Flowserve VTP Wet Pit User Manual
Page 42
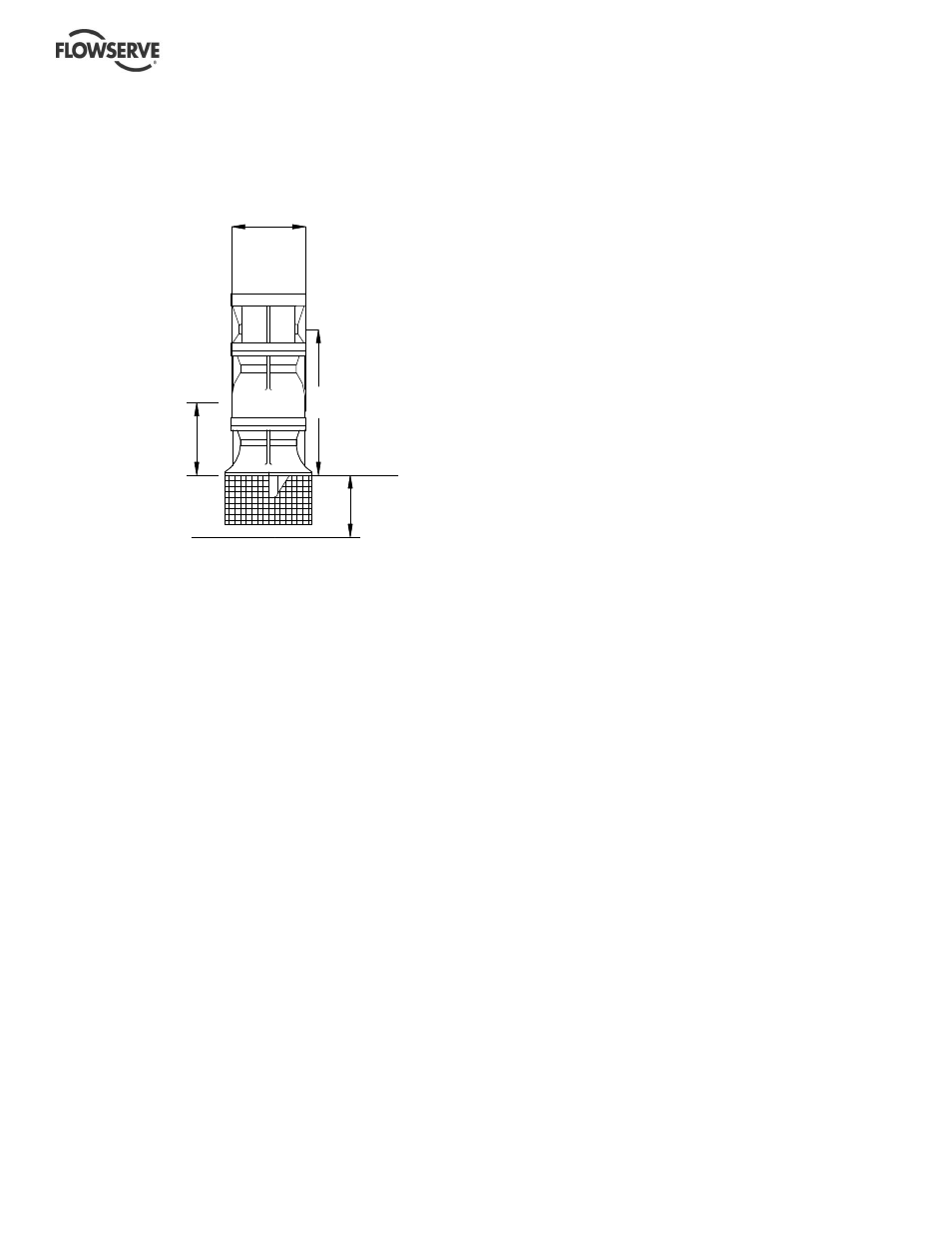
VERTICAL TURBINE PUMPS (VTPS) CENTRIFUGAL PUMPS ENGLISH 71569224
– 10-13
Page 42 of 76
flowserve.com
Pump submergence
5.6.1
Minimum submergence is required to prevent vortex
formation.
The submergence varies in general from 2 to 3 times
the nominal bowl diameter and is always specific to
each pump model. The submergence needed for
adequate NPSH to the first stage impeller may be
different from the general rule mentioned earlier.
Location of the first stage impeller eye to be taken
into account for minimum priming submergence. It is
also equally important to take note of the minimum
distance to be maintained to the suction bell from the
sump floor (with or without strainer). Therefore, refer
to the Flowserve supplied general assembly drawing
on minimum submergence or contact Flowserve
before the pump is started.
Starting the Pump
5.7
Pre-starting checks
5.7.1
Before starting the pump the following checks should
be made.
a) Rotate the pump shaft by hand to make sure the
pump rotates freely and the impellers are
correctly positioned.
b) Ensure that the electric motor has been properly
lubricated in accordance with the instructions
furnished with the driver.
c) Ensure the electric motor has been checked for
proper rotation. The pump must be disconnected
from the driver at the coupling before checking.
The electric motor must rotate counter-clockwise
when looking down on the top of the driver.
d) Check all connections to the driver and control.
Do not overfill the grease cavity. Over greasing
can lead to overheating and premature failure of
the thrust bearing.
e) Check that all piping connections are tight.
f) Check all foundation bolts for tightness.
g) Check all bolting connections for tightness
(coupling bolts, mechanical seal gland bolts,
driver bolts etc).
h) Make sure the mechanical seal is properly
adjusted and locked into place. Ensure that all
seal spacers are in the running position prior to
operation.
i) All guards must be secured in position prior to
pump startup to prevent possible contact with
rotating parts.
To ensure proper alignment three items are very
important during installation and they are:
All machined mating surfaces (such as the
mating faces of the pump and motor) must be
clean and free from burrs and nicks.
These surfaces should be cleaned thoroughly
with a scraper, wire brush and emery cloth if
necessary and all nicks or burrs removed with a
fine file
Exterior strain must not be transmitted to the
pump. The most common cause of trouble in this
respect is forcing the piping to mate with the
pump. It is recommended that flexible
connectors be installed in the piping adjacent to
the pump.
All threads should be checked for damage and
repaired if necessary. If filing is necessary,
remove the part from the pump if possible, or
arrange to catch all the filings so they do not fall
onto other parts of the pump. Clean all threads
with a wire brush and approved cleaning solvent,
ends of shafts must be cleaned and any burrs
removed since alignment depends on the shaft
ends butting squarely. Lubricate all threaded
connections with a suitable approved thread
lubricant (an approved anti-galling compound
should be used on stainless mating threads)
j) On pumps equipped with mechanical seals, clean
fluid should be put into the seal chamber. With
pumps under suction pressure, this can be
accomplished by bleeding all air and vapor out of
the seal chamber and allowing the fluid to enter.
With pumps not under suction pressure, the seal
chamber should be flushed liberally with clean
fluid to provide initial lubrication. Make sure the
mechanical seal is properly adjusted and locked
into place. Insure that all seal spacers are
removed prior to operation.
First
stage imp.
eye location.
Min. Liquid Lvl.
Min.distance
from the sump floor.
Bowl dia
Nom.