Iii. assembly, Worcester controls – Flowserve 90 Series Modular Accessory System User Manual
Page 5
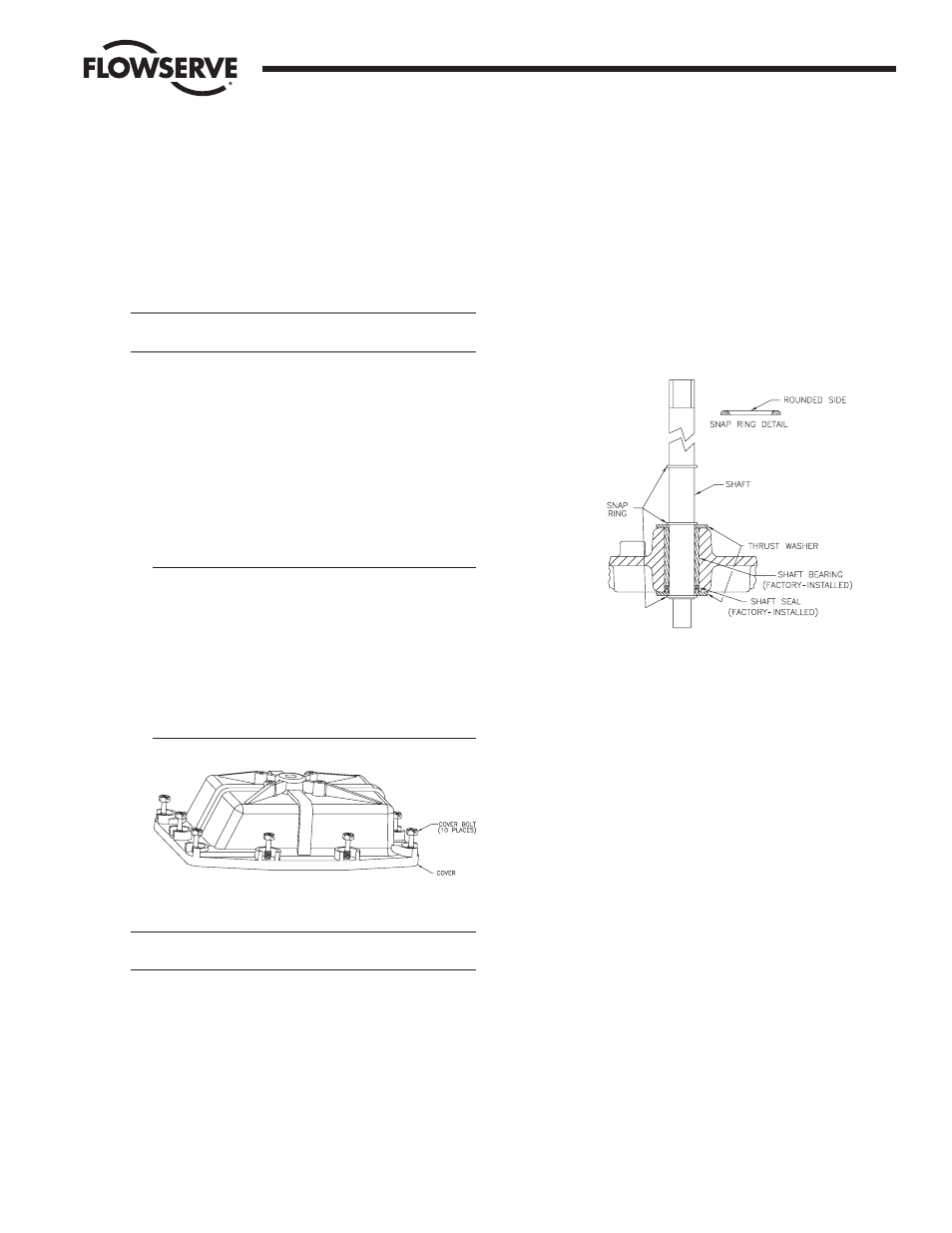
07334-F
Modular Accessory System (Series 90)
5
III. ASSEMBLY
A. Housing Assembly
The housing consists of the base, cover, shaft, baseplate, and
associated hardware. The housing is assembled as received from
Flowserve. For ease of maintenance, assembly instructions will be
provided here.
1. Cover
CAUTION: Use care to avoid damaging the machined flange
surface of the cover.
a. Apply a light coat of Cindal 2321 lubricant (or other
bearing grease) to the shaft hole.
b. Assemble the captive type cover screws through the
flange holes. The screws must be turned through approx.
¹⁄₄" of thread until they reach the clearance diameter and
remain loose in the cover. Use caution to avoid cross-
threading these screws. Refer to Figure 5.
c. Check to see that the shaft seal has been installed as
shown in Figure 6.
CAUTION: When assembling cover to base, be sure
wires are away from any rotating parts and are not
pinched between cover and base flanges.
Relubricate the shaft hole anytime cover is removed
and replaced.
To avoid damaging the cover hole finish and binding the
shaft to cover, check the top of the shaft for burrs or
impact damage before installing or removing cover.
2. Base
CAUTION: Use care to avoid damaging the machined flange
surface of the base.
a. Check to see that the shaft seal and bearing have been
installed as shown in Figure 6.
b. Apply a light coat of bearing lubricant to the shaft hole.
c. Insert the shaft through the shaft hole in the base from
the inside. The shaft fits through this hole with minimal
clearance — care must be taken to avoid damaging the
bearing surfaces or causing the shaft to gall.
d. Place one of the nylon thrust washers onto the shaft end
protruding outside the base. Assemble one of the snap
rings to the shaft in the groove below this thrust washer
(rounded side towards thrust washer – see detail).
e. Place a second nylon thrust washer over the shaft and
into place against the shaft boss on the inside of the
base. Secure the shaft in place with a second snap ring in
the groove adjacent to the second thrust washer (rounded
side towards thrust washer – see detail).
f.
Place the third snap ring into the upper groove as shown
in Figure 6.
g. If the base is machined to accept a Breather/Drain fitting
as shown in Figure 7, then the boss on the bottom of the
base near the electrical conduit connection bosses will be
tapped with
³ ₈" NPT threads. If this boss is tapped, the
Breather/Drain fitting must be installed. The use of
fluoropolymer tape or other thread sealant is
recommended prior to installing this fitting into the boss.
h. Plug the
³ ₄" NPT conduit connection on the end of the
base temporarily with the threaded plastic plug provided.
This plug will be removed and discarded when the unit is
installed.
i.
Plug the (4)
¹ ₄" NPT and (1) ¹ ₈" NPT air connection ports
with the stainless steel pipe plugs provided. Thread
sealant is not recommended prior to installing these
plugs. The residue left by a thread sealing compound
could foul the solenoid valve air passages. If a solenoid
valve option is to be installed in the unit, some of these
plugs will not be used – refer to the Solenoid Block
Installation Instructions to determine which plugs can be
left out.
IMPORTANT: If no solenoid is to be used, all of the ports
must be plugged. Refer to Figure 7.
j.
The M.A.S. uses a standard O-ring to achieve both
Watertight (TYPE 4) and Explosion-proof – (TYPE 7)
ratings. Refer to Figure 8.
Flow Control Division
Worcester Controls
Figure 5
Figure 6