Flowserve 1400 Valtek Logix User Manual
Page 19
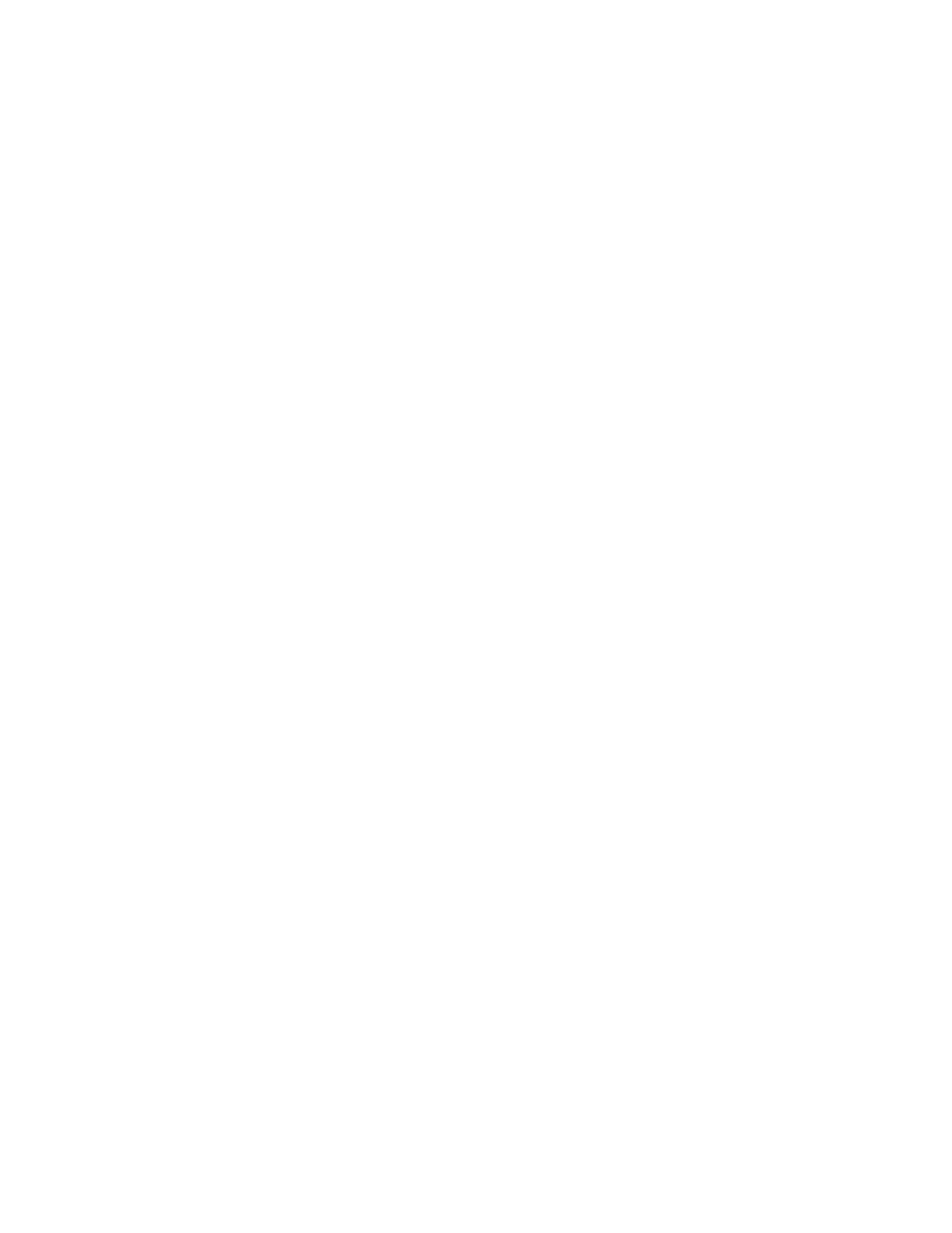
46-19
Flowserve Corporation, Valtek Control Products, Tel. USA 801 489 8611
Modulator Current Alarm
The pressure modulator is an electro-pnuematic device
which takes a current signal from the electronics control
and generates a pressure which moves the spool. The
Logix 1400 digital positioner is a FB powered device
which must run on very low power. During operation, the
pressure modulator current is monitored. If the current
draw exceeds 0.9mA under normal control, the modula-
tor current alarm will become active and the red LED will
blink. Sometimes, the current level may be right at the
threshold of 0.9mA causing the LED to alternate between
red and green. Listed below are some reasons for a
modulator current alarm. The magnitude of modulator
coil current can be viewed from the configurator.
