Flowserve VF User Manual
Page 20
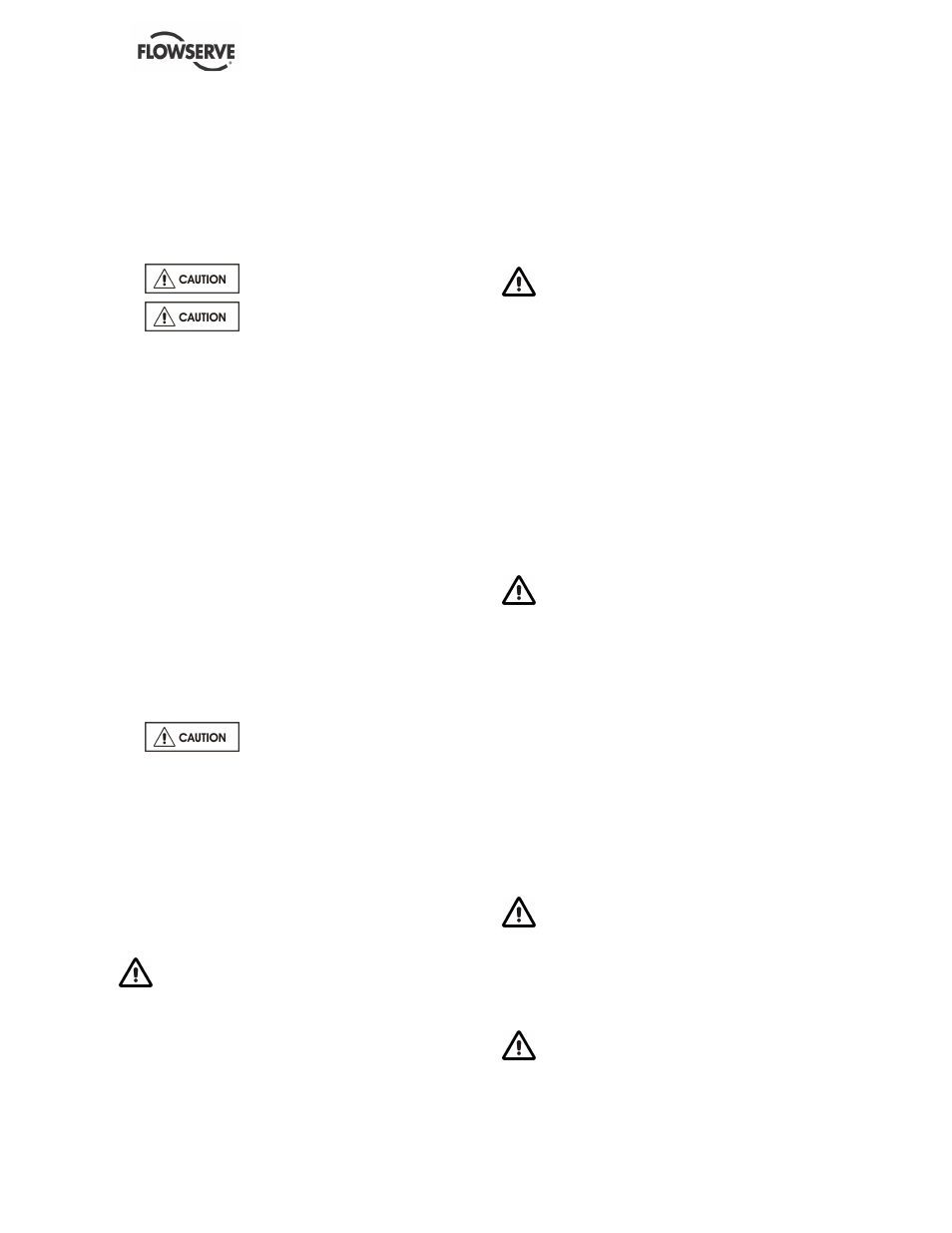
VF USER INSTRUCTIONS ENGLISH 71561233 - 11/09
Page 20 de 32
5.4 Starting the pump
5.4.1 Bring controls and preparation before the
first starting and after each service call
Necessarily:
a) Check the tightening of the different plugs.
b) Check that the gland lightly tightens the
packing rings.
c)
Risk of seal ring overheating.
d)
Install all protection systems
and more particularly the shield grid of the
gland packing [9610.01] and the coupling
guard [9610.02].
e) Check that the liner spraying and filling lines
are effectively connected to the clean water
distribution network.
f) Close the valve at discharge.
g) Check the direction of rotation of the motor.
Refer to the rotation arrow of the pump.
h) Check that the motor bearings are correctly
greased.
i)
Make sure that the ventilating grate is not
obstructed or too near to a wall or an obstacle.
5.4.2 First pump start-up
a) Before starting, the flushing valves of the seals
(if existing) must be opened.
b) The flushing valves of the bearing liner must
be opened.
c) Start motor and check outlet pressure.
d) If pressure is satisfactory, slowly OPEN the
outlet valve.
e)
Do not run the pump with the
outlet valve closed for a period longer than 30
seconds.
f) If NO pressure, or LOW pressure, STOP the
pump. Refer to fault finding chart for fault
diagnosis.
The pump should run smoothly and without
abnormal vibration (see page 21)
The pump must never run at a capacity of less
than 40% of that at the best efficiency.
Never remove a plug when the pump is
running.
When the unit is normally running, note the
maximum intensities absorbed on each phase.
Adjust definitively the circuit breaker for a slightly
greater current to the maximum noticed current,
which must never be superior to the currents,
indicated on the motor description plate. Check
that the voltage between phases in the motor
terminals is correct.
A well adjusted and maintained circuit breaker
efficiently protects the pump unit. Any disjunction
means that the unit is badly running (voltage loss,
cut phase, misadjustment, foreign matter in the
pump, jamming, etc...).
5.5 Running the pump
5.5.1 Venting the pump
Vent the pump to enable all trapped air to
escape taking due care with hot or hazardous
liquids. Under normal operating conditions, after
the pump has been fully primed and vented, it
should be unnecessary to re-vent the pump.
5.5.2 Pump fitted with a stuffing box
If the pump has a packed gland there must be
some leakage from the gland. Gland nuts should
initially be finger-tight only. Leakage should take
place soon after the stuffing box is pressurized. If
no leakage takes place the packing will begin to
overheat. If overheating takes place the pump
should be stopped and allowed to cool before
being re-started. When the pump is re-started it
should be checked to ensure leakage is taking
place at the packed gland.
When adjusting an operating stuffing box
(shield grids removed for this operation), the
operator must be very careful. Safety gloves are
compulsory and loose clothes are not allowed
(above all to the arms) to avoid being caught by
the pump shaft.
The pump should be run for ten minutes with
steady leakage and the gland nuts tightened by 10
degrees at a time until leakage is reduced to an
acceptable level. The temperature of the gland
should be checked after each round of tightening.
If the temperature starts to climb rapidly then back
off the gland nuts until the temperature drops
down. Wait for the temperature to stabilize before
tightening again. The leakage must not be
reduced below a rate of 20 drops per minute.
Bedding in of the packing may take several hours.
Shield grids being removed during
installation of the gland packing, it must be
ensured that they are replaced as soon as this
operation is completed.
SAFETY INSTRUCTIONS WHEN THE PUMP IS
RUNNING:
If hot or freezing components of the machine
can present a danger to operators, they must be
shielded to avoid accidental contact. If a 100 %
protection is not possible, the machine access
must be confined to the maintenance staff only.