Data communications, Address setting, Relay - contact outputs – GAI-Tronics 379-002 Monitored RElay Module (MRM) Stations User Manual
Page 4
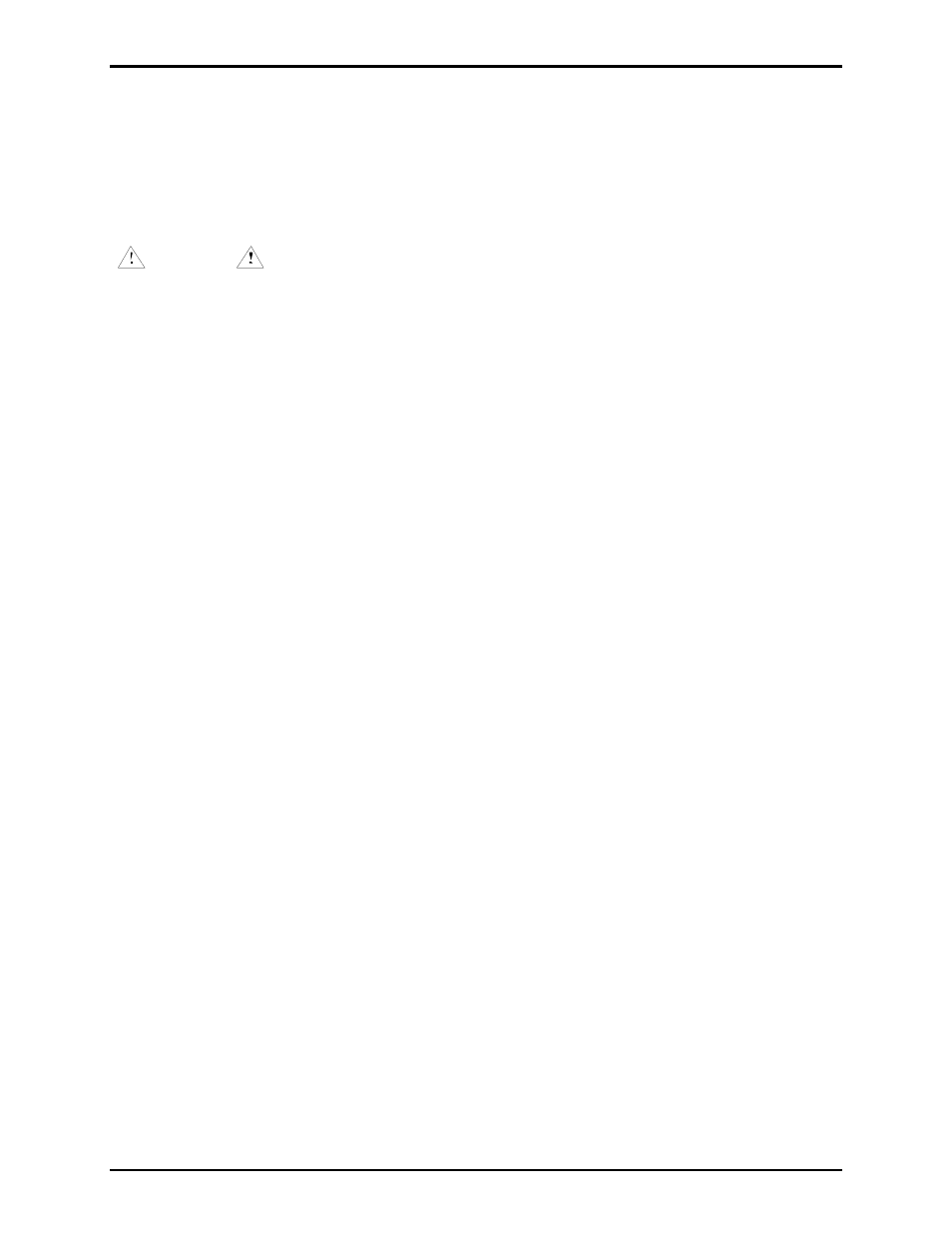
Pub. 42004-491A
Model 379-002 Monitored Relay Module Station
Page 4 of 13
f:\standard ioms - current release\42004 instr. manuals\42004-491a.doc
03/14
Data Communications
Terminal blocks TB11 and TB12 are for “feed-thru” connection of the RS-485 data cable. The data cable
should consist of a twisted pair with shield. One end of the data cable must be terminated to the
ADVANCE System Control Cabinet. A total of ten MR M and MIM modules can be parallel wired to
the data cable. The most distant MRM or MIM should have a termination resistor installed to the data
line by installing jumper P2 on the 69248-xxx CPU PCBA.
CAUTION
The RS-485 line is polarity-sensitive. Be sure to maintain circuit polarity throughout installation.
N
OTES
:
Only one termination resistor should be installed across the RS-485 data line. Be sure jumper P2 is
installed on only the most distant MRM or MIM.
Address Setting
Each MRM and MIM on the RS-485 data line must be set with a unique hardware address. Consult the
System Administrator for the proper address prior to setting the address switch on the MRM or MIM.
Addresses for each module are determined by the System Administrator’s software configuration of the
ADVANCE system. The address is set using the hexadecimal switch on the 69248-xxx CPU PCBA.
Valid addresses are 5–F.
Relay - Contact Outputs
The MRM contains eight individually configurable relay-contact outputs, allowing it to control field
devices such as beacons. Connections with these field devices are made at connectors TB1 through TB8
of the 69252-xxx Power Relay Module.
Each connector corresponds to a single output (TB1 is used for output #1, TB2 is used for output #2, etc.).
If fewer than eight supervised relay-contact outputs are required, the unused outputs may be used to
receive inputs (dry contact closures or non-supervised 24 V dc wet contact closures) from field devices.
In this case, connections with these field devices are made at connectors TB1 through TB8 of the 69251-
xxx Monitored-In-8 PCBA. Each of these outputs may be configured to operate in one of six modes.
Two of these six modes are used to control signaling devices, while the remaining four modes are used to
receive inputs (contact closures) from field devices.
Each mode requires a unique connection scheme between the external field devices and the appropriate
connector on the MRM. The connection scheme for each mode is described below. Since the connection
scheme is independent of which output is used, only Output #1 will be discussed.
To ensure proper termination, ferrules must be crimped on the ends of all conductors that are terminated
on the terminal blocks. The size of the ferrule is dependent upon the size of the conductor used and can
be sourced from any supplier such as Phoenix, Altec or Weidmuller. The terminals accept a maximum
conductor size of No. 12 AWG and a minimum conductor size of No. 28 AWG.