Xl90 options – Flowserve XL90 Series User Manual
Page 8
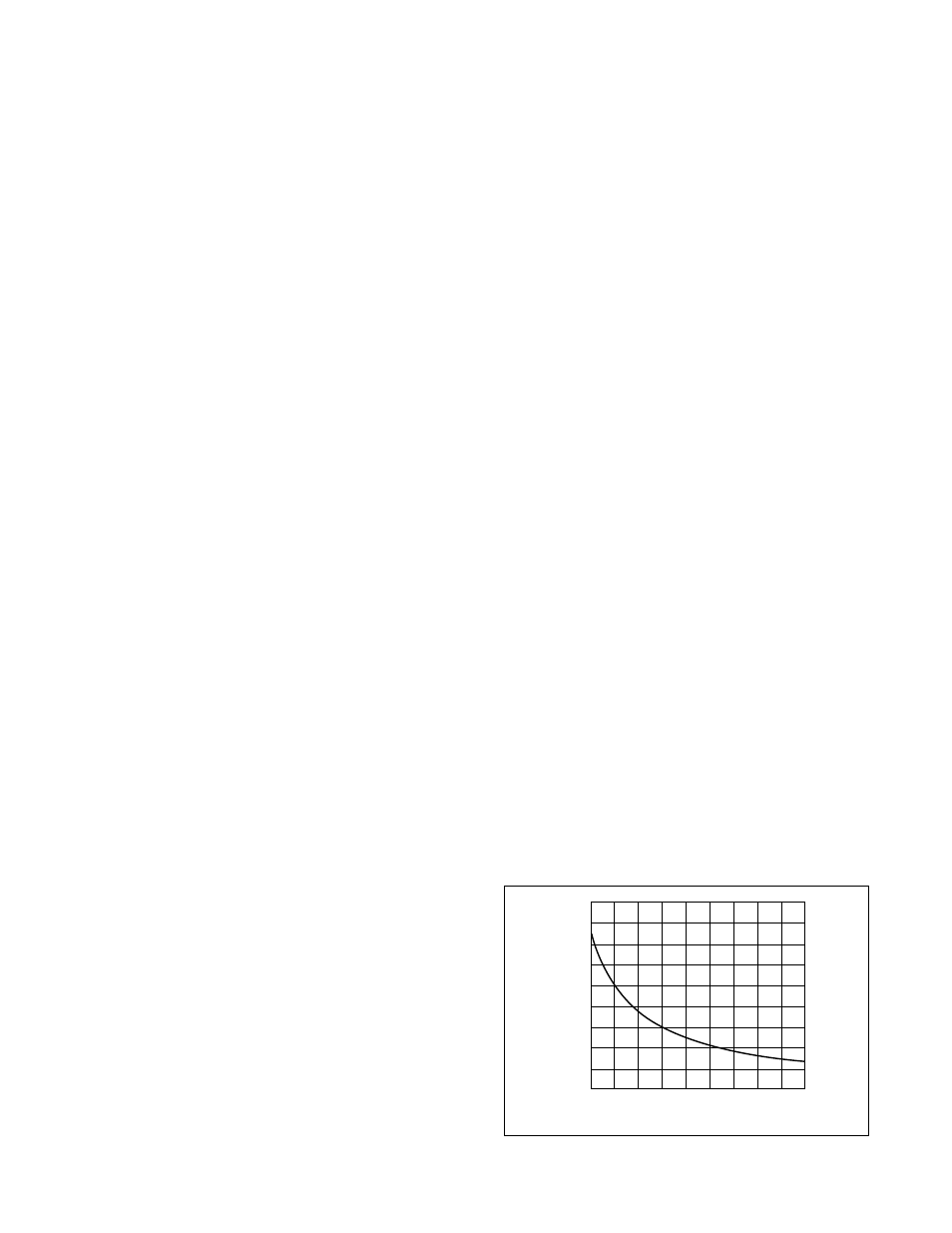
adjustable gain lower plate (26), and diaphragm plate.
Remove signal diaphragm assembly (15) and remove relay
plate (14) from between the diaphragms. Place relay plate
(14) between the diaphragms on the new assembly taking
care to align the 1/16-inch diameter holes between the
diaphragms and the relay plate (14). Replace diaphragm
plate (15), adjustable gain lower plate (26), washer (24),
and locking screw, but do not tighten. Replace four screws
(32) that hold signal diaphragm assembly together.
