Flowserve CPXV fitted with Mark 3 ASME hydraulics User Manual
Page 19
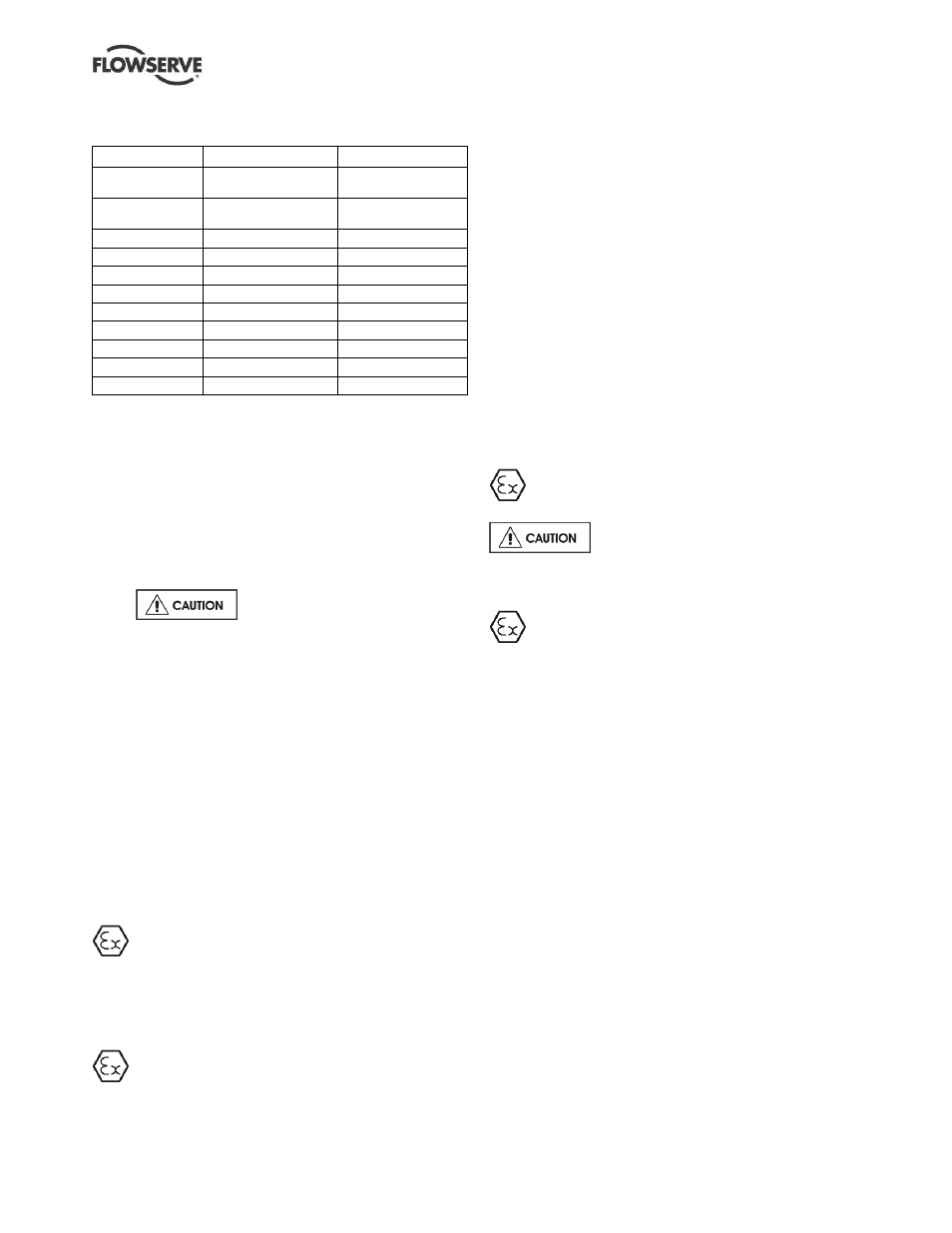
CPXV with Mark 3 ASME hydraulics ENGLISH 71569291 12-14
Page 19 of 44
flowserve.com
5.2.3 Recommended rolling element bearing
grease lubricants
Grease
NLGI 2 *
NLGI 3
Temperature
range
-20 to +100 ºC
(-4 to +212 ºF)
-20 to +100 ºC
(-4 to +212 ºF)
Designation
acc. to DIN
KP2K-25
KP3K-20
BP
Energrease LS-EP2
Energrease LS-EP3
Elf
Multis EP2
Multis EP3
Fuchs
RENOLIT EP2
RENOLIT EP3
Esso
Beacon EP2
Beacon EP3
Mobil
Mobilux EP2
Mobilux EP3 **
Q8
Rembrandt EP2
Rembrandt EP3
Shell
Alvania EP2
Alvania EP3
Texaco
Multifak EP2
Multifak EP3
SKF
LGEP 2
* NLGI 2 is an alternative grease and is not to be mixed with other
grades.
