Fast laser nozzles -3, Principles of operation -3, Fast nozzle installation -3 – Hypertherm LH2100 User Manual
Page 30: Inspect the baffle -3, Fast laser nozzles
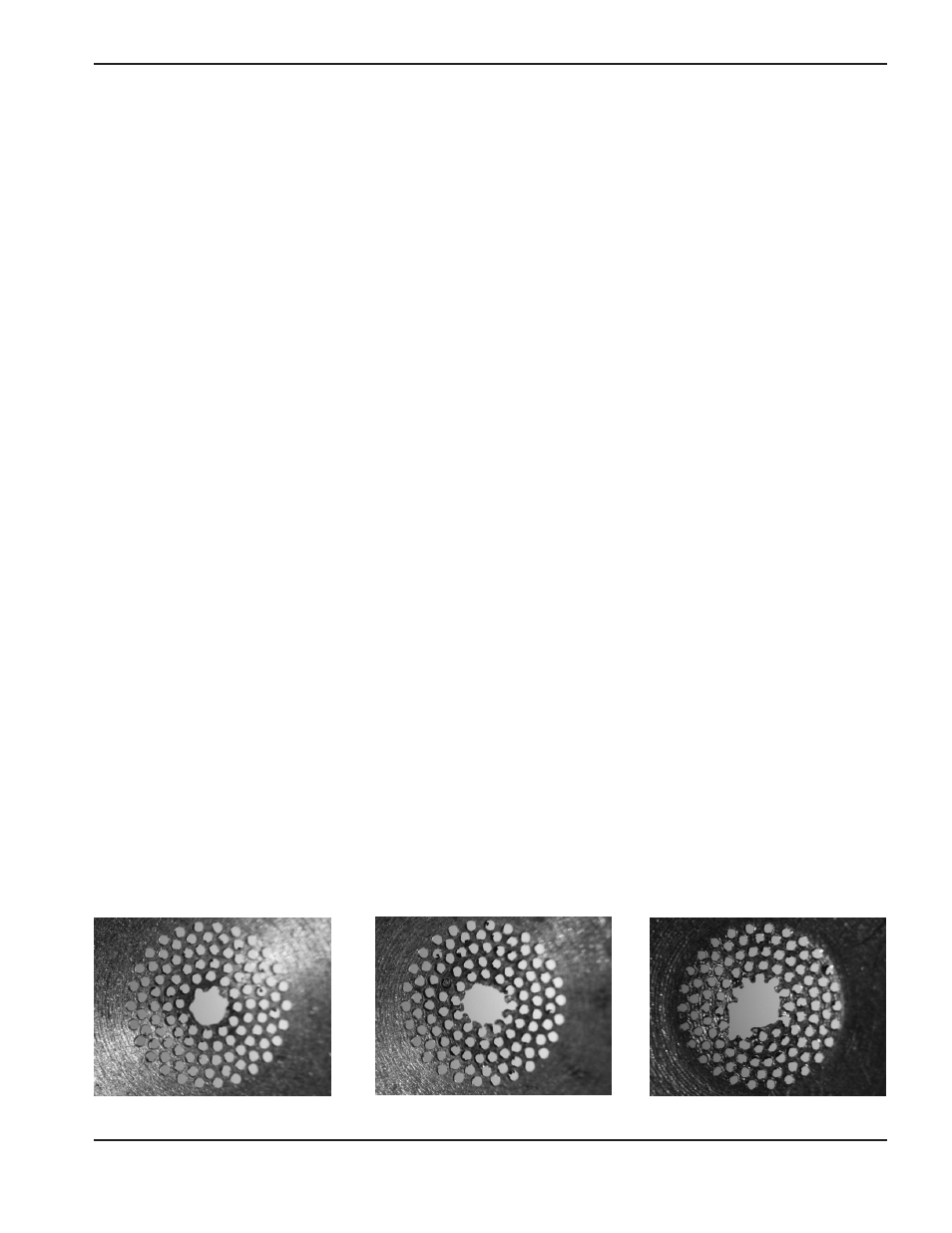
1
OPERATION
LH2125/LH2100 Laser Head Instruction Manual
4-3
FAST Laser nozzles
Principles of operation
FAST Laser nozzles achieve increased performance in oxygen-assisted mild steel cutting by modification of the cutting-
gas flow as it passes through the baffle at the nozzle exit. The laser beam forms a hole in the baffle that is the the same
diameter as the beam and approximately the same width as the kerf in the plate. The gas flow through this hole is
unrestricted and forms a small-diameter jet that couples efficiently into the kerf. The gas flow through the surrounding
baffle is restricted and exits with a lower velocity. This low-velocity jet shields the high-velocity central jet and controls
the reaction between the gas and workpiece. The FAST Laser nozzles operate at a plenum pressure that is 1.5 to 2
times higher than traditional laser cutting nozzles.
The reaction between the oxygen and the mild steel is influenced by many factors, including oxygen purity, oxygen
pressure, chemical composition of the plate, microstructure of the grains in the steel, surface condition of the steel and
laser mode (quality). It is also important to verify that the nozzle is in good condition, and essential that the hole in the
baffle remains approximately the same size as the kerf, to prevent excessive burning. FAST laser nozzles are intended for
low pressure 3.0 bar (45 psi) O
2
cutting.
Take these precautions to prevent enlargement of the hole:
1. Maintain a nozzle-to-workpiece distance of 6 mm (0.24") or more during a pierce. If the nozzle is too close to the
workpiece, a reflection during the first 50 milliseconds can damage the baffle.
2. Use a pressure of 1.4 bar (20 psi) or higher during a continuous wave (blast) pierce, to protect the nozzle from molten
metal that is blown back from the pierce.
3. The relative position of the lens in its piercing and cutting position must be kept within 2% of the lens’ focal length to
ensure the hole in the baffle does not grow to an unacceptable level.
Note: Do not use Hypertherm’s FAST Laser nozzles for cutting stainless steel, aluminum or laser
alignment. Use only the “standard” nozzles listed in the Parts List of this manual for cutting
stainless steel and during laser alignment.
FAST nozzle installation
When a new nozzle is installed it must be conditioned by using the following procedure:
Move the focus about + 3.5 mm (0.14") from the normal cutting location and irradiate the nozzle with the laser
beam for about 10 seconds at full power. This will ensure that the baffle will not interfere with laser beam when the
focus is returned to the cutting location and gives optimal piercing and cutting performance.
Inspect the baffle
The nozzle should be replaced when the central (conditioned) hole becomes large enough to break into the next
array of holes.
Baffle with central (conditioned) hole
The nozzle needs to be replaced
Baffle with a marginal hole