2 changing of mechanical seal – Flowserve HWX Worthington User Manual
Page 34
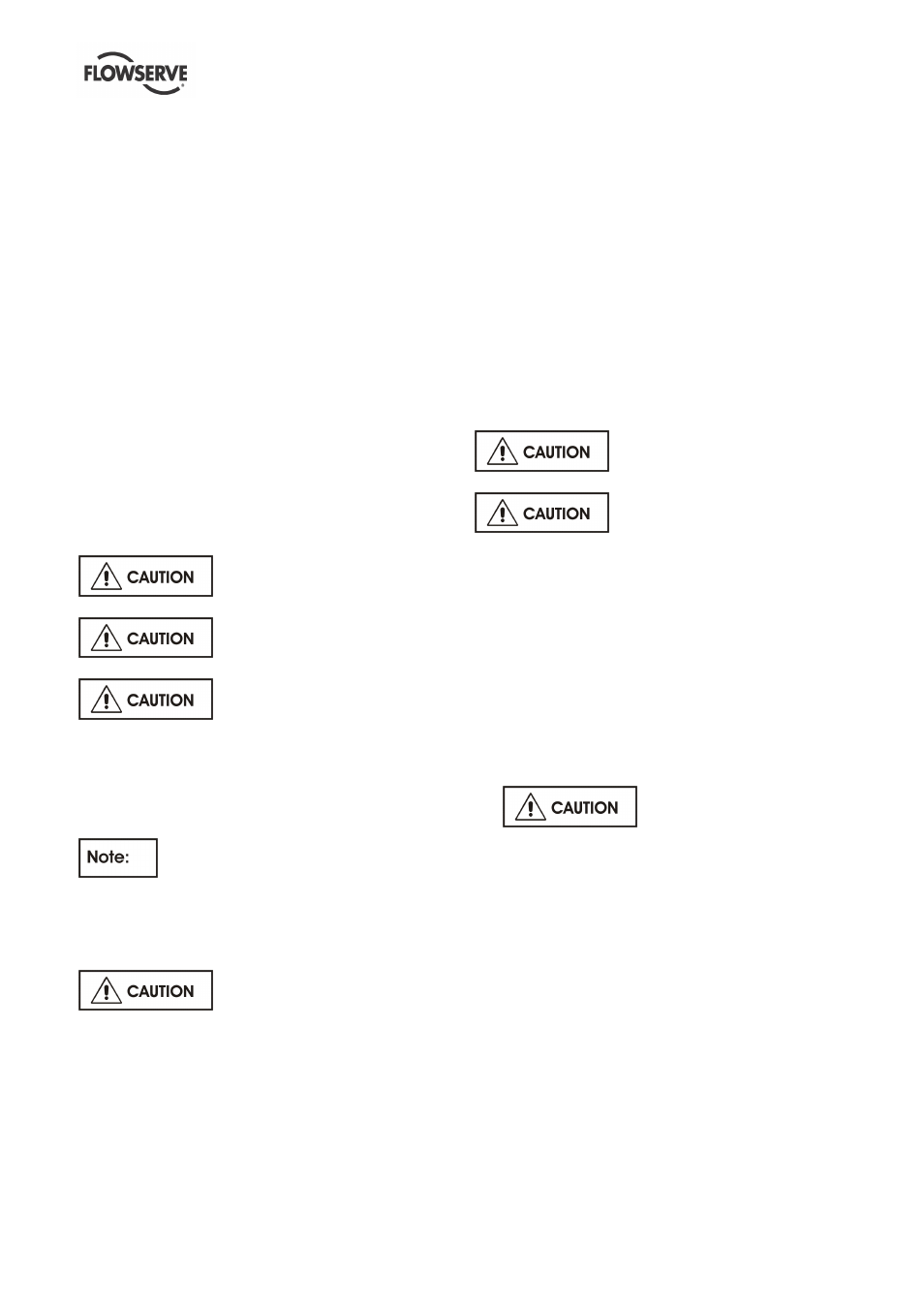
HWX USER INSTRUCTIONS ENGLISH - 07/14
Page 34 of 40
Plan 02 is a dead ended seal chamber with no flush
fluid circulation. Flushing is not necessary because
the seal is not exposed to the pumped liquid.
Plan 53 pressurized dual seal systems are used in
services where no leakage to atmosphere can be
tolerated. A Plan 53b system consists of dual
mechanical seals with a liquid barrier fluid between
them. The barrier fluid is contained in a seal pot and
is pressurized by using a bladder type accumulator.
Inner seal leakage will be barrier fluid leakage into
the product. There will always be some leakage
(max.5 ml/hour).
The leakage rate is monitored by monitoring the seal
pot level. The product must be able to accommodate
a small amount of contamination from the barrier
fluid. The seal pot pressure must be maintained at
the proper level. If the seal pot pressure drops, the
system will begin to operate like a Plan 52, or
unpressurized dual seal, which does not offer the
same level of sealing integrity. Specifically, the inner
seal leakage direction will be reversed and the barrier
fluid will, over time, become contaminated with the
process fluid with the problems that result, including
possible seal failure.
Fill the seal system with a suitable
barrier buffer fluid (refer to lubrication table).
Open all necessary valves in the
cooling and auxiliary piping and check the flow.
Disassembly of the seal cartridge
is only allowed by authorized personal. Contact
Flowserve for any service of the mechanical seal. We
recommend to have a spare cartridge seal on stock
for easy replacement.
7.1.4 Single Mechanical Seal with API–Plan 13+61
Refer to mechanical seal drawing and
auxiliary piping drawing.
The pump is equipped with a single mechanical seal.
The cartridge design allows to change the
mechanical seal without taking it apart.
Try to turn the rotor by hand.If the
rotor cannot be turned, the pump must be
disassembled, refer to section 6.6 Dismantling HWX.
Actions after start up:
Check all connections to the seal gland and the
mechanical seal itself against leakage. It is usual that
at the seal faces a small leakage occurs after start
up, which decreases with the time of operation and
should stop after the seal is run in. Check the
temperature of the seal gland. I slight increase of
temperature may be observed during the run in
period. The mechanical seal is flushed by an API
Plan 13 and the temperature at the seal gland should
be max. 10 °C (18 °F) above the pumped liquid
temperature, unless otherwise specified by
mechanical seal supplier.
In API Plan 13 product is routed from the seal
chamber back to the pump suction to provide cooling
for the seal and to vent air or vapors from the seal
chamber. The seal chamber is subjected to discharge
pressure.
API Plan 61 has tapped and plugged connections for
the purchaser´s use. Typically this plan is used when
the purchaser is to provide fluid (such as steam, gas, or
water) to an external sealing device.
Refer to the GA - drawing for the
required quench medium, pressure and flow.
Disassembly of the seal cartridge
is only allowed by authorized personal. Contact
Flowserve for any service of the mechanical seal. We
recommend to have a spare cartridge seal on stock
for easy replacement.
7.2 Changing of mechanical seal
1) Completely drain the pump by using the drain
connection. By pumping explosive or toxic media,
flush the system with Nitrogen.
2) Secure the mechanical seal by putting the
mounting plates into the groove of the shaft
sleeve [2450]. Loose the grub screws [6814.4],
and disconnect the seal piping.
Drain the seal system, if
applicable.
3) For disassembly refer to section 6.6, Dismantling
of pump.
4) For assembly refer to section 6.8, Assembly of
pump.