Flowserve CPXV fitted with Mark 3 ASME hydraulics User Manual
Page 8
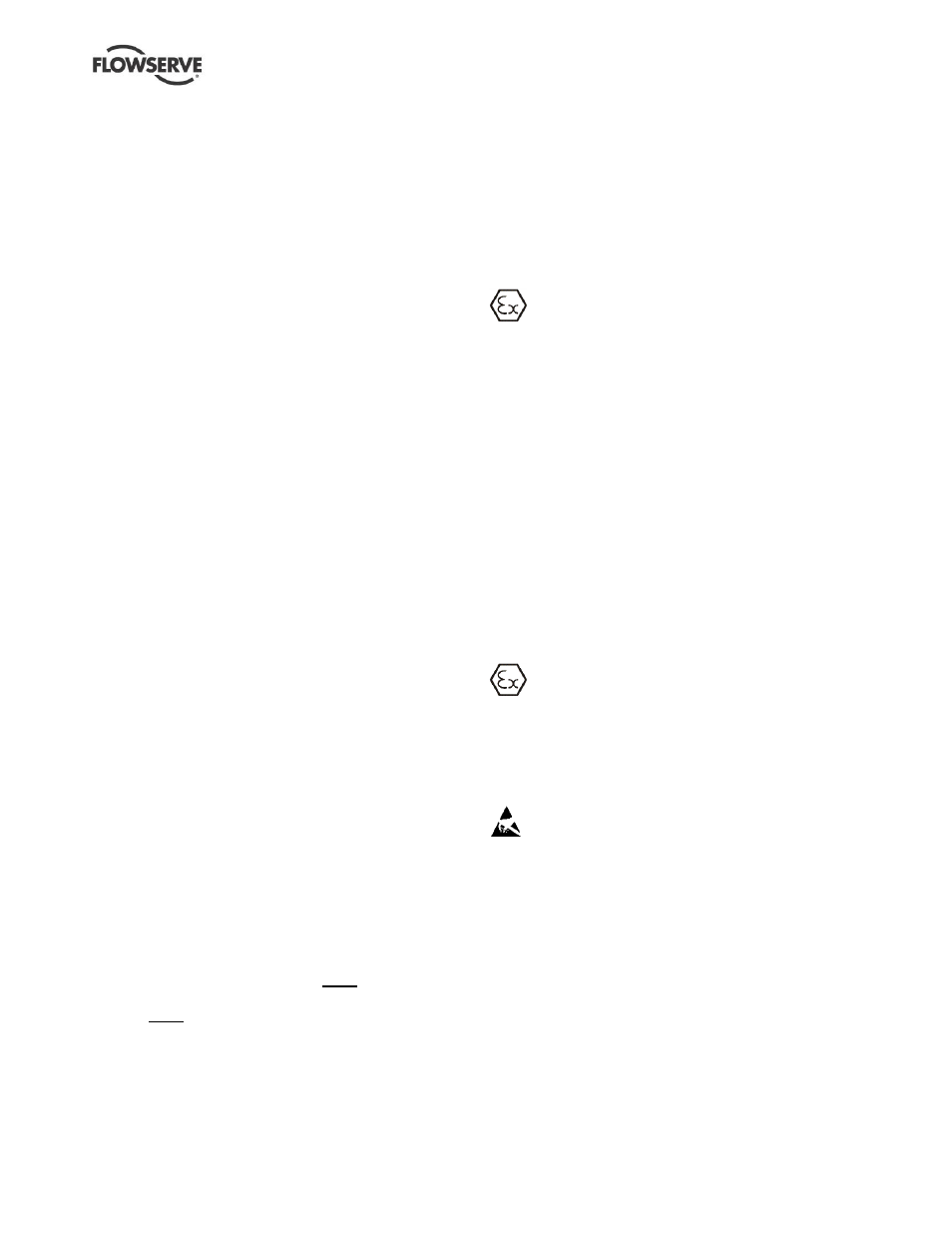
CPXV with Mark 3 ASME hydraulics ENGLISH 71569291 12-14
Page 8 of 44
flowserve.com
Where there is any risk of the pump being run against
a closed valve generating high liquid and casing
external surface temperatures fit an external surface
temperature protection device.
Avoid mechanical, hydraulic or electrical overload by
using motor overload trips, a temperature or power
monitor and make routine vibration monitoring checks.
In dirty or dusty environments, regular checks must
be made and dirt removed from areas around close
clearances, bearing housings and motors.
The equipment utilises polymer based seals and
bearing surfaces that could be corroded if they
are in contact with unsuitable liquids or gases.
These surfaces are important for the operation of
the pump. Contact Flowserve if you are uncertain
about the performance of these materials with
respect to aggressive substances that may be
present in the hazardous area.
The pump casing must be flooded with liquid to the
minimum level on the dimensional General
Arrangement (GA) drawing, at any time that the pump
is operated. On pumps furnished to Group II
Category 1 below the sole plate, monitoring of the
level with a pump cut out on low level is required.
Where there is the potential hazard of a loss of a seal
barrier fluid the barrier fluid system must be monitored.
Where there is a risk that the external flush to a seal or
bearing could fail, for example by freezing, blocking by
debris or loss of supply pressure, then the flow must be
monitored.
Where there is product flush via filters then flow must
be monitored.
Visual indicators are suitable when equipment is
regulary inspected, but sensors connected to the pump
control system must be used if the pump runs remotely.
For Category 2 equipment the monitoring must create
an alarm to the plant operator or shut down the pump.
For equipment to category 1/2 or 1/3 with external flush
or filtered product flush, the flow to each line bearing
must be separately monitored and temperature sensors
fitted on each line bearing that is connected to the
pump control system. The monitoring equipment must
be suitable for the hazardous area.
For equipment to category 1/2 or 1/3 the presence of
seal barrier liquid and the temperature of the inboard
seal must both be monitored and connected to the
pump control to create an alarm signal to the operator,
or to shut down the pump.
See also sections 5.8.2 to 5.8.6.
1.6.4.4 Preventing the build-up of explosive
mixtures
ENSURE THE PUMP IS PROPERLY FILLED
AND VENTED AND DOES NOT RUN DRY
Ensure the pump and relevant suction and discharge
pipeline system is totally filled with liquid at all times
during the pump operation, so that an explosive
atmosphere is prevented. In addition it is essential to
make sure that seal chambers, auxiliary shaft seal
systems and any heating and cooling systems are
properly filled.
If the operation of the system cannot avoid this
condition, fit an appropriate dry run protection device
(for example liquid detection or a power monitor).
To avoid potential hazards from fugitive emissions of
vapor or gas to atmosphere the surrounding area
must be well ventilated.
1.6.4.5 Preventing sparks
To prevent a potential hazard from mechanical
contact, the coupling guard must be non-sparking
and anti-static for Category 2.
To avoid the potential hazard from random induced
current generating a spark, the earth contact on the
baseplate must be used.
Avoid electrostatic charge: do not rub non-metallic
surfaces with a dry cloth; ensure cloth is damp.
For ATEX the coupling must be selected to comply with
the requirements of European Directive 2014/34/EU
(previously 94/9/EC which remains valid until 20 April
2016 during the transition). Correct coupling alignment
must be maintained.