fastening in excess of industry standards for
appropriate size and alloy fasteners. Ref. Torque Table
#1a & 1b on page 11.
19. The plug is turned a minimum of three times and the
sleeve is checked on all four seal zones for tears.
20. With the plug in the open position, adjuster fasteners
(Part 12A) are then torqued to the following levels: Ref.
Table #2. The height of the plug port should be positioned
approximately
1
/
16
" above, to flush with the body port.
Size
Torque
6"
15 ft-lb
8"
31 ft-lb
21. Operate the plug a minimum of three times.
22. The gear box or actuator is installed with the plug set in
the open position, and the adjusting screw is then locked.
Careful attention is required to set the gear box stop
screw at 90° rotation for the closed position. A protractor
may be used to check for 90° rotation or alignment
scribes may be noted on the gear box cover.
SECTION VI
ASSEMBLY SPECIFICATIONS – FIRESAFE VALVES G4Z, G4ZHF, G4ZR
Selection, Installation, Operation and Maintenance
Flowserve Corporation has established industry leadership in the design and
manu fac ture of its products. When properly select ed, each product is designed to
perform its intended function safely during its useful service life. However, it is
necessary that Flowserve customers be fully aware of their responsi bilities when
using these products.
Each Flowserve valve product may be used in numerous applications under
a wide variety of industrial service conditions. Although Flowserve can, and often
does, provide general guide lines, it is obviously not possible to provide application-
specific data and warnings for all conceivable applications. The purchaser/end user
must therefore assume the ultimate responsibility for the proper selection, instal-
lation, operation and main tenance of the products. Read the appropriate IOM before
installation, operating or repairing any valve. The purchaser/end user should train
its employees and/or contractors in the safe use of the Flowserve products in
connection with the purchaser’s manufac turing processes.
Flowserve will continue to provide its customers with the best possible products
and service available. We do not recommend substituting surplus or remanufac-
tured valves over new Durco valves or those repaired in an authorized service center.
Should you have any questions about these provisions or about Flowserve products
in general, please contact your local Flowserve valve representative, who will be
happy to help.