Infloor Infloorboard II User Manual
Page 3
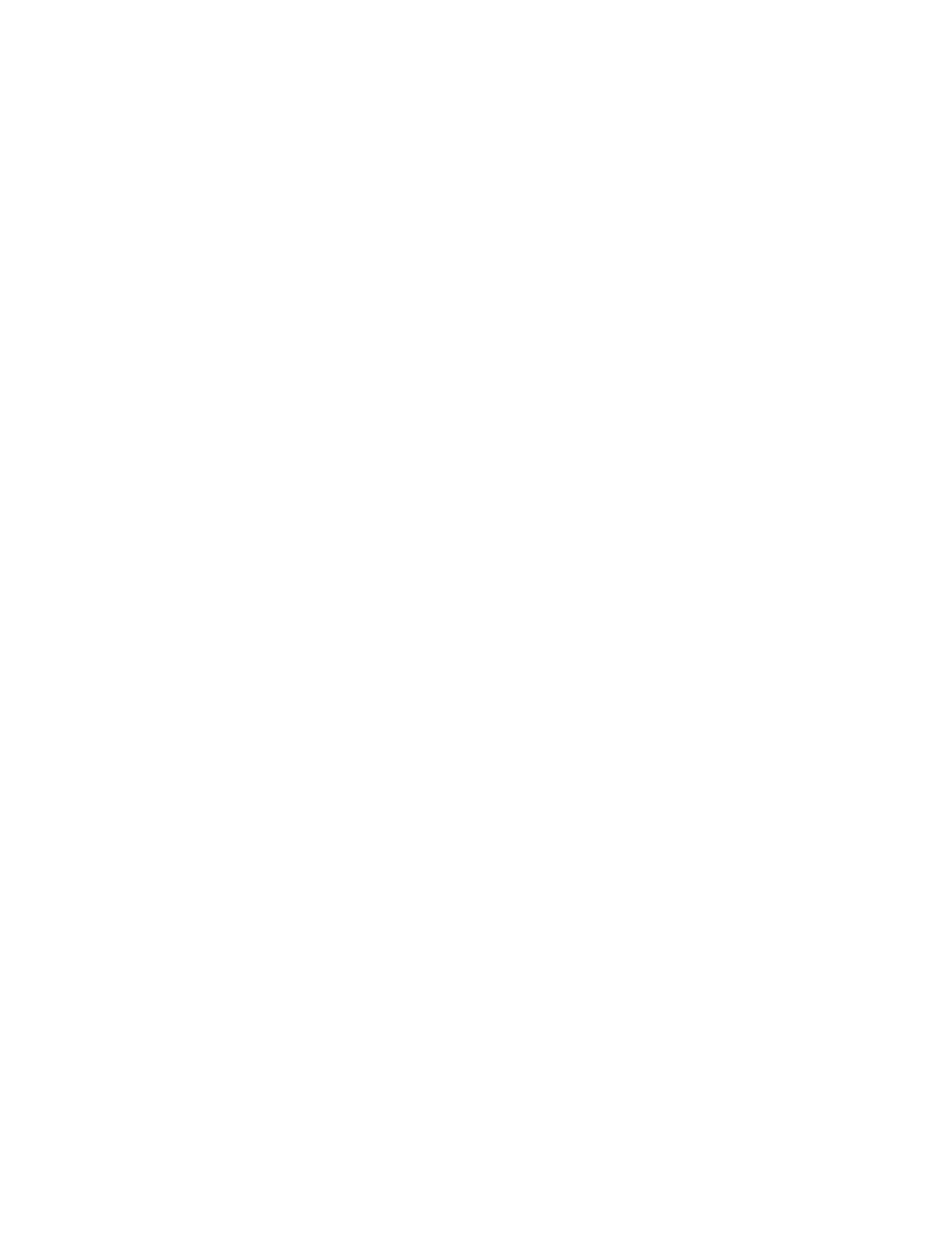
3
InfloorBoard II™ & PEX Tubing
Requirements
InfloorBoard II™: To estimate the number of
boards needed, divide the square footage of the
area by 4 (each board is 4sq.ft.). Example: A
20ft. X 20ft. room = 400sq.ft., dividing 400 by 4
= 100 boards. For standard room configura-
tions, (square, rectangle) include 5% additional
boards to allow for waste. For rooms with an-
gled walls, multiple corners, or bump outs, in-
clude 10% additional boards.
