Flowserve HWX Worthington User Manual
Page 27
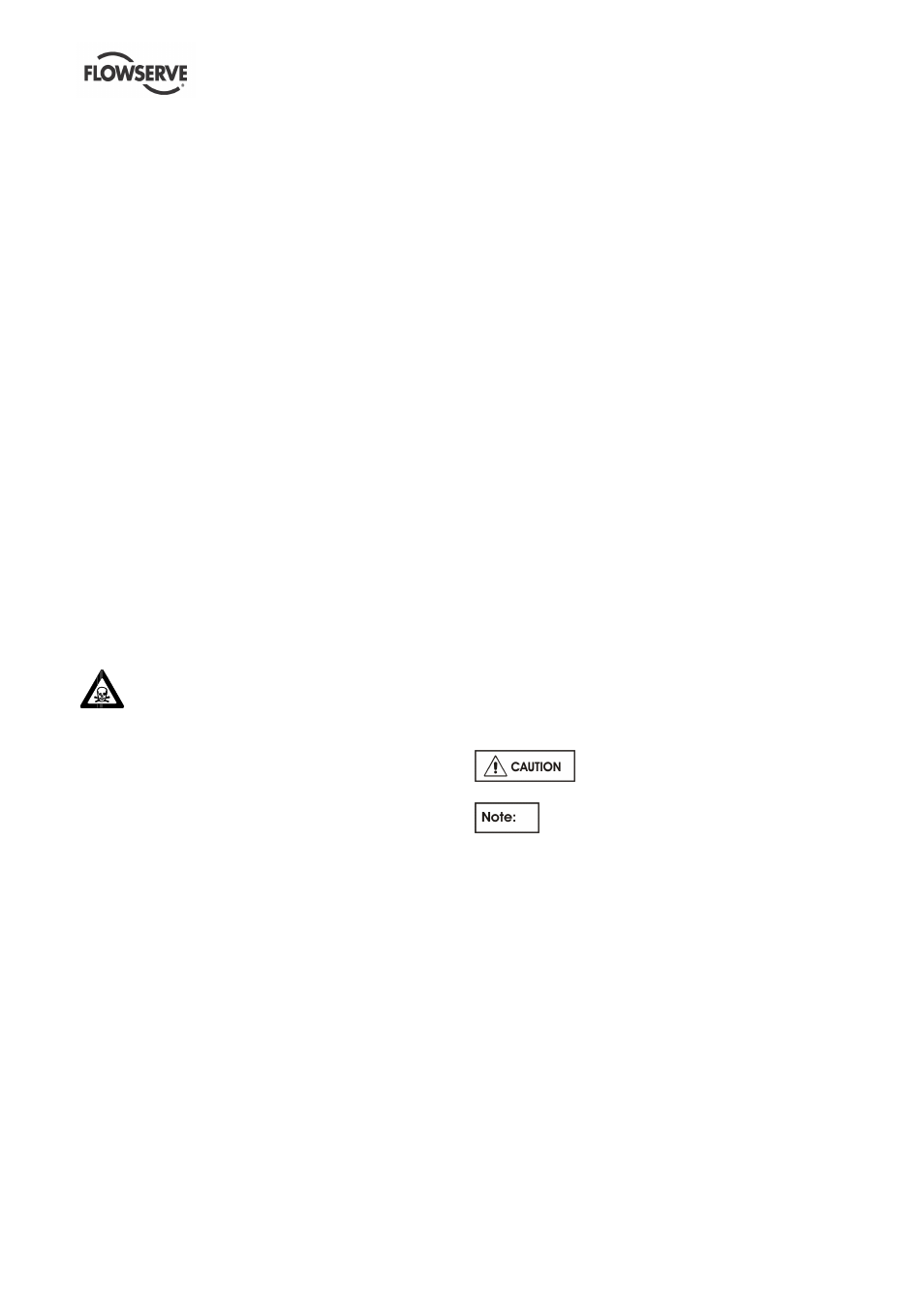
HWX USER INSTRUCTIONS ENGLISH - 07/14
Page 27 of 40
In particular, fault diagnosis is essential to
enhance pump and plant reliability.
