Interlink Electronics FSR 400 Series User Manual
Page 31
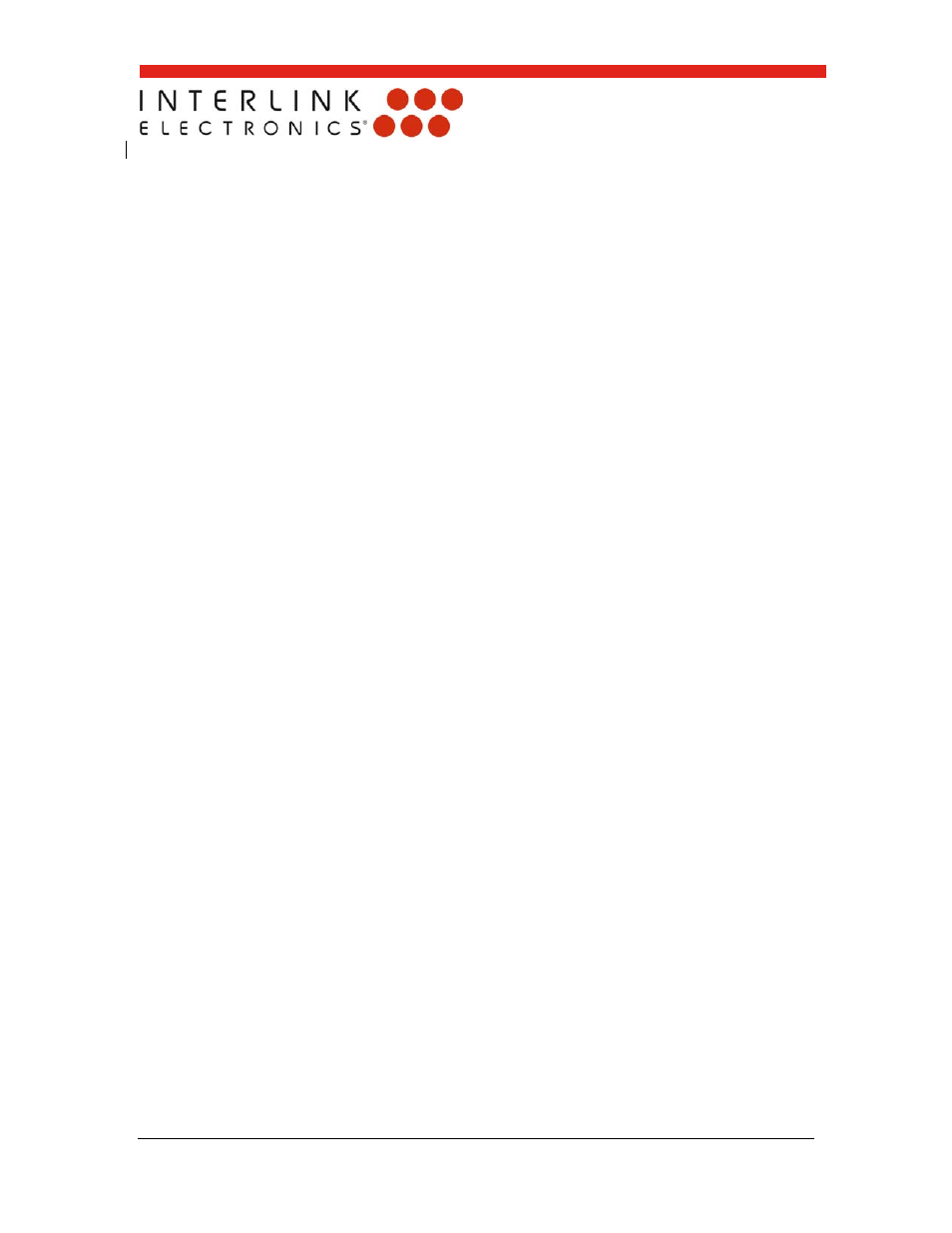
www.interlinkelectronics.com
29
FSR
®
Integration Guide
Keep actuation cycle time consistent. Because of the time dependence of the FSR
resistance to an applied force (drift), it is important when characterizing the sensor
system to assure that increasing loads (e.g. force ramps) are applied at consistent
rates (cycle-to-cycle). Likewise, static force measurements must take into account
FSR mechanical setting time. This time is dependent on the mechanics of actuation
and the amount of force applied and is usually on the order of seconds.
4. Use the Optimal Electronic Interface
In most product designs, the critical characteristic is Force vs. Output Voltage, which is
controlled by the choice of interface electronics. A variety of interface solutions are
detailed in the Measurement Techniques section of this guide. Summarized here are
some suggested circuits for common FSR applications:
For FSR Pressure or Force Switches, use the simple interfaces detailed on page 20.
For dynamic FSR measurements or Variable Controls, a current-to-voltage converter
(see page 21) is recommended. This circuit produces an output voltage that is
inversely proportional to FSR resistance. Since the FSR resistance is roughly
inversely proportional to applied force, the end result is a direct proportionality
between force and voltage; in other words, this circuit gives roughly linear increases
in output voltage for increases in applied force. This linearization of the response
optimizes the resolution and simplifies data interpretation.
5. Develop a Nominal Voltage Curve and Error Spread
When a repeatable and reproducible system has been established, data from a group of
FSR parts can be collected. Test several FSR parts in the system. Record the output
voltage at various pre-selected force points throughout the range of interest. Once a
family of curves is obtained, a nominal force vs. output voltage curve and the total force
accuracy of the system can be determined.
6. Use Part Calibration if Greater Accuracy is Required
For applications requiring the highest obtainable force accuracy, part calibration will be
necessary. Two methods can be utilized: gain and offset trimming, and curve fitting.
Gain and offset trimming can be used as a simple method of calibration. The
reference voltage and feedback resistor of the current-to-voltage converter are
adjusted for each FSR to pull their responses closer to the nominal curve.
Curve fitting is the most complete calibration method. A parametric curve fit is done
for the nominal curve of a set of FSR devices, and the resultant equation is stored for
future use. Fit parameters are then established for each individual FSR (or sending
element in an array) in the set. These parameters, along with the measured sensor
resistance (or voltage), are inserted into the equation to obtain the force reading. If
needed, temperature compensation can also be included in the equation.
7. Refine the System
False results can normally be traced to sensor error or system error. If you have any
questions, contact Interlink Electronics’ Sales Engineer to discuss your system and final
data.