Actuator troubleshooting guide (electrical) – Flowserve CEA Series Limitorque Automax User Manual
Page 24
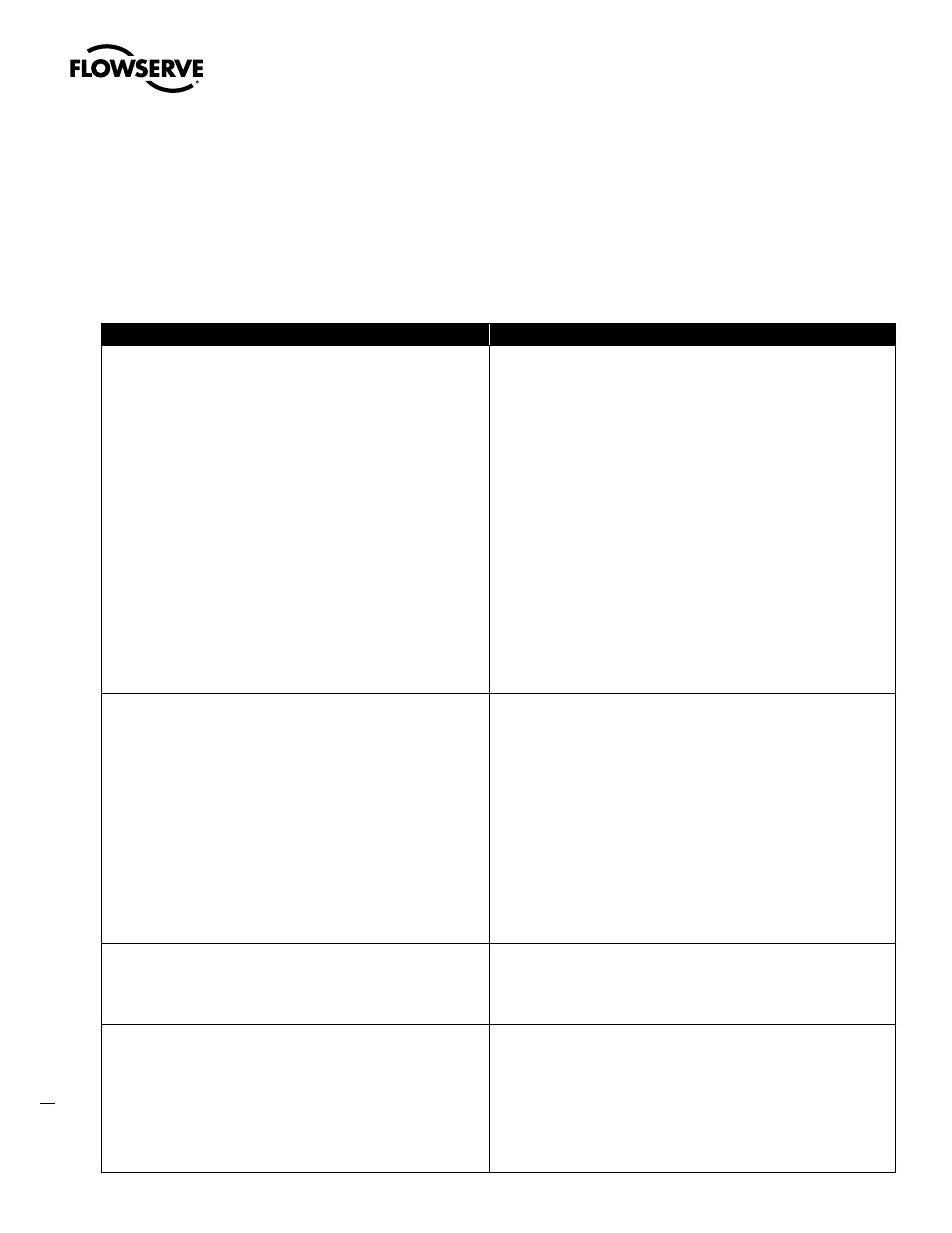
Limitorque Worcester Controls CEA Series FCD WCENIM2080-00-AQ 12/14
24
Symptom
Resolution
Actuator is commanded to move but does not move.
1.
Use hand wheel to move actuator to check for binding in valve mounting.
2.
Is there power to the actuator? Check voltage at terminals L1 and L2 must
be between 90VAC and 240VAC
3.
If a PRO unit check voltage between terminals 20 and 21 then check
voltage between terminals 20 and 22 must be between 24vdc and 240VAC
for AC models.
4.
If unit is a MOD, remove the field wires from terminals 11&12. Apply
20 mA signal using a process output meter to terminals 11 &12 noting
11 is positive and 12 is negative. Apply a 4 mA signal, if still no actuator
movement, replace main control board.
5.
Check open and closed torque setting. Change to 100% and retry step 3 or
step 4 depending on MOD or PRO unit.
6.
Check the compartment temperature and motor temperature for excessive
heat as motor controller or motor could have shut down due to excessive
heat.
7.
If unit still does not move when commanded then factory service will be
required.
NO Relay Output 1 or 2 (CW or CCW)
1.
Check physical endpoint position using hand wheel.
2.
Is there power to the actuator? Check voltage at terminals L1 and L2 must
be between 90VAC and 240VAC for AC models
3.
Remove field wiring from terminals 1 & 2 and measure continuity using a
DMM. If output is activating resistance value will be zero. Check terminals
3 & 4 in a similar fashion for output 2.
4.
Recalibrate unit and recheck. In Full CCW or Full CW output 1 or 2 should
read ZERO continuity, if not ZERO replace relay board.
5.
In the menu check for POS CCW and POS CW for output 1 and 2. If they
are not POS CCW and POS CW change accordingly.
6.
Beacon drive assembly has failed and will need to be replaced. (Factory
service recommended)
No 4-20mA output at terminals 13 and 14.
1.
Confirm model code for this option
2.
Is there 24vdc loop power on terminals 13 and 14? If so and there is still
no output on terminals 13 and 14 replace Main Control Board (MCB)
Actuator is hunting (oscillating) back and forth
1.
For C-PRO unit check voltages between terminals 20 and 21 then check
voltage between terminals 20 and 22. Is the supply voltage being com-
manded ON and OFF from the source? If not replace PMCB.
2.
For C-MOD unit check that deadband setting is not set below 0.1%
3.
If unit is still oscillating replace encoder board and then recalibrate using
autocal.
4.
Beacon drive assembly has failed (factory service recommended)
7. Actuator Troubleshooting Guide
(Electrical)
The actuator contains (5) five electrical devices, a 3 phase BLDC
motor, Motor Controller, Main Control Board, Relay Board and a 12 bit
Rotary Encoder Board. This is an electro-mechanical device and will,
after many years of service, require inspection of mechanical compo-
nents to ensure the root cause is not hidden there.
The actuator main position control is derived from the 12 bit magnetic
rotary encoder. The actuator will be calibrated from the factory but if
for any reason field service is performed on the actuator e.g. travel
stop adjustment or board replacement, the actuator will
require recalibration.
Before replacing any parts always check for loose field wiring at the
terminal block. This usually solves most known issues with the actua-
tor. If no loose wiring is found proceed below.