Flowserve MENBLOC User Manual
Page 26
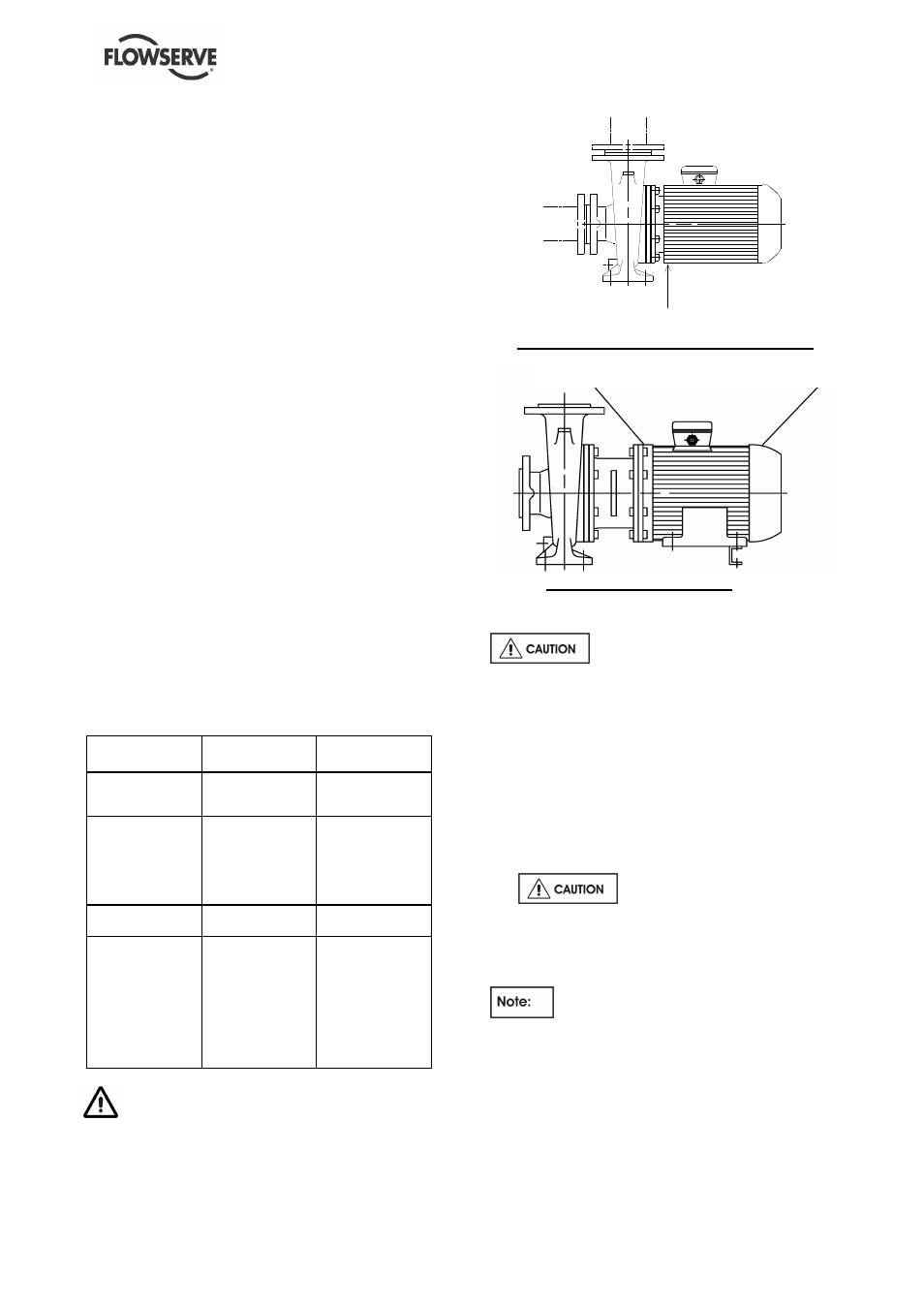
MENBLOC USER INSTRUCTIONS ENGLISH 71576296 - 02/13
Page 26 of 40
flowserve.com
j)
Check the tightness of the connections.
k) Check dirt and dust is removed from areas
around close clearances, bearing housings
and motors.
l)
Check coupling alignment and re-align if
necessary.
m) Verify the correct operation of the system.
The equipment used for maintenance and
disassembly in an ATEX zone must be in
conformity with the requirements zone.
Our specialist service personnel can help with
preventative maintenance records and provide
condition monitoring for temperature and vibration
to identify the onset of potential problems.
If any problems are found the following sequence
of actions should take place:
a) Refer to section 7, Faults; causes and
remedies, for fault diagnosis.
b) Ensure equipment complies with the
recommendations in this manual.
c) Contact Flowserve if the problem persists.
6.2.1 Standard maintenance
Roller bearing
The bearings fitted are prepacked with grease at
the factory. When the regreasing period is reached
it is necessary to remove as much of the old
grease as possible with a clean lint free cloth and
repack the bearings with fresh grease.
MAINTENANCE
OPERATION
FREQUENCY
OBSERVATIONS
Starting (example
of a stand-by
pump)
Weekly
Check the running
state
Evacuation of
condensation
water closed IP 55
motor
Weekly
•
Increase
frequency for
frequent
stops/starts
•
See figure 1
below
Lubrication of all
bearing types
Greased for life
If motors fitted
with grease nipple,
lubrication of
motor bearings
Every 3750 hours
of operation
•
Put 15 g (0.53
oz) of ESSO
UNIMEX N3 or
similar grease for
each grease
nipple with the
electro-pump set
stopped.
•
See figure 2
Open and replace the plastic plugs located
under the casings.
p lu g
Fig. 1 Evacuation of condensation water
G re a s e n ip p le G re a s e n ip p le
Fig. 2 Bearing lubrication
6.2.2 Routine inspection (daily/weekly)
The following checks should be
made and the appropriate action taken to remedy
any deviations:
a) Check the behavior of the pump while running:
noise level, vibrations, bearings temperature,
flow rate and pressure.
b) Motors with sealed for life bearings require no
maintenance. If grease nipples are fitted,
check running hours since last recharge of
grease or carry out a grease change.
6.2.3 Periodic inspection (six monthly)
a)
Check foundation bolts for
security of attachment and corrosion.
b) Check pump-running records for hourly usage
to determine if bearing lubricant requires
changing.
If a check shows a bad running of the
motor pump unit, the user must:
a)
Refer to the "fault finding chart" chapter
7 of this leaflet to apply the recommended
solutions.
b) Ensure that your equipment corresponds to
the arrangements of this leaflet.
c) Contact FLOWSERVE after-sales Department
if the problem persists.