Air supply and electrical installation, Worcester controls – Flowserve 10 ACCESS I 39 Actuators with DeviceNet Interface User Manual
Page 3
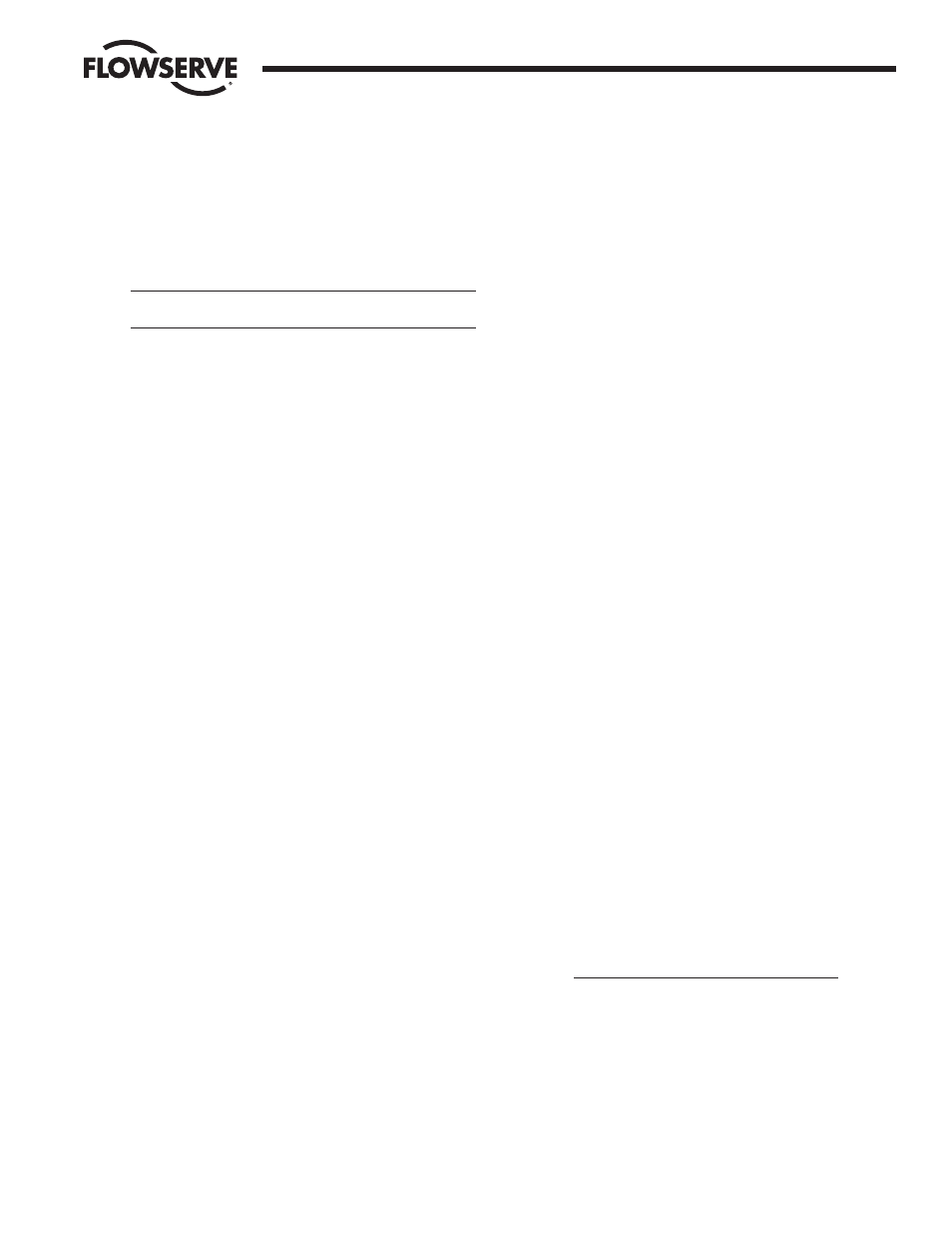
WCAIM2019
10, 15, 20 ACCESS I 39 Actuators with DeviceNet Interface
3
Flow Control Division
Worcester Controls
remove handle nut, lockwasher, handle, separate stop plate (if
any), retaining nut and stop pin(s). Add the two additional
Belleville washers with their larger diameter sides touching
each other. Add the self-locking nut to the stem and tighten
while holding the stem flats with wrench. Tighten until
Belleville washers are flat, the nut will “bottom,” and then back
nut off
1
/
3
of a turn. The two additional Belleville washers and
the self-locking nut are included in the mounting kit.
