3 open impeller clearance, Direction of rotation, 5 guarding – Flowserve CPXV fitted with Mark 3 ASME hydraulics User Manual
Page 20: Priming and auxiliary supplies, Guarding (5.5), 4 direction of rotation, 6 priming and auxiliary supplies
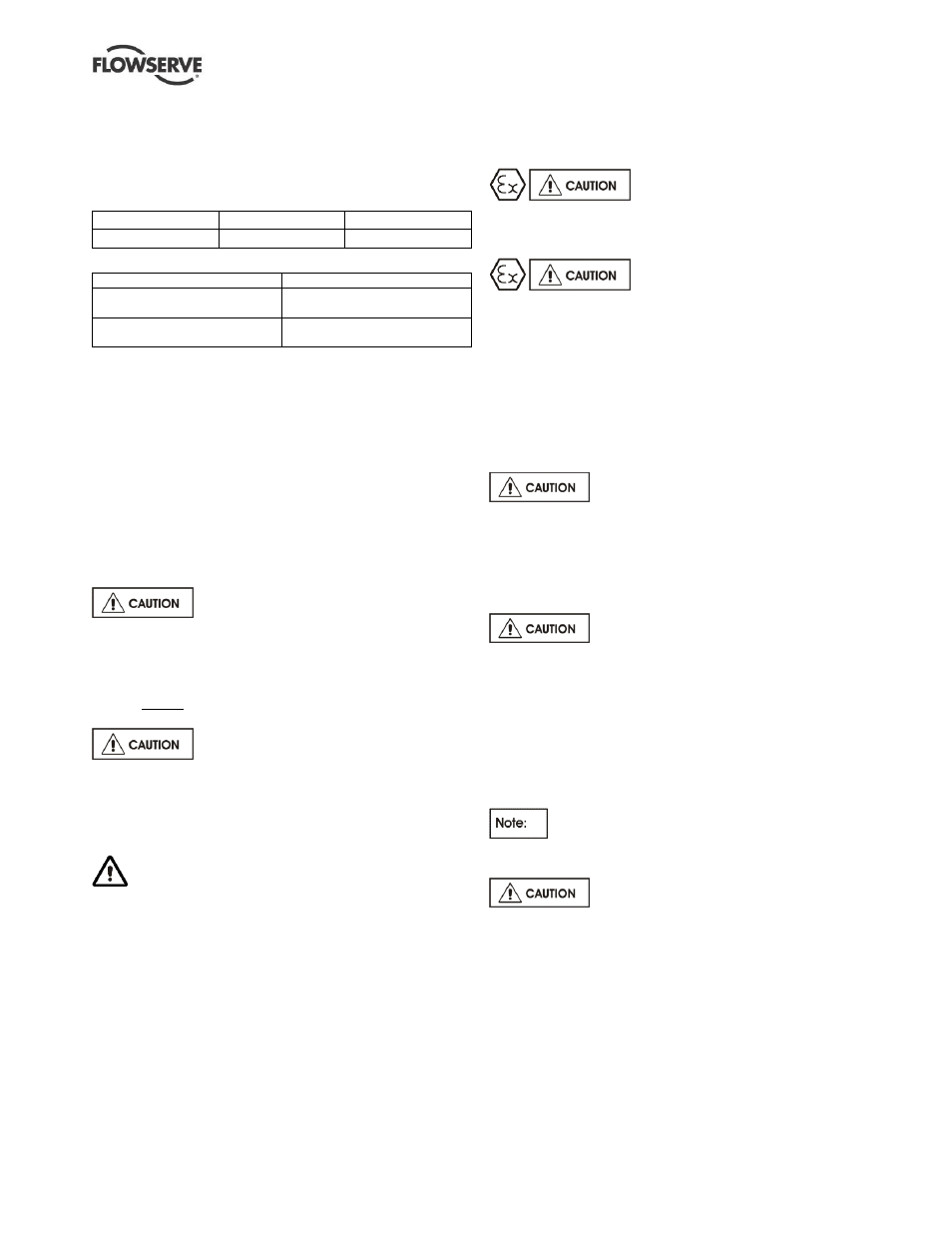
CPXV with Mark 3 ASME hydraulics ENGLISH 71569291 12-14
Page 20 of 44
flowserve.com
Grease lubricated line bearings require frequent
lubrication. Grease lubricating systems may be utilized.
Follow the automatic lubricator manufacturer’s
instructions for proper use. General lubrication intervals
and amounts are shown in the tables below.
Service
Clean
Contains abrasives
Interval *
8 hours
4
– 6 hours
* Interval depends on process conditions
Location
Amount
Intermediate bearings [3020.1]
18 ml or 18 g (0.625 oz.)
per interval
Bottom bearings [3020.2]
11 ml or 11 g (0.375 oz.)
per interval
Flowserve offers one system for the CPXV consisting
of individual 120 ml (4 oz.) minimum automatic
lubricators per line shaft. Consult your Flowserve
representative for additional information.
5.3 Open impeller clearance
The impeller clearance is set in the factory. This may
require adjustment because of piping attachment or
increase in temperatures. For setting instructions see
section 6.7, Setting impeller clearance.
5.4
Direction of rotation
Serious damage can result if the pump
is started or run in the wrong direction of rotation.
The pump is shipped with the coupling element
removed. Ensure the direction of rotation of the motor is
correct before fitting the coupling element. Direction of
rotation must correspond to the direction arrow.
If maintenance work has been carried
out to the site's electricity supply, the direction of
rotation should be re-checked as above in case the
supply phasing has been altered.
5.5 Guarding
Guarding is supplied fitted to the pump set.
Fasteners for guards must remain captive in the guard
to comply with the Machinery Directive 2006/42/EC.
When releasing guards, the fasteners must be
unscrewed in an appropriate way to ensure that the
fasteners remain captive.
Whenever guarding is removed or disturbed ensure
that all the protective guards are securely refitted prior
to start-up.
5.6
Priming and auxiliary supplies
5.6.1 Filling and priming
.
The pump end needs to be
completely submerged in the product.
5.6.2 Auxiliary supplies
.
Ensure all electrical, hydraulic,
pneumatic, sealant and lubrication systems (as
applicable) are connected and operational.
5.6.2.1 Agitation system
Where an agitation system is provided this should be
used prior to and during start up, supplied by a 23 m
3
/h
(100 US gpm) water inlet at 3.5 - 4 barg (50 - 60 psig).
5.6.3 Pumps fitted with a heating jacket on
molten sulphur pumps
The pump should be pre-heated for at
least one hour using steam through the heating jacket
before hot liquid is brought into the pump. The
quantity, temperature and pressure can be obtained
from the dimensional drawing. This action is
important to avoid distortion and maintain the gap
between impeller and casing.
Ensure pump is electrically isolated.
Then, before starting the driver, rotate the shaft
several times by (thermal gloved) hand to ensure
freedom of rotation as the high temperature will
cause expansion and the increase in lengths of the
components should be identical.
5.6.4 Pumps with rigid coupling on high
temperature service fitted with cooling fan and
heat sink (eg for molten salt)
These instructions already assume that any
vertical expansion bellows have been installed and
adjusted prior to installation of the pump assembly.
There are no constraints on the time
required to lower the pump into the tank but allow three
to four hours for bringing the pump unit to the required
temperature. (Minimum time required specified is
between placing the pump in place and the point of
starting the pump.) Standard safety procedures must
be followed. Pump can be installed and removed at any
liquid level; however, the spacer coupling above the
pump thrust bearing must be removed prior to this and
the impeller clearance must be wide so that the rotor
can be free to move axially in both directions.