9 disassembly – Flowserve CPXV fitted with Mark 3 ASME hydraulics User Manual
Page 29
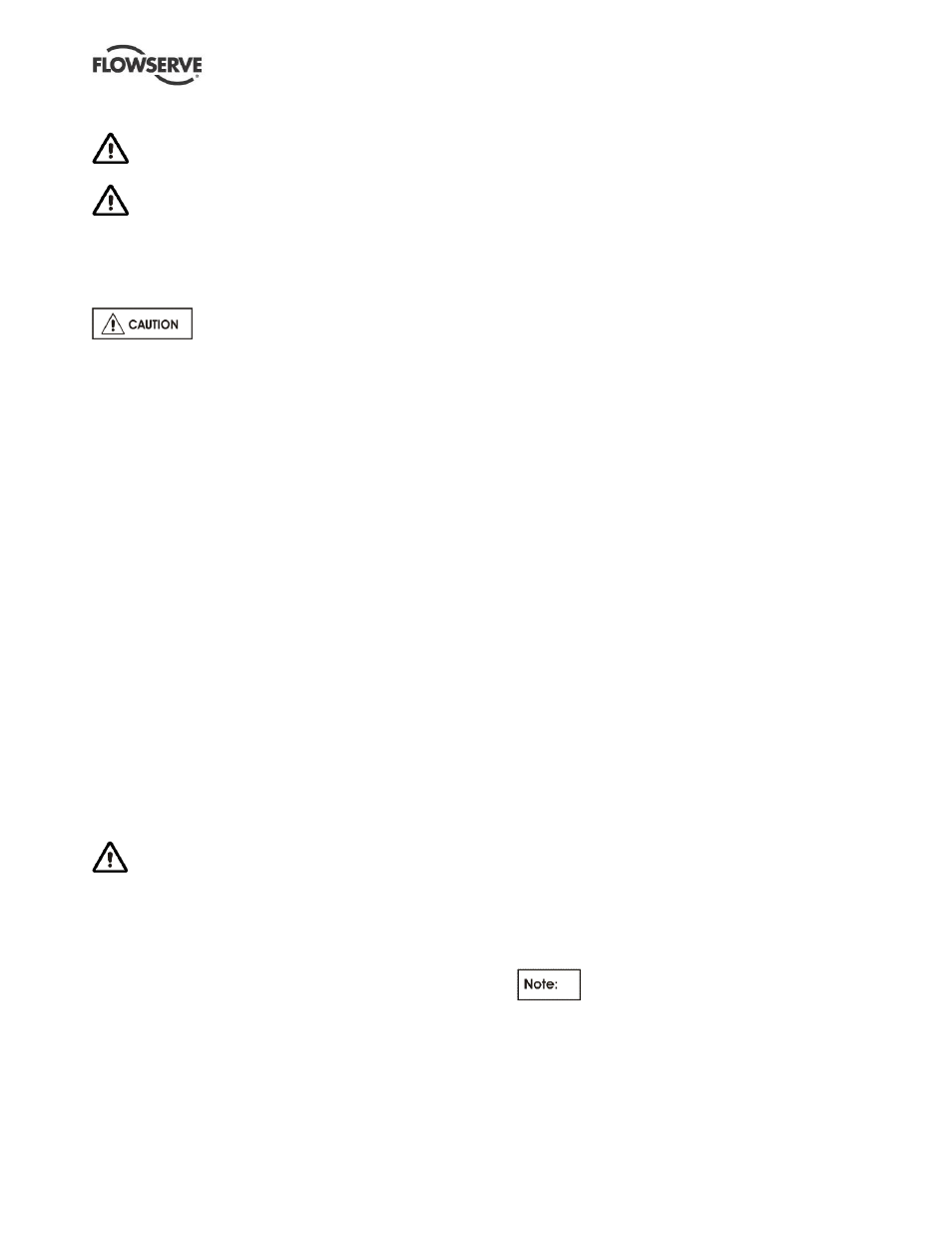
CPXV with Mark 3 ASME hydraulics ENGLISH 71569291 12-14
Page 29 of 44
flowserve.com
6.9 Disassembly
Refer to Safety section before dismantling the
pump.