Tubing: InfloorBoard II™ is designed to secure
3/8” ASTM F876 PEX tubing. Based upon the
InfloorBoard II™ provided 8” on center spacing
a tubing factor of 1.5 should be used. To deter-
mine the required amount of tubing, multiply the
square footage of the area by 1.5. The result is
the amount of tubing required to be installed
into the boards. In addition, supply/return leader
lengths must also be added depending upon
the manifold/system connection location.
Where required heat outputs are 25 BtuH/ft² or
greater, circuit lengths should be limited to
aproximately 200ft. (including supply/return
leaders). For heat outputs less than 25 BtuH/ft²,
circuit lengths should be designed around 250ft.
Number of Circuits: To determine the number
of individual circuits of tubing required, subtract
the supply/return leader length from the desired
total circuit length (200ft, 250ft.). Divide the
resulting circuit length into the total calculated
tubing requirement (sq.ft. x 1.5) to determine
the number of circuits for the project. Example:
250ft. circuits minus a 25ft. supply and 25ft.
return leader (50ft.) = 200ft. The total calculated
tubing requirement is known to be 1200ft. (an
800sq.ft. area x 1.5). Divide 1200 by 200 to
determine 6 circuits will be required.
Equipment Required
The following are recommended for the
installation of InfloorBoard II™:
•
Table or skill saw with a high quality carbide
or better blade.
•
Drill Gun (electric or cordless) with No. 2
Phillips bit.
•
3/4” drill bit for supply/return leader access
locations.
•
Screws (min. 1-1/4”).
•
Rubber or similar soft mallet.
•
Chalk line
•
Carpenter Square
•
Short (aprox. 6”) lengths of 3/8” PEX Tubing
for board groove alignment.
•
Vacuum cleaner for subfloor and groove
preparation.
Subfloor Preparation
All subfloors must be structurally sound, level,
and free of voids or defects. High and/or low
spots must be addressed prior to board
installation. Sags and/or creaking may be signs
of a larger problem. These, and all, structural
deficiencies will need to be repaired in order to
assure satisfactory board installation. The
entire floor area should be swept and
vacuumed prior to installation.
Moisture Content: The moisture resistant
properties of InfloorBoard II™ provides greatly
increased resiliance to the damaging effects of
moisture and humidity over standard wood
products. However, excessive or continual
moisture can cause adverse effects on
subfoors, framing, finish flooring and, if left
uncorrected, eventually to InfloorBoard II™.
Wood subfloors should have a stable moisture
content below 10% before board installation.
Due to environmental, shipping, and storage
conditions, InfloorBoard II™ should be placed in
the room that it is to be installed and allowed to
acclimate to the environment (48-72 hrs.). It
should be maintained at the same temperature
(>50˚F) and have a moisture content within 4%
of that of the subfloor. This also holds true for
any finish wood flooring that is to be installed
over InfloorBoard II™.
Concrete slabs will require special
consideration. All slabs will release moisture
regardless of their location (below, above, or on
grade). In most cases, for new slabs, it will take
60 days or more before the slab is dry enough
(cured) to proceed. After fully curing, moisture
levels should be checked. Due to the specific
procedures for properly testing concrete
moisture content, and that slab moisture
conditions can change as environmental
conditions change, testing should be done by
an experienced professional. If using a calcium
chloride moisture test, the allowable amount of
moisture emission is 3.0 pounds per 1000sq.ft.
per 24 hours. If moisture conditions are
questionable or inconsistent, slabs should be
sealed with an appropriate moisture barrier.