Flowserve LHS Hydraulic Heavy-Duty Actuator Series User Manual
Page 14
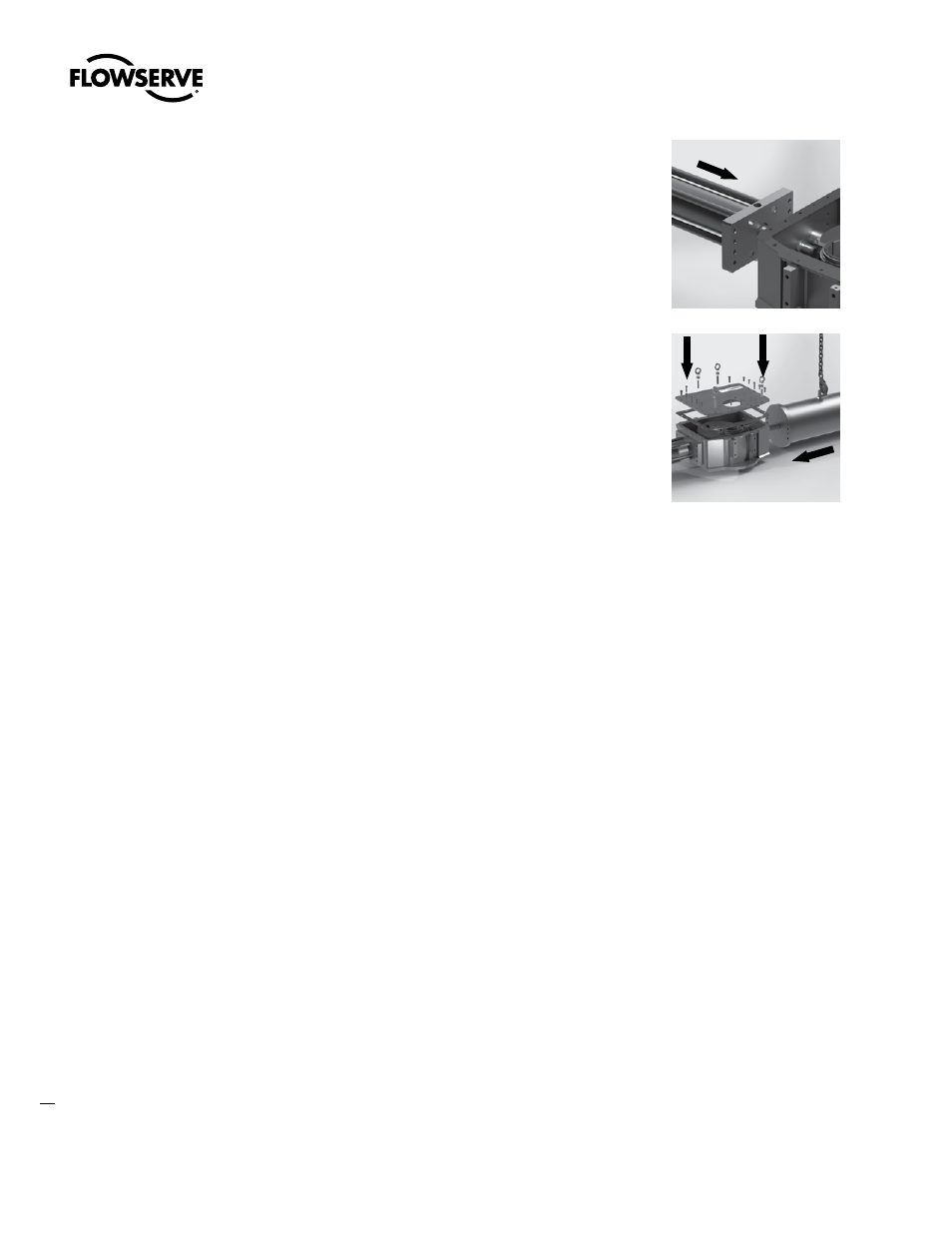
14
LHS Hydraulic Heavy-Duty Actuator Series FCD LFENIM0003-00-AQ 7/14
3.1.3 Change the adapter kit. Replace the adapters (54 and 55) designed for fail
close (open) action, with the new ones designed for the opposite action.
NOTE: Take care to choose the adapter kit suitable for the scotch-yoke
type in use (symmetric or canted).
Reassemble the hydraulic cylinder with adapter, using the reverse
procedure as described in point 4.3.
NOTE: You can recognize the cylinder adapter to the spring can adapter
through the three grub screws (53).
3.1.4 Manually rotate the scotch-yoke (36) until the guide block (48) is in contact
with the cylinder adapter (54), in correspondence of the relevant slot.
Reassemble the spring can, as instructed in paragraph 4.2. Reposition
the cover, taking care to replace the cover gasket (47).
Readjust the stops, as instructed in paragraph 2.3.
Periodically operate the actuator to check the functioning in the
new fail configuration.
3.2 Actuator Connected to the Valve
(and the valve can be stroked)
NOTE: If the valve cannot be rotated, due to the requirements of the plant, the actuator must be removed from
the valve following the instructions given in paragraph 2.2. In this case, use the procedure described above. The
actuator should be reinstalled in the same position of the valve.
a
WARNING: Ensure that the hydraulic connection ports of the cylinder are disconnected. Also make sure that
all hydraulic supplies to the control unit and all power supplies are disconnected. Finally, make sure that the
actuator is in fail safe position, i.e. that it is not locked in a position with the spring compressed by means of
locking devices.
3.2.1 Apply the minimum necessary pressure to the cylinder hydraulic port on the end flange and move the actu-
ator to approximately 45°. If the actuator is provided with a manual override, you can use it to perform this
operation.
3.2.2 Measure the position of the spring can end stop (7), remove it, and then lock the spring in the compressed
position by means of a special tool for this maintenance. The tool is to be installed in the opening where the
spring-end travel-stop has been removed. Remove pressure from the hydraulic cylinder.
a
WARNING: At this point the spring is compressed and the spring module contains a large quantity of stored
energy. Failure to properly engage the retaining device or failure to handle the spring carefully could result in
release of the spring with potential damage to equipment or injury to personnel.