Third-party actuator mounting, Troubleshooting the logix 1400 digital positioner, Theory of operation – Flowserve 1400 Valtek Logix User Manual
Page 13: Orient the take-off arm for final lock down, Optional rotary mounting procedure
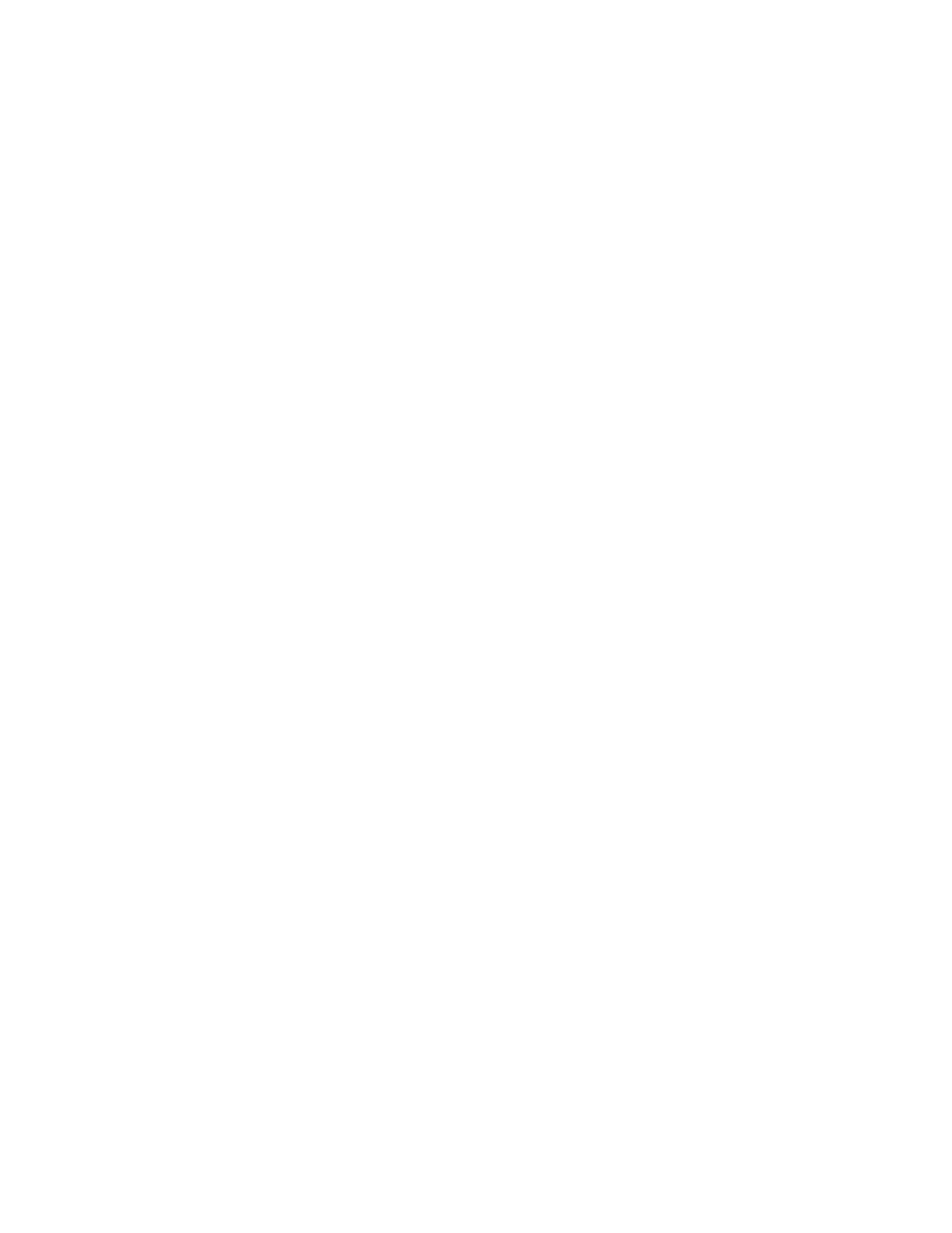
46-13
Flowserve Corporation, Valtek Control Products, Tel. USA 801 489 8611
Third-party Actuator Mounting
Contact the factory for information on mounting the Logix
1400 digital positioner on actuators not manufactured by
Flowserve.