** Standard pre-packed grease for fitted antifriction bearings.
5.2.3.1 Food grade grease (when applicable)
NSF H1 Klubersynth UH1 64-62 is the food grade
grease option and it is NLGI grade 2.
5.2.4 Recommended fill quantities
Refer to section
5.2.2, Rolling element bearing sizes
and grease/oil capacities.
5.2.5
Lubrication schedule
5.2.5.1 Oil lubricated rolling element bearings
Normal oil change intervals are 2 000 operating hours.
For pumps on hot service or in severely damp or
corrosive atmosphere, the oil will require changing more
frequently. Lubricant and bearing temperature analysis
can be useful in optimizing lubricant change intervals.
The lubricating oil should be a high quality mineral oil
having foam inhibitors. Synthetic oils may also be
used if checks show that the rubber oil seals will not be
adversely affected.
The bearing temperature may be allowed to rise to
50 ºC (90 ºF) above ambient, but should not exceed
82 ºC (180 ºF) (API 610 limit). A continuously rising
temperature, or an abrupt rise, indicates a fault.
T5 and T6 temperature classes have more
restrictive temperature control limits, see 5.8.3.
Pumps that handle high temperature liquids may
require their bearings to be cooled to prevent bearing
temperatures exceeding their limits.
T5 and T6 temperature classes have more
restrictive temperature control limits, see 5.8.3.
5.2.5.2 Grease lubricated rolling element bearings
When grease nipples are fitted, one charge between
grease changes is advisable for most operating
conditions; ie 2 000 hours interval. Normal intervals
between grease changes are 4 000 hours or at least
every 6 months
. For food grade grease the grease
change and relubrication intervals are half that of the
conventional greases.
The characteristics of the installation and severity of
service will determine the frequency of lubrication.
Lubricant and bearing temperature analysis can be
useful in optimizing lubricant change intervals.
The bearing temperature may be allowed to rise to
55 ºC (99 ºF) above ambient, but should not exceed
95 ºC (204 ºF). For most operating conditions, a
quality grease having a lithium soap base and NLGI
consistency of No 2 or No 3 is recommended. The
drop point should exceed 175 ºC (350 ºF).
T5 and T6 temperature classes have more
restrictive temperature control limits, see 5.8.3.
Never mix greases containing
different bases, thickeners or additives.
5.2.5.3 Grease lubricated plain line bearings
This option must not be used with ATEX pumps.
Pumps furnished with grease-lubricated shaft
bearings [3300] will leave the factory with lubrication
pipes [3840] shown in section 8.2, and bearings
[3300] already packed with grease. The grease used
will be of a water-resistant nature. A 120 ml (4 oz.)
minimum automatic lubricator [3800] should be
started prior to the pump start-up through their fittings
located above the pump sole plate [6140].
Grease must be insoluble in the liquid being pumped
to be effective. The recommended grease procured
with the automatic lubricators must also be
compatible to that being provided in the lubrication
lines. The normal standard default for an automatic
lubricator is Mobil Mobilith SCH100 NLGI 2 grade
grease or an equivalent, in which case the bearing
lubrication lines are filled with that grease type before
the pump leaves the factory. Check the automatic
lubricator manufacturer’s instructions provided with
the order. Consult local lubricant suppliers for the
type of grease most compatible with the liquid being
pumped.