Pid for trim control – Yaskawa S12051 for GPD 515/G5 User Manual
Page 2
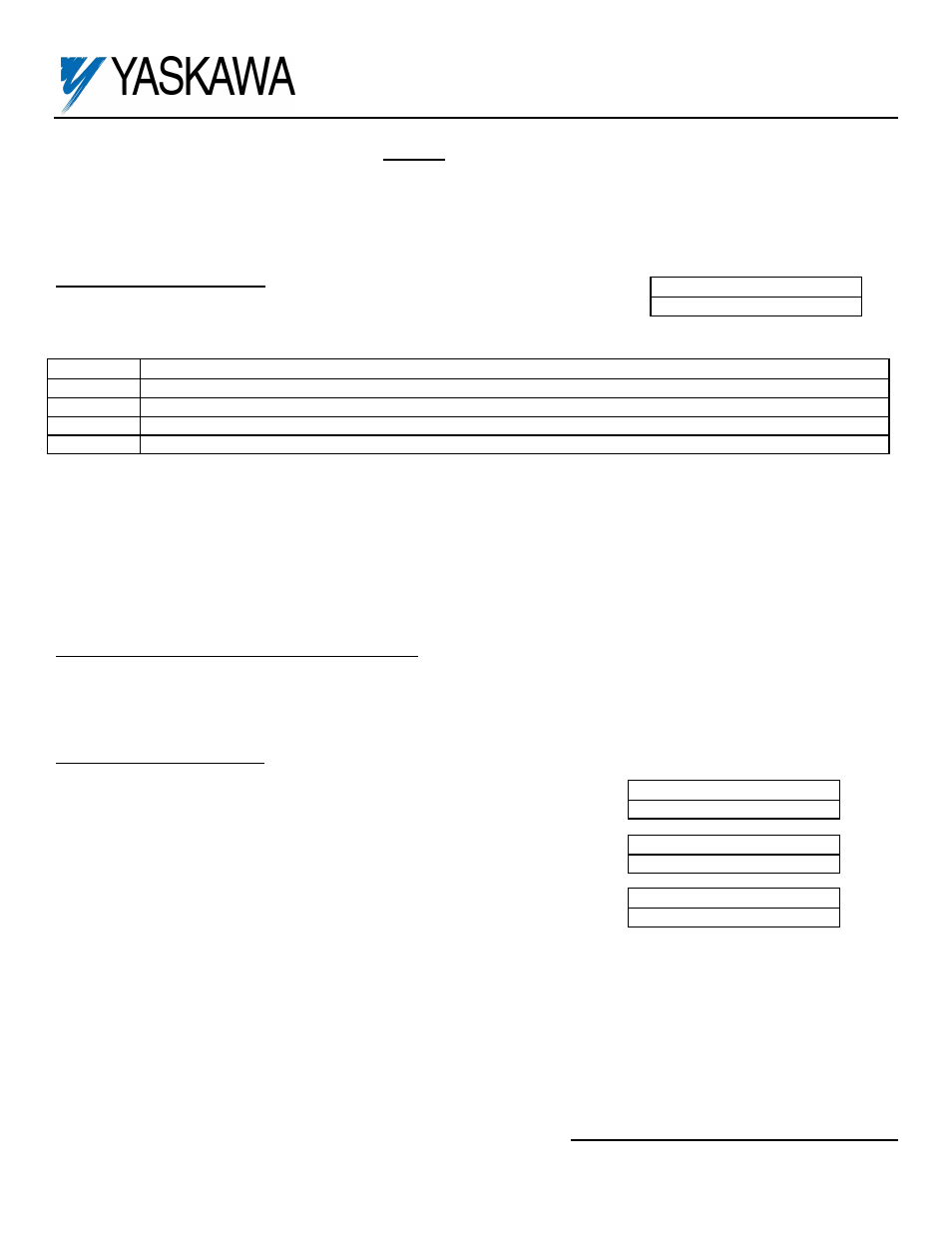
Flash Software-PID for Trim Control
Option S12051 for GPD 515/G5
Yaskawa Electric America, Inc-www.drives.com
02Y00025-0428 Page 2 of 11
Date: 08/23/01
PID For Trim Control
This section replaces section 5.36
(2)
The Proportional, Integral and Derivative control function provides closed-loop control, or regulation of a system process
variable (dancer position, pressure, temperature, etc.). This regulation is accomplished by comparing a feedback signal
to a setpoint reference, which results in an error signal. The PID control algorithm then performs calculations, based upon
the PID parameter settings (b5-01 thru b5-12), on this error signal. The result of the PID algorithm is then used as the
new speed reference, or to trim the existing speed reference.
5.36A. b5-01 : PID Selection
Using this parameter, PID control can be enabled, and the type of PID control can be selected.
Setting Description
0
PID Disabled
1
PID Enabled (Output Only) - PID output becomes the output frequency
2
PID Enabled (Output + Reference) - PID output “trims” the frequency reference
3
PID Enabled (Output + Reference, with accel / decel timer) - PID output “trims” the frequency reference
• If b5-01 is set to 0, no PID function will occur.
• If b5-01 is set to 1, the frequency reference the drive will use will come from the PID control only.
• If b5-01 is set to 2, the frequency reference the drive will use will be the actual frequency reference (Terminal 13 or d1-
01 thru d1-09) plus the output of the PID control. This mode could be used to perform a line speed w/dancer trim
function.
• If b5-01 is set to 3, the frequency reference the drive will use will be the actual frequency reference (Terminal 13 or
d1-01 thru d1-09) plus the output of the PID control. In addition, the accel/decel ramps will change to the settings in
C1-07 & C1-08 after the time specified in b5-08. See description of b5-08 for more details.
5.36B. Line Speed / Frequency Reference Selection
Refer to Section 5.25 - Local/Remote and Reference Selection
(2)
in order to select the line speed. NOTE: in Section 5.25,
the “Auto” speed reference is terminal 13. The “Manual” speed reference is terminal 16, and the “Memory Data” refers to
speed reference parameters d1-01 thru d1-09.
5.36C. PID Setpoint Selection
b5-07: Position Offset
H3-05: Multi-function Analog Input 1
Selection (Term. 16)
H3-09: Multi-function Analog Input 2
Selection (Term. 14)
Select the PID control Setpoint Reference from either the internal digital setting b5-07, or from an analog input (Terminal
16 or 14). Note: if both a digital and an analog setpoint reference are used simultaneously, the two will add together.
• Voltage signal (0 -10 VDC) Terminal 16: Set H3-05 to data “20” and H3-04 to data “0”.
• Voltage signal (-10 to +10 VDC) Terminal 16: Set H3-05 to data “20” and H3-04 to data “1”.
• Current signal (4 to 20 mA) Terminal 14: Set H3-09 to data “20” and H3-08 to data “2”.
• Voltage signal
(3)
(0 -10 VDC) Terminal 14: Set H3-09 to data “20” and H3-04 to data “0”.
•
Voltage signal
(3)
(-10 to +10 VDC) Terminal 14: Set H3-09 to data “20” and H3-04 to data “1”.
(2)
GPD515 Technical Manual TM4515
Factory Setting: 0
Range: 0, 1, 2, 3
Factory Setting: 0.00
Range: -10.00 to +10.00V
Factory Setting: 0
Range: 0 - 21
Factory Setting: 1F
Range: 0 - 21