5 protection systems – Flowserve MENBLOC User Manual
Page 20
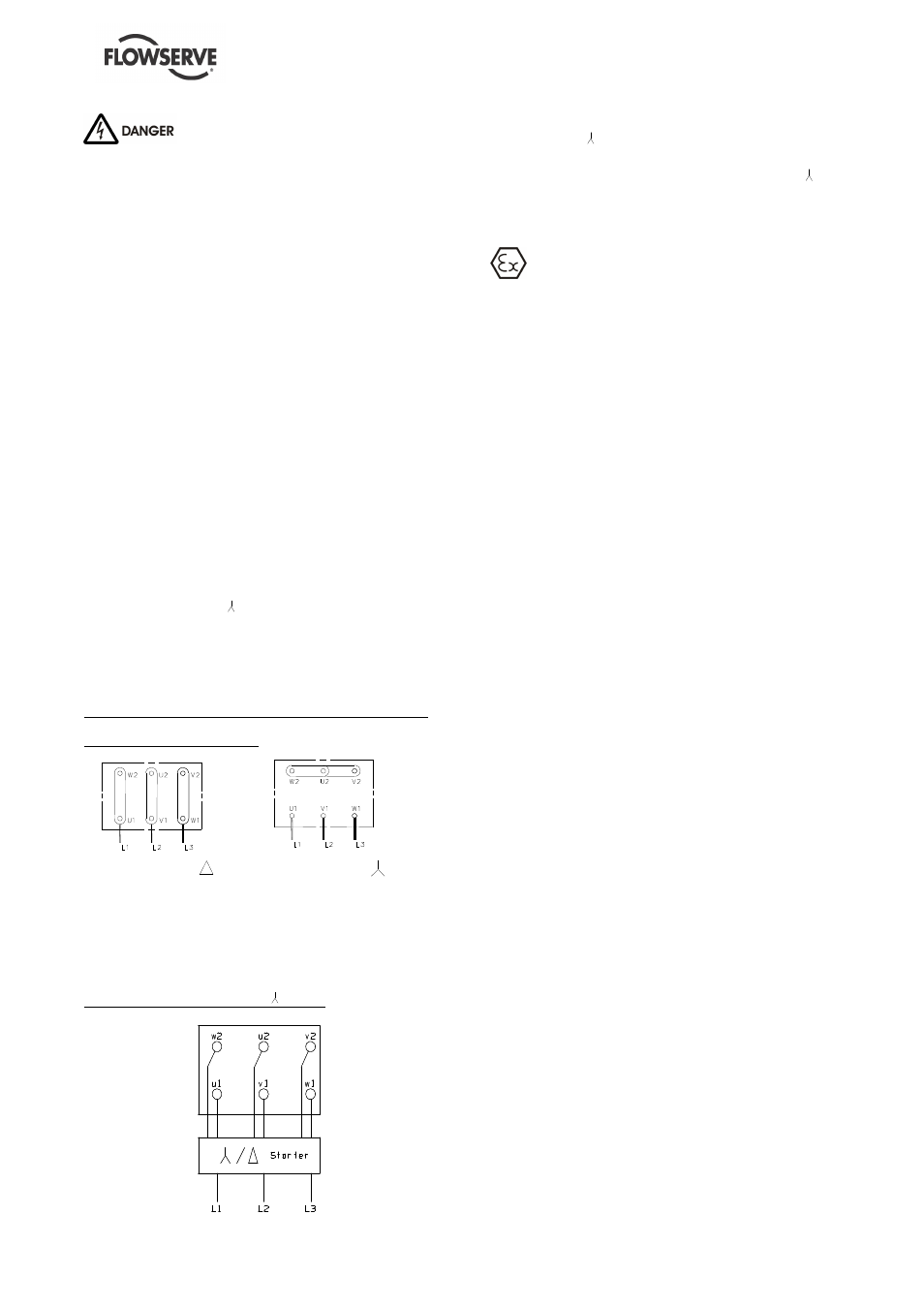
MENBLOC USER INSTRUCTIONS ENGLISH 71576296 - 02/13
Page 20 of 40
flowserve.com
The motor must be protected from
electrical overloading by a thermal overload switch
(overload relay) and fuses, installed between the
isolating switch and motor.
The capacity of the buses and overload relay must
be selected with reference to the full load values
written on the motor nameplate.
The final adjustment of the overload relay setting
should be done following § 5.4.2.
An emergency stop must be fitted.
4.4.2 Electrical supply
Make sure that the voltage of the electrical supply
line is correct for that specified on the motor
nameplate.
Make sure that the supply wires have sufficient
load capacity for the correct running of the
installation.
4.4.3 Wiring Instructions
Motors must be wired:
•
Delta connection (
∆
) for 220/240 V supply or
star connection ( ) for 380/415 V supply for
motors below 3 kW
•
Delta connection (
∆
) for 380/415 V supply for
motors 3.0 kW or larger
•
Supply frequency 50 Hz in all cases
Connection wiring diagram for three phase motors
For Direct on-line starting
Delta connection
Star connection
Wire up the motor terminals according to the
voltage supply, in accordance with the nameplate
fixed on the motor and the connection wiring
diagram displayed inside the terminal box, as
shown above.
When using a separate
∆
/ Stator
Motors of 3.0 kW or larger may be wired up for
star/delta (
∆
/ ) starting on 380/415 V supply. All
connections strips must be removed from the
terminal box and 6 wires connected to the
∆
/
starter, as shown above.
4.5 Protection systems
The following protection systems are
recommended particularly if the pump is installed
in a potentially explosive area or is handling a
hazardous liquid. If in doubt consult Flowserve.
If there is any possibility of the system allowing the
pump to run against a closed valve or below
minimum continuous safe flow a protection device
should be installed to ensure the temperature of
the liquid does not rise to an unsafe level.
If there are any circumstances in which the system
can allow the pump to run dry, or start up empty, a
power monitor should be fitted to stop the pump or
prevent it from being started. This is particularly
relevant if the pump is handling a flammable liquid.
If leakage of product from the pump or its
associated sealing system can cause a hazard it is
recommended that an appropriate leakage
detection system is installed.
To prevent excessive surface temperatures at
bearings it is recommended that temperature or
vibration monitoring are carried out. See sections
5.5.3 and 5.5.4.
If a defect of cooling can lead to temperature
higher than those acceptable a system of cooling
surveillance must be installed.
Except when explicitly required by the customer in
the specifications, when a possibility of reverse
rotation exists the customer must install a reverse
rotation protection device.
The customer must install all equipment required
to avoid water hammer.