Foreword, Welding – Flowserve G4 Sleeveline Plug Valves User Manual
Page 2
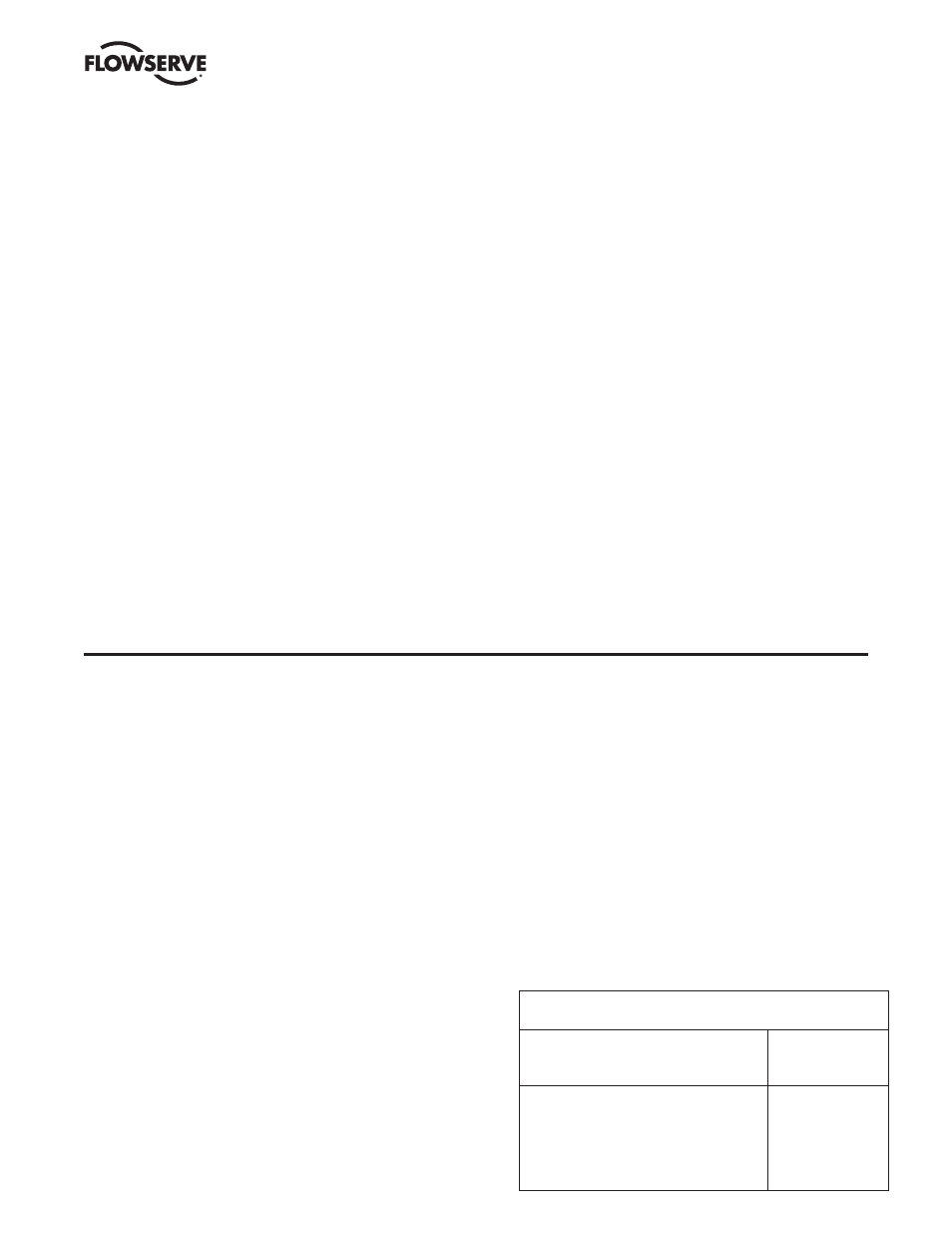
2
G4, G4ZHF AND G4R USER INSTRUCTIONS ENGLISH 5-14
FOREWORD
Flowserve Corporation, Flow Control Division, has established
this Installation, Operating and Maintenance Manual to facili-
tate field installation, operation and repair of G4, G4ZHF and
G4R valves.