To perform a good visual inspection and to obtain the
highest degree of cleanliness, which is essential to
the correct fit and balance of all rotating parts, the
shaft must be stripped of all parts. The visual
inspection consists of examining the following parts
for those conditions that commonly impair pump
operation. Where the corrective action may not be
apparent to a journeyman millwright or a more
extensive examination is required, the inspection item
is cross-referenced to a detailed procedure. Unless
noted below, all damaged parts should be replaced
rather than repaired.
6.7.1 Cleaning Agents
When the pump is used in the steam generator feed,
the boiler feed, the reactor feed, or other such steam
(or water) circuit, all internal metal parts of the pump
including the case should be cleaned with a non-
petroleum-base cleaning agent such as alcohol or
acetone or a steam cleaner that uses steam from
demineralised water. The basic concern should be to
insure that the solvent is compatible with the
pumpage. Petroleum-base agents such as dry
cleaning solvent and kerosene may be used for
cleaning internal parts when such agent will dissolve
in the liquid being pumped without inducing an ill
effect. Petroleum-base agents should be used to
clean the bearings and their housings.
Fumes from alcohol, acetone, petroleum
solvents and other such chemicals are injurious
to health and may ignite from a spark; make
certain that the area where they are used is well
ventilated and have a fire extinguisher handy.
6.7.2 Casing, seal housing and impeller
a) Inspect for erosion, foreign object damage and
cracks; erosion and damage must be corrected
before final assembly.
b) Inspect impeller cap nut [2912] and impeller
[2200] for nicks, gouges, galling and rust.
c) Inspect impeller bore for correct fit with shaft (See
Section 6.8.2 ”Checking Fit Between Impeller
Bore and Shaft”).
d) Inspect running surfaces of stuffing box bushing
[4133], shaft [2100], case wear ring [1500.1],
casing cover wear ring [1500.2], and impeller
wear ring [2300.1–2300.2] for nicks, burrs,
scratches, scouring and excessive wear.
Concentric and smooth surfaces are required
(See Section 6.8.1 “Wear Rings”).
e) Replace as necessary.
6.7.3 Mechanical seal
a) Mechanical seal stationary and rotating faces
should be inspected for signs of wear or cracks
and replaced as necessary.
b) It is recommended that when reassembling
mechanical seal new "O" rings and gaskets be
used.
c) Refer to manufacturers drawing for assembly of
mechanical seal. Refer to mechanical seal
section within this manual for further details.
6.7.4 Throat Bush (If fitted)
a) Check the throat bush and replace if required.
Note that the bush outside diameter should be
the same diameter as the adjacent impeller wear
ring.
6.7.5 Shaft
Shaft [2100] for scratches, nicks, burrs, and
distortion; absolutely smooth surfaces and a straight
shaft are required.
After the shaft is inspected for damage as described
above, it must be checked for straightness before
reassembling the rotating parts. When making the
check do not turn the shaft in its lathe centers. It is
possible for the lathe centers of a straight shaft to be
off center slightly, resulting in a false indication of a
bent shaft.
1. Set shaft in soft-faced V-blocks, precision rollers
(or equivalent).
2. Check straightness by taking dial indicator
readings all along the shaft while it is rotated; total
runout of shaft must not exceed 0.04 mm (0.0015
in). If runout is exceeded shaft must be cold-
straightened or replaced.
Application of heat to straighten
shaft will cause more distortion.
The term "soft-faced V-blocks" refers to
V-blocks faced with metal that is softer than the
shaft, for example, V-blocks faced with copper.
6.7.6 Gaskets and O-rings
After dismantling, discard and replace.
6.7.7 Bearings
a) It is recommended that bearings are not re-used
after any removal from the shaft. In any case the
bearings must be replaced not after 25000
operating hours.
b) If the bearing cannot be removed with the tools
available never use a torch under any
circumstances. Split the outer ring with a small
hand grinder, saw through the ball/roller retainer,
and split the inner ring about three quarters
through with a grinder and break with a cold steel
chisel.