Yaskawa F7 Drive Enhanced PID for Air Compressor User Manual
Page 11
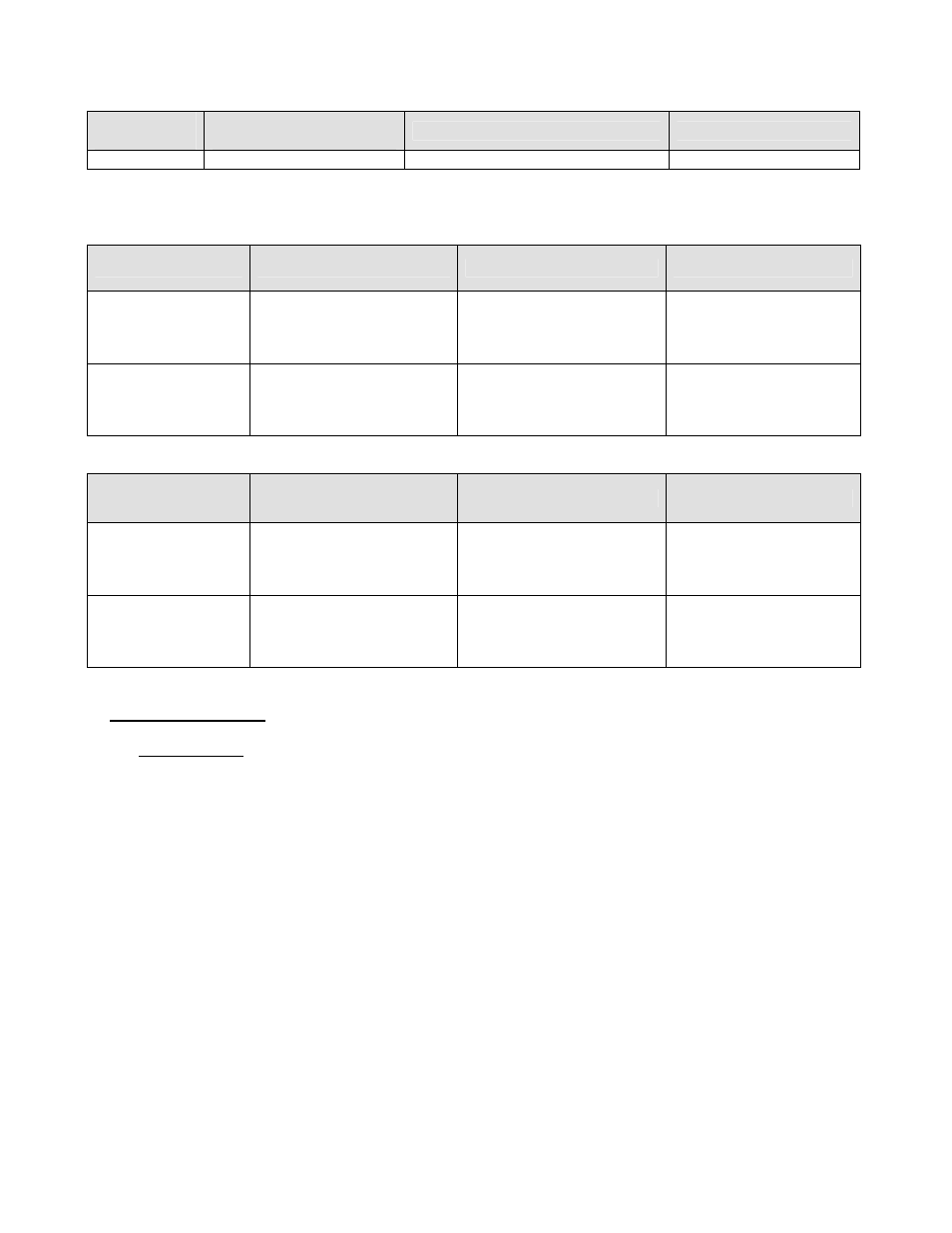
Date: 08/01/05, Rev: 05-08
Page 11 of 17
TM.F7SW.096
4.5 Modbus Registers
Modbus
Address
Monitor
Name
Description
Unit
024H
Output Frequency
Output frequency monitor
0.01Hz *4
*4: Scaling based on P2-10 (Output Monitor Units) setting. Parameter P2-10 programs and functions exactly like
standard parameter O1-03.
4.6 Faults
Fault Display
Description
Cause
Countermeasures
FRH
Feedback Range
High
PID feedback out of range
(high). Motor will coast to a
stop.
P1-01 = 4 or 5 and the PID
feedback has exceeded the
P1-02 level for the time set
in P1-03.
Correct the cause of the
high feedback signal.
FRL
Feedback Range
Low
PID feedback out of range
(low). Motor will coast to a
stop.
P1-01 = 4 or 5 and the PID
feedback has fallen below
the P1-05 level for the time
set in P1-06.
Correct the cause of the
low feedback signal.
4.7 Alarms
Alarm Display
Description
Cause
Countermeasures
FRH
Feedback Range
High
PID feedback out of range
(high)
P1-01 = 2 or 3 and the PID
feedback has exceeded the
P1-02 level for the time set
in P1-03.
Correct the cause of the
high feedback signal.
FRL
Feedback Range
Low
PID feedback out of range
(low)
P1-01 = 2 or 3 and the PID
feedback has fallen below
the P1-05 level for the time
set in P1-06.
Correct the cause of the
low feedback signal.
5.0 Function Description
5.1 Enhanced PID
The Enhanced PID feature includes many enhancements over the drive’s standard PID function. The PID
algorithm is programmed using the existing B5 group of parameters as well as the P group of parameters.
See Section 2.0 for details. Enhanced features include:
• The ramp in the PID setpoint behaves differently depending upon the PID mode and the reference
source. In most cases, the PID setpoint ramp affects only the PID setpoint. When the PID + Trim feature
is enabled (B5-01 = 3 or 4) and there is no independent PID setpoint, the PID ramp affects both the PID
setpoint and the frequency reference.
• The PID output is now algebraically summed with the frequency reference. Motor rotation will be forward
if: a forward run is commanded and there is a positive PID + trim, or if a reverse run is commanded and
there is a negative PID + trim. Motor rotation will be reverse if: a reverse run is commanded and there is
a positive PID + trim, or if a forward run is commanded and there is a negative PID + trim.
• The integral time is lower-limited to the to the PID minimum output limit (P2-01). The integrator is also
held during the sleep mode, and the sleep minimum off time. These changes were done to prevent
integrator windup and insure smooth starts with a minimum of pressure overshoot.