• Modulator minimum pressure too low
• Clogged or restricted orifice
• Bad or missing cable connection to collector board
assembly
• Stuck or sticky spool
• Internal air leaks: tubing, orifice gasket, pressure
modulator
EEPROM Checksum Alarm
Configuration data is stored in EEPROM. When power is
lost, configuration information is retrieved from EEPROM
and operation resumes. A check is done by the micro-
controller after a power-up to make sure data saved in
EEPROM has not been corrupted. The checksum is a
number which is calculated based on configuration data.
It is also saved in EEPROM every time data is stored. If
after a power-up, this number does not match the data in
memory, an EEPROM checksum alarm is generated and
the red LED will blink. If this occurs, try powering the
Logix 1400 digital positioner off and then back on. If the
error does not clear, try saving configuration data again
using FB Configurator. If previous configuration has not
been saved, you must reset the device and re-configure.
If these steps still do not clear the error, the main PCB
assembly must be replaced. Refer to the
Spare Part Kits
section.
Pressure Alarms
Note: Pressure alarms are only available on models with
advanced diagnostics (Logix 141x).
Advanced diagnostic models add ouput port 1, output port
2 and supply pressure sensors. These sensor readings
and alarms are only accessible from the communicator
when the configuration has been set to advanced.
Loss of Pressure: The loss of pressure alarm becomes
active when the supply pressure is near the minimum
positioner operating pressure of 30 psig. If the LEDs
alternate between red and green, the supply pressure
may be at the limit threshold. This alarm is meant to alert
the user to low supply pressure as well as complete loss
of pressure.
Output Port 1 Sensor, Output Port 2 Sensor, Supply
Sensor: Each sensor is checked during actuator calibra-
tion. If a calibration reading appears to be out of range,
the appropriate alarm will become active. The pressure
sensors are located on the collector board assembly.
Alerts
FINAL_VALUE_CUTOFF
The FINAL_VALUE_CUTOFF or tight shutoff feature
of the Logix 1400 digital positioner allows the user to
control the level at which the command signal causes
full actuator saturation in the closed or open position.
This feature can be used to guarantee actuator satura-
tion in the closed or open position or prevent throttling
around the seat at small command signal levels. To
enable, use configuration to apply the desired
FINAL_VALUE_CUTOFF threshold.
Note: The positioner automatically adds a 1 percent
hysteresis value to the FINAL_VALUE_CUTOFF_LO
setting to prevent jumping in and out of saturation when
the command is close to the setting.
Effects of FINAL_VALUE_CUTOFF on Operation
With the FINAL_VALUE_CUTOFF_LO set at 5 percent
the positioner will operate as follows:
Assume that the present command signal is at 50
percent. If the command signal is decreased, the posi-
tioner will follow the command until it reaches 5 percent.
At 5 percent, full actuator saturation will occur. The
actuator will maintain full saturation below 5 percent
command signal. Now, as the command increases, the
positioner will remain saturated until the command
reaches 6 percent (remember the 1 percent hysteresis
value added by the positioner). At this point, the stem
position will follow the command signal.
If the FINAL_VALUE_CUTOFF_LO is set to 3 percent
but the valve will not go below 10 percent,
SOFTSTOP_LOW may be enabled. The lower soft
limit must be less than or equal to 0 percent in order
for the FINAL_VALUE_CUTOFF_LO to become ac-
tive. If soft stops are active (ie: SOFTSTOP_LOW =
0 or SOFTSTOP_HIGH = 100) FINAL_VALUE_CUTOFF
is disabled.
Soft Limits
Unlike position alerts, soft limits prevent the stem posi-
tion from going below or above the configured limits. If
the command signal is trying to drive the position past
one of the limits, the yellow LED will blink but the stem
position will remain at the set limit.
Travel Accumulator
The travel accumulator is equivalent to a car odometer
and sums the total valve movement. Using the user
defined stroke length and travel dead-band, the Logix