For pumps with heating jackets, ensure that the
pump is cooled down correctly and sufficiently before
handling. After evacuating the tank and shutting off
the pump, the pumped liquid flows down through the
pump into the sump. After approximately 30 minutes
the heating steam line should be closed.
Before dismantling the pump for
overhaul, ensure genuine Flowserve replacement
parts are available.
Refer to sectional drawings for part numbers and
identification. See section 8, Parts lists and drawings.
6.9.1 Pump disassembly
a) Disconnect all auxiliary pipes and tubes where
applicable.
b)
Disconnect all discharge and auxiliary pipework.
c)
Remove coupling guard, disconnect coupling and
remove motor.
d)
If oil lubricated unit, drain oil.
e)
Remove nuts securing sole plate to foundations
and lift the complete unit clear.
f)
Record the gap between bearing carrier and sole
plate so that this setting can be used during
workshop assembly.
g)
Remove suction pipe and/or strainer if fitted.
h)
Remove all flushing lines as appropriate, casing
screws and discharge flange bolts.
i)
Remove pump casing.
j)
Remove pump casing and discharge flange
gaskets and discard. (A replacement gasket will
be required for assembly.)
k)
Clean the gasket mating surfaces.
6.9.2 Impeller removal (threaded on impeller)
NEVER APPLY HEAT TO REMOVE THE
IMPELLER. TRAPPED OIL OR LUBRICANT MAY
CAUSE AN EXPLOSION
a)
Fit a chain wrench or bolt a bar to the holes in the
coupling half, or fit a keyed shaft wrench directly
to the shaft.
b)
Wearing metal mesh reinforced gloves, rotate the
shaft [2100] by turning the impeller [2200]
clockwise as viewed from the impeller end of the
shaft, so that the wrench makes contact with one
of the supports of the motor pedestal [3160].
c) Give the impeller a quick turn counter-clockwise
so that the wrench handle strikes the other side
of the window edge of the motor pedestal [3160].
A few sharp strikes will loosen one of the shaft
threads. If at this point the impeller is still firmly
threaded to the pump end shaft [2100], then
check in the windows in column pipe above each
inter bearing to see where the threads have
started to disengage.
d)
If the impeller is loose then unscrew it and
discard the impeller O-ring [4610.1]. Use a new
O-ring for assembly.
e)
In case the shaft starts to disengage at another
thread. Loosen screws and nuts [6570.5 and
6580.1] to disconnect the discharge pipe [1360]
from the pump casing [1100].
f)
Ensure both sections of the support column are
well supported. Unscrew the screw and nut
[6570.11 and 6580.2] at the loose joint, and
disengage the lubrication pipe [3840]. Unscrew
the shaft [2100s] taking great care to support
both shaft ends when they disengage to avoid
damaging the line bearings.
g)
Remove the lower section of the support column
and place on a level support structure.
h) If the support column contains at least one inter
bearing, remove the highest column pipe section by
removing the screw and nut [6570.11 and 6580.2]
and the lubrication pipe [3840]. Then slide the
support pipe and line bearing assembly over the
shaft while ensuring the shaft is well supported.
Remove the free section of shaft [2100]. Repeat
the above until only the lowest section of the
support column pipe [1350] remains.
i)
Fix the lowest section of the support column on a
workbench. Fit a spanner to the flats of the
upper end of the shaft and ensure it can not slip.
j)
Fit a strap wrench around the impeller and spin
the impeller clockwise to lift the spanner from the
work bench.
k) Spin the impeller quickly counter-clockwise with
the wrench to get the spanner to make impact on
the workbench or a wooden block. The impact
will loosen the impeller.
l)
Unscrew the impeller and discard the impeller
O-ring [4610.1]. Use a new O-ring for assembly.
6.9.3 Support columns, shafts and bearings
a)
Remove the two screws which fix the lower
bearing carrier to the lower support column.
b)
Remove the lower bearing carrier.
If silicon carbide, carbon or high graphite
iron bearings are fitted extreme care should be taken
to avoid chipping or cracking these relatively brittle
components.
c)
Unbolt and remove support column(s).
d)
Unscrew the overhanging shaft section prior to
removing the next section of support column.