Troubleshooting the Logix 1400 Digital
Positioner
This section provides troubleshooting information for the
two-wire, F
OUNDATION
fieldbus communication based, Logix
14xx series digital positioner. In addition, pointers on
operation and configuration will also be covered.
Theory of Operation
Figure 16 shows the basic positioning block diagram for
the Logix 1400 digital positioner.
Orient the Take-off Arm for Final Lock Down
Tube positioner to valve in the following manner:
1. Output 1 port of the manifold to bottom side of actuator.
2. Output 2 port of the manifold to the top side of the
actuator.
3. Connect the fieldbus to the field termination screws
under cover.
4. Connect regulated (70 psi) air supply to appropriate
port in manifold.
5. If setup was successful the green LED will blink and
the valve will be in control mode.
Use the NI Configurator to complete and monitor the
following steps:
1. Start the configurator.
2. Monitor the FVPTB block
3. In the transducer block, variable AD_RAW_FB
number is the digital representation of shaft position.
NOTE: To update the AD_RAW_FB variable, the
‘Enable Diagnostic Variable Access’ selection must
be enabled in TEST_MODE of the transducer block.
4. With supply pressure cut, rotate follower arm in the
same direction the shaft would rotate upon a loss of
supply pressure. When the mechanical stop of follower
arm is reached, tighten bolt on the take-off arm.
NOTE: The nut should be snug enough to hold the
follower arm in place but allow movement when
pushed.
The AD_RAW_FB number should now read 3600 or
500 (
±
50).
5. Back the follower arm away from the mechanical
stop, watching the AD_RAW_FB number, until the
number changes 50-150 counts.
6. Tighten the nut on the take-off arm.
NOTE: The
socket head bolt on the take-off arm needs to be as
tight as possible. If the take-off arm slips the positioner
will need to be re-calibrated.
7. Recalibrate using the Re-Cal button.
8. Set the FINAL_VALUE to 100. Using a screwdriver
press down on the follower arm’s pin so the pin
touches the other side of the slot. The AD_RAW_FB
number should change about 20 counts and the
valve should move a small amount. If no change in
the AD_RAW_FB number or movement in the valve
occurs repeat steps 4-8 but limit the change in
AD_RAW_FB in step 5 to 30-75 counts.
WARNING: Failure to follow this procedure will
result in positioner and/or linkage damage. Check
air-action and stroke carefully before lockdown
of take-off arm to spline lever adapter.
Optional Rotary Mounting Procedure
(Figure 15)
The optional rotary mounting applies to valve/actuator
assemblies that are equipped with mounted volume
tanks or handwheels. The optional mounting uses a four-
bar linkage coupled to the valve shaft. The following tools
are required:
3
/
8
-inch box wrench
7
/
16
-inch box wrench
1
/
2
-inch box wrench
1. Using a
1
/
2
-inch box end wrench and two
5
/
16
-18 x .50
L. bolts, attach bracket to actuator transfer case
pads. Leave bracket loose to allow for adjustment.
2. Using four
1
/
4
-20 x .50 L. bolts and a
1
/
16
-inch box
wrench, fasten positioner to universal bracket, using
the four-hole pattern that locates the positioner the
farthest from the valve. Rotate positioner 90 degrees
from normal so gauges are facing upward.
3. Attach follower arm to positioner feedback shaft,
using the star washer and No. 10-32 nut.
4. Attach tripper and tripper clamp to shaft, using two
1
/
4
-20 L. bolts and two
1
/
4
-20 locknuts. Leave tripper
loose on shaft until final adjustment.
5. Thread ball joint linkage end to tripper and tighten
(Thread locking compound such as Loctite is recom-
mended to prevent back threading). Adjust length of
tie rod so follower arm and tripper rotate parallel to
each other (the rod must be cut to the desired
length). Connect other ball joint end to follower arm
using a star washer and a No. 10-32 nut.
6. Tighten bracket and tripper bolting.
7. Check for proper operation, note direction of rotation.
WARNING: Rotating in the wrong direction will
result in serious damage to the positioner and/or
linkage. Check air action and stroke direction
carefully.