CAUTION: The self-locking stem nut is difficult to tighten,
and must fully flatten Belleville washers before backing off.
For 2" 59, H71, 82/83, and 2
1
/
2
" 45, 82/83 valves, and valves 3"
and larger with square stem, remove handle assembly,
retaining nut, stop and stop screws. Replace with valve stem
spacer or, if valve has graphite stem packing, with two
Belleville washers, and replace retaining nut. NOTE: Belleville
washers are installed with their larger diameter sides touching
each other. Do not use stem spacer when Belleville washers
are used. Using a wrench to prevent stem from turning,
tighten retaining nut until stem packing is fully compressed or
Bellevilles, if used, are fully flattened, then back off nut
1
/
6
turn. Excessive tightening causes higher torque and shorter
seal life.
NOTE: Large valves with V51 high-cycle stem packing option
installed, identified by two Belleville washers installed and
handle assembly, stop and stop screws removed, and
818/828 Series valves do not require stem area disassembly.
For 2" and larger 818/828 valves, remove handle assembly,
locking plates and hardware, and stop screw (if any). Do not
remove stop plate or spacer.
For
1
/
2
"–2" 94 valves, remove handle (if any). Do not remove
gland plate or gland bolts.
For 3" and larger 94 and 2" and larger E818/828 valves,
remove handle assembly, stop, and spacer (if any). Do not
remove gland plate or gland bolts.
3. Center coupling on valve stem.
4. Lower mounting bracket/actuator assembly over coupling and
onto valve, making sure that male actuator shaft engages slot
in coupling.
5. Secure bracket to valve using cap screws and lockwashers, or
bolts and nuts provided in mounting kit. Tighten securely. For
1
/
2
"–2" top mount style valves, bracket nameplate will be to the
side of the valve.
6. Install set screws (if any) in the coupling and tighten securely
7. Determine if mode of operation is as desired; if not:
a. Double-Acting Actuators – Mount the actuator 90° from
normal mounting, or the actuator can be inverted, yielding
the opposite mode.
b. Spring-Return Actuators – The normal method of
mounting is to have the actuator inline with the pipe line
and the valve and actuator in the “Fail-Closed” position.
For “FAIL-CLOSED” cross-line operation, invert
actuator and cross-line mount actuator to pipe line.
For “FAIL-OPEN” inline operation, invert actuator.
(NOTE: If inline coupling is used, actuator does not
need to be inverted.) Rotate the valve ball and stem
90°, so coupling lines up with actuator shaft. Mount
actuator in line with the pipeline. See Electrical
Connection Section for proper wiring information.
For “FAIL-OPEN” cross-line operation, rotate the valve
ball and stem 90°, so coupling lines up with actuator
shaft. Mount actuator cross-line to pipe line. See
Electrical Connection Section for proper wiring
information.
8. Determine position indication. Buttons on position indicator
are set up to show valve closed on inline mounting, i.e.,
pistons together in actuator. If different indication is required:
a. Check which visual indication is required.
b. Check that indicator, when located on actuator shaft, will
show correct indication.
c. To change indication, push out (remove) red and white
buttons and reassemble in opposite positions.
d. Locate indicator on actuator shaft flats. Press firmly until
location nibs snap into recess on pinion.
AIR SUPPLY AND
ELECTRICAL INSTALLATION
A. 1.
Air Supply:
The Series 39 Actuator is factory lubricated. For optimum
operation, the use of filtered and lubricated air is
recommended.
2. Air Supply Pressure:
Standard double-acting actuators require 40–120 psig supply
air. Spring-return actuators require 80–120 psig supply air.
Spring-return actuators can also be set up to operate on
supply air pressures ranging from 40–80 psig by using fewer
springs. See “Rebuilding Instructions,” Spring-Return
Actuator, paragraph 1 on page 10 for proper number and
location of springs for reduced supply air pressures.
3. Air Supply Connection:
Connect air supply to
1
/
4
" NPT connection on control block.
4. Recommended Tubing Sizes:
In order to provide sufficient flow of supply air to the Series
39 actuator, the following tubing sizes are recommended:
Runs Up To
Runs Over
Actuator Size
4 ft. Long
4 ft. Long
10, 15, 20
1
/
8
"
1
/
4
"
5. Air Consumption:
The following chart shows the amount of pressurized (80
psig) air consumed per stroke in cubic feet. To determine the
total amount of air consumed per complete cycle for double-
acting actuators, simply add the volumes for both the opening
and closing strokes together; for spring-return units, the total
volume of air consumed is the volume shown for the opening
stroke.