0 performance optimization – Interlink Electronics FSR 400 Series User Manual
Page 30
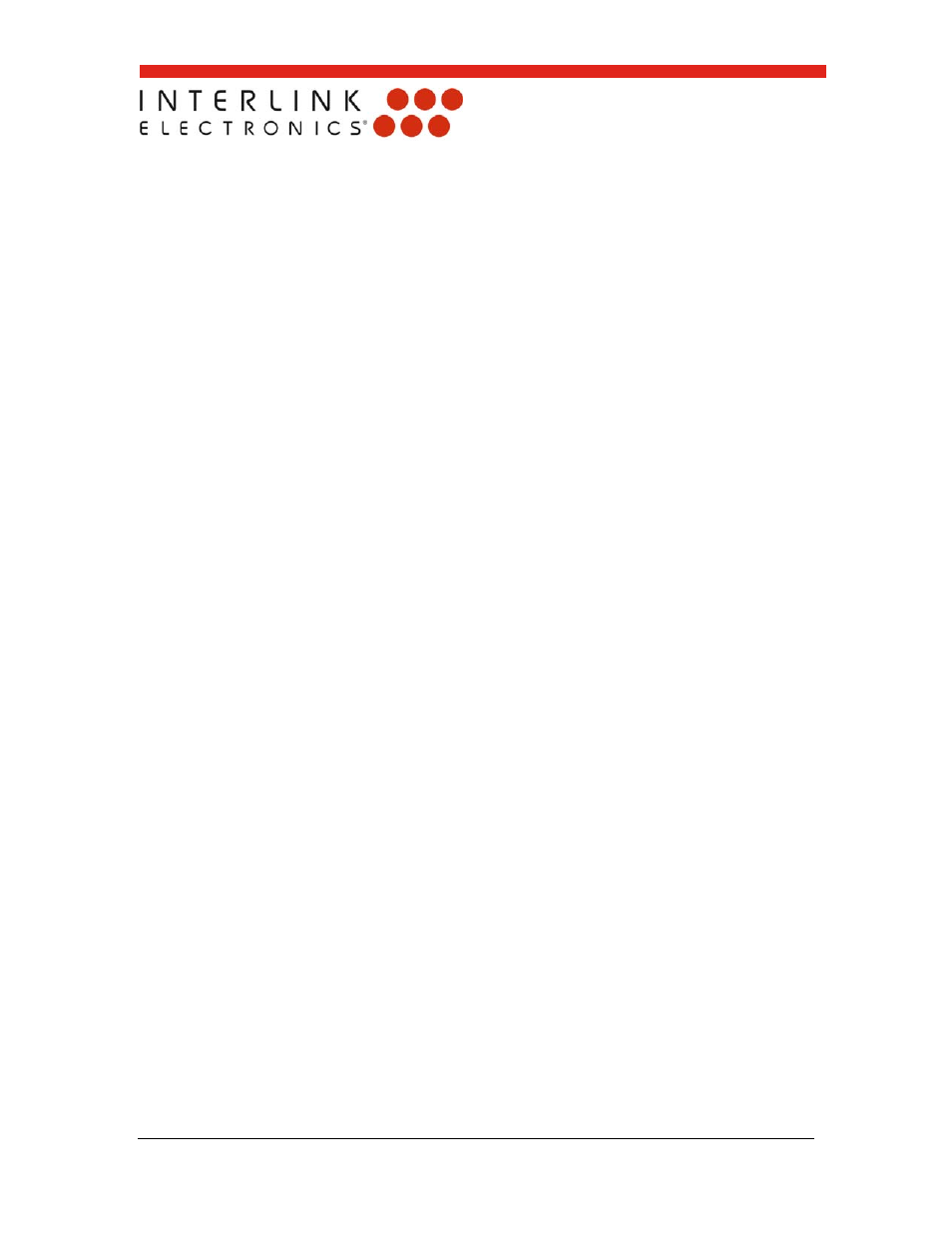
www.interlinkelectronics.com
28
FSR
®
Integration Guide
7.0 Performance
Optimization
For best results, follow these seven steps when beginning any new product design,
proof-of-concept, technology evaluation, or first prototype implementation:
1. Start with Reasonable Expectations (Know Your Sensor)
The FSR sensor is not a strain gauge, load cell, or pressure transducer. While it can be
used for dynamic measurement, only qualitative results are generally obtainable. Force
accuracy ranges from approximately ± 6% to ± 50% depending on the consistency of the
measurement and actuation system, the repeatability tolerance held in manufacturing,
and the extremes of the environment.
2. Choose the Sensor that Best Fits the Geometry of Your Application
Usually sensor size and shape are the limiting parameters in FSR integration, so any
evaluation part should be chosen to fit the desired mechanical actuation system. In
general, standard FSR products have a common response and only by varying actuation
methods (e.g. overlays and actuator areas) or electrical interfaces can different response
characteristics be achieved.
3. Set-up a Repeatable and Reproducible Mechanical Actuation System
When designing the actuation mechanics, follow these guidelines to achieve the best
force repeatability:
Provide a consistent force distribution. FSR response is very sensitive to the
distribution of the applied force. In general, this precludes the use of dead weights for
characterization since exact duplication of the weight location is rarely repeatable
cycle-to-cycle. A consistent weight (force) distribution is more difficult to achieve than
merely obtaining a consistent total applied weight (force). As long as the distribution
is the same cycle-to-cycle, then repeatability will be maximized. The use of a thin
elastomer between the applied force and the FSR can help absorb error from
inconsistent force distributions.
Keep the actuator area, shape, and material properties consistent. Changes in these
parameters significantly alter the response of a given sensor. Any test, mock-up, or
evaluation conditions should be closely matched to the final use conditions. The
greater the cycle-to-cycle consistency of these parameters, the greater the device
repeatability. In human interface applications where a finger is the mode of actuation,
perfect control of these parameters is not generally possible. However, human
perception of force is somewhat inaccurate so these applications may be more
forgiving.
Control actuator placement. In cases where the actuator is to be smaller than the
FSR active area, cycle-to-cycle consistency of actuator placement is necessary.
(Caution: an adhesive that surrounds the electrically active areas holds FSR layers
together. If force is applied over an area that includes the adhesive, the resulting
response characteristic will be drastically altered.) In an extreme case (e.g., a large,
flat, hard actuator that bridges the bordering adhesive), the adhesive can prevent
FSR actuation.