Powermax1650, Maintenance, Service manual – Hypertherm Powermax1650 Service Manual User Manual
Page 39
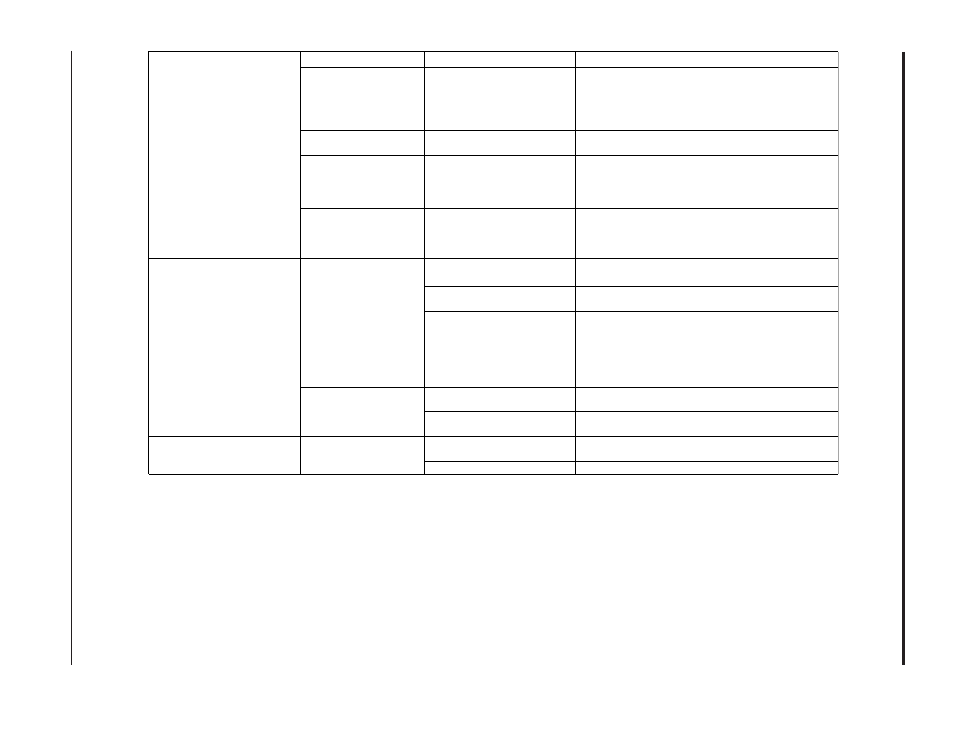
MAINTENANCE
3-12
powermax1650
Service Manual
0
Worn consumables
Worn-out consumables
Replace consumables
Improper air pressure
setting or low flow
Insufficient supply or air leak
on supply line
Turn current adjust knob to test flow and set pressure
regulator to 75 psi (5.2 bar) for cutting or 50 psi (3.4
bar) for gouging. If unable to adjust to proper setting,
verify that inlet pressure is between 90 psi (6.1 bar)
and 120 psi (8.3 bar).
Poor quality air
Moisture or contaminates in air
supply
Add appropriate filtration and purge lines with nitrogen
to flush out oil and moisture.
Insufficient input power
Undersized electrical supply
installation:
- Breaker/fuse
- Supply wire
Verify external electrical power is installed per
specifications in section 2. Check input voltage while
trying to fire torch. Voltage drop indicates undersized
electrical supply installation.
Inverter fault or interlock
Power board (PCB2) failure
If the control board (PCB2) IF LED illuminates and one
or more of the fault LEDs illuminate, then the fault is
caused by the parameter monitored by the fault LED. If
no fault LED is illuminated, replace power board.
Poor work lead connection
Verify work lead is attached to workpiece and
workpiece is free of rust, paint, etc.
Damaged work lead
Check continuity of work lead. Replace or repair as
required.
Defective pilot arc IGBT (Q15) Turn power OFF, remove consumables, check
resistance between plunger and work piece. If
resistance is greater than 8k ohms. Inspect work lead.
Check pilot arc IGBT resistance between two screws at
Q15 on power board. If resistance is less than 5k
ohms, replace pilot arc IGBT.
Current adjustment set too low Verify current adjust knob is at proper setting (turn to
max, full clockwise).
Defective power board current
sensor
Replace power board. Can confirm power output by
measuring with a DC current clamp meter on work
Mode switch set wrong
Set mode switch to correct position.
Faulty control board (PCB3)
Replace control board.
Inadequate ground
Low output from power
supply
Losing pilot arc when going
off plate while in continuous
pilot mode
Continous pilot arc does
not work.
When pressing torch
trigger/start switch, pilot arc
starts but “pops out” before
the normal 5 second time-out
period
Machine will not cut material
(does not appear to be
operating at full cutting
power)