16. Pack O-ring grease into the O-ring groove and lightly lubri-
cate the outside of the relay tube on diaphragm relay
assembly (13). Make sure small holes on the side of the
tube do not get plugged with grease. Insert the relay
diaphragm assembly (13) as assembled in steps 7 and 8
into the lower relay half. Carefully align the flapper (21) over
the adjustable gain screw (19) and replace and tighten the
nut (25).
17. Fasten the two halves of the relay together using four long
screws (32). Make sure the 1/16-inch diameter holes in the
relay diaphragm assembly (13) and the upper relay body
(9) line up. Set gain to desired setting and tighten locking
screws (23, 25). See gain adjustment procedure.
18. Replace screen (110) and O-rings (8,12) found on the back
of the pilot relay before reinstalling the pilot relay on the
base of the positioner with four screws (33). Clean out any
debris lodged in screen or replace with a new one.
19. Replace span arm and zero arm (40, 46) and feedback
spring (47).
Installation, Operation and Maintenance of
UltraSwitch Position Indicators
For detailed information, refer to the following Accord controls
bulletins:
• PS0008, PS0009, PS0031, PS0032, PS0033, PS0034,
PS0037 and PS0050
XL90 OPTIONS
Option F: 4-20 mA Transmitter
The XL 90 Feedback Option allows accurate and reliable moni-
toring of valve position when installed in the XL 90 positioner.
The Feedback Option may be used in any non-hazardous loca-
tion. For hazardous locations utilize the UltraSwitch L explosion
proof limit switch enclosure.
Voltage Supply Required: 6-30 VDC
Impedance: 300 Ohms at 20 mA
Note: Impedance changes with current (see chart). To properly
design the current loop, use 300 Ohms and 20 mA current.
Option J and K: Mechanical Switches
Mechanical switch technology is the oldest yet most cost effec-
tive switching method used today. Tool-free cam adjustment is
accomplished through a spring-loaded spline arrangement.
Simply push or pull the cam, disengaging the splines, and rotate
to the desired switch trip point. After releasing, the spring causes
automatic spline engagement, locking the setting.
2-SPDT
Load Capacity: 15 amp & 1/2 HP 125 VAC, 10 amp 250 VAC,
1/2 amp 125 VDC, 1/4 amp 250 VDC
Operating Force: 4.8 ounces
Differential Travel: 0.016 inches minimum
Mechanical Life: 10,000,000 cycles
Option M and N: Proximity Switches
Proximity reed switches offer cost effective contacts for extend-
ed life in corrosive applications. These switches are tripped by
magnets embedded in cams to indicate valve open and closed
positions. Tool-free cam adjustment is accomplished through a
spring-loaded spline arrangement. Simply push or pull the cam,
disengaging the splines, and rotate to desired switch trip point.
After releasing, the spring causes automatic spline engagement,
locking the setting.
SPST Proximity Switches
Load Capacity: 0.35 amp 140 VAC, 1 amp 50 VDC, 50 Watt Max.
contact rating
Contact Material: Rhodium plated
Actuated by magnetic force
SPDT Proximity Switches
Load Capacity: 0.25 amp 120 VAC, 0.25 amp 28 VDC, 3 Watt
Max. contact rating
Contact Material: Ruthenium plated
Actuatore by magnetic force
MOV and 0.25 amp fuse protected
Option Q: Intrinsically Safe Solid State Proximity Switches
With the same mounting as the mechanical switches the
FM/CSA rated I.S. Solid State Proximity Switches can be used to
obtain valve open and closed position. Tool-free cam adjustment
is accomplished through a spring-loaded spline arrangement.
Simply push or pull the cam, disengaging the splines, and rotate
to the desired switch trip point. After releasing, the spring causes
automatic spline engagement, locking the setting.
Load Capacity:
≤
(less than or equal to) 1 mA
≥
(greater than or
equal to) 3 mA
Voltage Range: 5-25 VDC
48-8
Flowserve Corporation, Valtek Control Products, Tel. USA 801 489 8611
4 8 12
16 20
1800
1600
1400
1200
1000
800
600
400
200
0
CURRENT (mA)
IMPED
ANCE (OHMS)