Tri Tool 602TSB Clamshell Air User Manual
Page 33
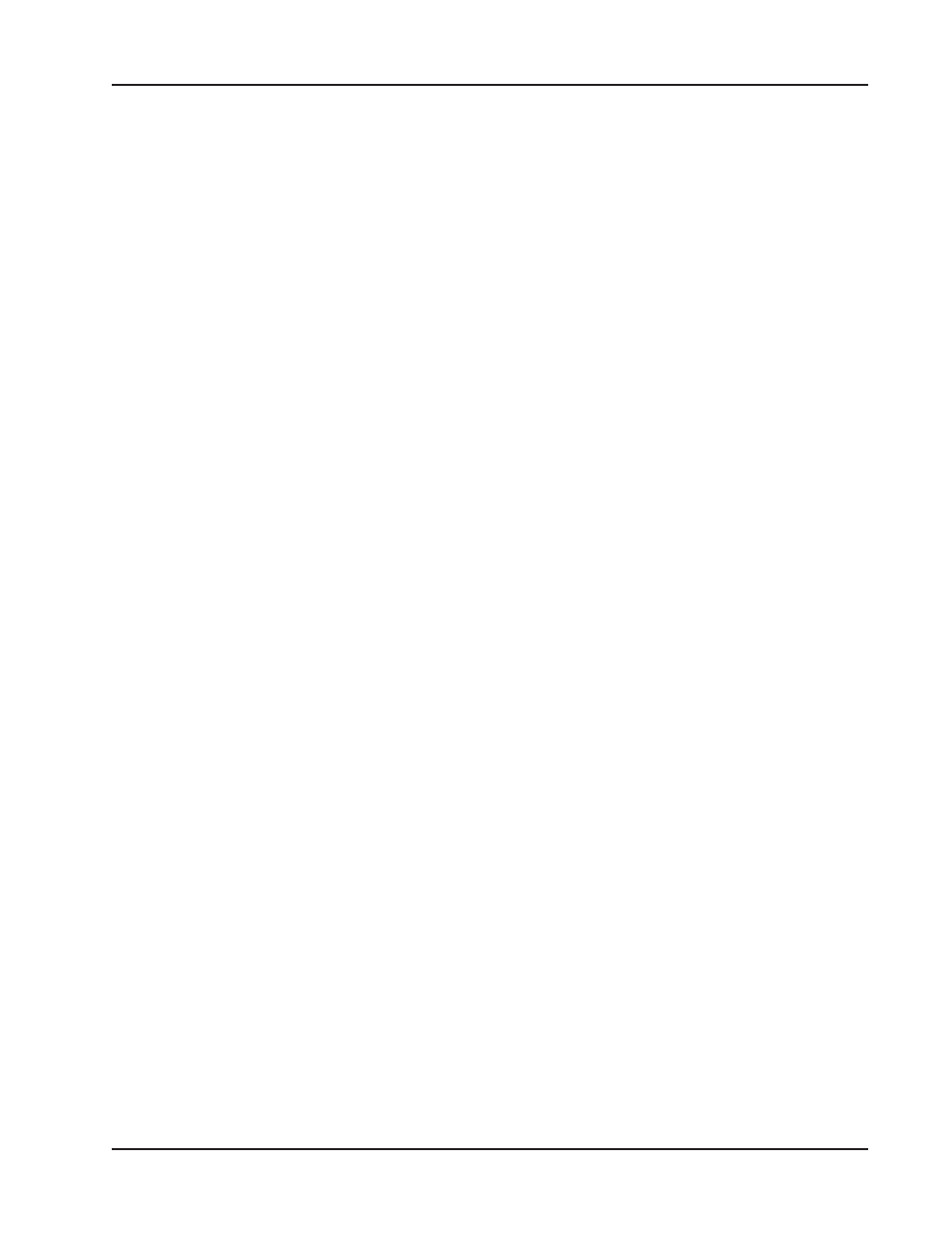
33
Model 602TSB
92-0139 : Rev.131230
Problem:
The Headstock is hard to rotate by hand
Probable causes:
The Air Motor is still engaged.
The Clamping Pads are too tight on the tube.
Foreign material is on the mating surface of the split-lines.
Chips and/or other foreign material are in the rotating section.
The Tool Bit is in contact with the tube.
The Tool Block is in contact with the tube.
The Main Bearing pre-load is too tight.
Problem:
The tool holder is not feeding
Probable causes:
The Feed Pin is broken or out of position.
The Feed Sprocket Shear Pin is broken.
The Feed Screw is stripped.
The Feed Nut is stripped.
The Slide Rails are too tight.
Problem:
There is a loss of air power
Probable causes:
The air supply pressure is too low.
The air filter is plugged.
The air motor is not properly lubricated.
The exhaust is plugged.
The air line size is insufficient.
The air line is too long.
The Motor is icing up because the water trap in the FRL has not been
drained.
Problem:
There is a loss of hydraulic power
Probable causes:
The hydraulic supply pressure is too low.
The hydraulic filter is plugged.
The hydraulic line size is insufficient.
The hydraulic line is too long.
Problem:
The Clamshell is slipping on the tube. (Fixed Pads)
Probable causes:
The Clamping Pads are not in full contact with the tube.
The clamping pressure is too light.
Scale and/or other foreign material is present on the tube.
Weld seams, swelling, or bumps under the Clamping Pads are preventing
full contact.
Dull Tool Bits are causing extra force in the axial and/or radial direction.
The tube wall is too thin which allows the tube wall to flex and the machine
to move.