It is recommended that questions or concerns involving
the processes described in this manual be directed to the
local Sales Representative of Flowserve Corporation. Only
Flowserve replacement repair parts and assembly tooling
made or designed by Flowserve Corporation should be used.
Part numbers referenced in the following sections are avail-
able from Flowserve Corporation, Flow Control Division.
TABLE OF CONTENTS
SECTION TITLE
PAGE
FOREWORD
I
INSTALLATION INSTRUCTIONS – FLANGED AND WELDED G4, G4ZHF, G4R
2
II
OPERATING/MAINTENANCE – G4, G4ZHF, G4R
3
III
VALVE DISASSEMBLY – G4, G4ZHF, G4R
4
IV
PRESSURE CONTAINING FASTENERS
5–6
V
A. VALVE ASSEMBLY –
1
/
2
" &
3
/
4
" G4, G4R
7–8
B. VALVE ASSEMBLY – 1"– 8" G4, G4R
9–11
VI
ASSEMBLY SPECIFICATIONS – FIRESAFE VALVES G4Z, G4ZHF, G4ZR
12–14
VII
RECOMMENDED SPARE PARTS
15
SECTION I
INSTALLATION INSTRUCTIONS – FLANGED AND WELDED G4, G4ZHF, G4R PLUG VALVES
FLANGED:
Installation of Flowserve flanged valves is best accomplished by
locating valves in pipeline flanges, assuring all corrosion and
foreign materials are removed from pipe flange, and then center
gaskets with the valve flanges. Fastener or taper pins should be
used to align holes and locate gaskets. Fasteners should be
tightened to the corresponding valve and fastener size.
WELDING:
Flowserve Corporation, Flow Control Division recommends
using only qualified welding procedures and personnel for weld
installation of G4R valves.
The following precautions should be observed:
1. The valve should be inspected prior to welding to assure that
no foreign materials obstruct the flow passageway and that the
weld preparation is free of corrosion and physical damage.
2. The valve should be in the open position while being welded.
Open position is when the flats on the plug stem are parallel with
the pipeline.
3. The G4R valve contains various sleeve and diaphragm materials
that have a different maximium temperature limitation. Refer to
Table 1.1 for temperature limitations.
4. The valve body sleeve and diaphragm must not exceed these
tem peratures during welding. This includes preheats, inter passes,
or post weld heat treatments, as applicable. Refer to Figure 11-1
for locations of the sleeve and diaphragm in the center valve
section.
5. Welding of the G4R valve without disassembly may be
accomplished with no damage to the sleeve and diaphragm.
Precautions MUST be taken to cool the valve bowl and
monitor temperature. The temperature of the center or bowl
area of the valve must not exceed the listed temperature for the
material. Valves, sizes two inch and smaller, must be wrapped
with water-soaked, fire-resistant material to cool the valve bowl
and inlet where the weld is to be made. Use temperature melt
crayons equal to the sleeve and diaphragm rating to mark
the body welding end and monitor the body temperature.
Thermocouples may be attached to the welding end of the
body, or surface pyrometers may be used to monitor the body
bowl temperature.
TABLE 1.1
TEMPERATURE LIMITATIONS
MAXIMUM
MATERIAL DESCRIPTION
SERVICE
TEMPERATURE
Ultra High Molecular Weight
Polyethylene (UMPE)
200°F (93°C)
Tetrafluoroethylene Polymer (PTFE)
400°F (204°C)
Durlon 2
450°F (232°C)
Duriron Durco 82 (DU-82)
275°F (135°C)
CAUTION: DO NOT ALLOW WATER FROM THE SOAKED
WRAPPING MATERIAL TO ENTER THE WELDMENT.