Flowserve CPXV fitted with Mark 3 ASME hydraulics User Manual
Page 31
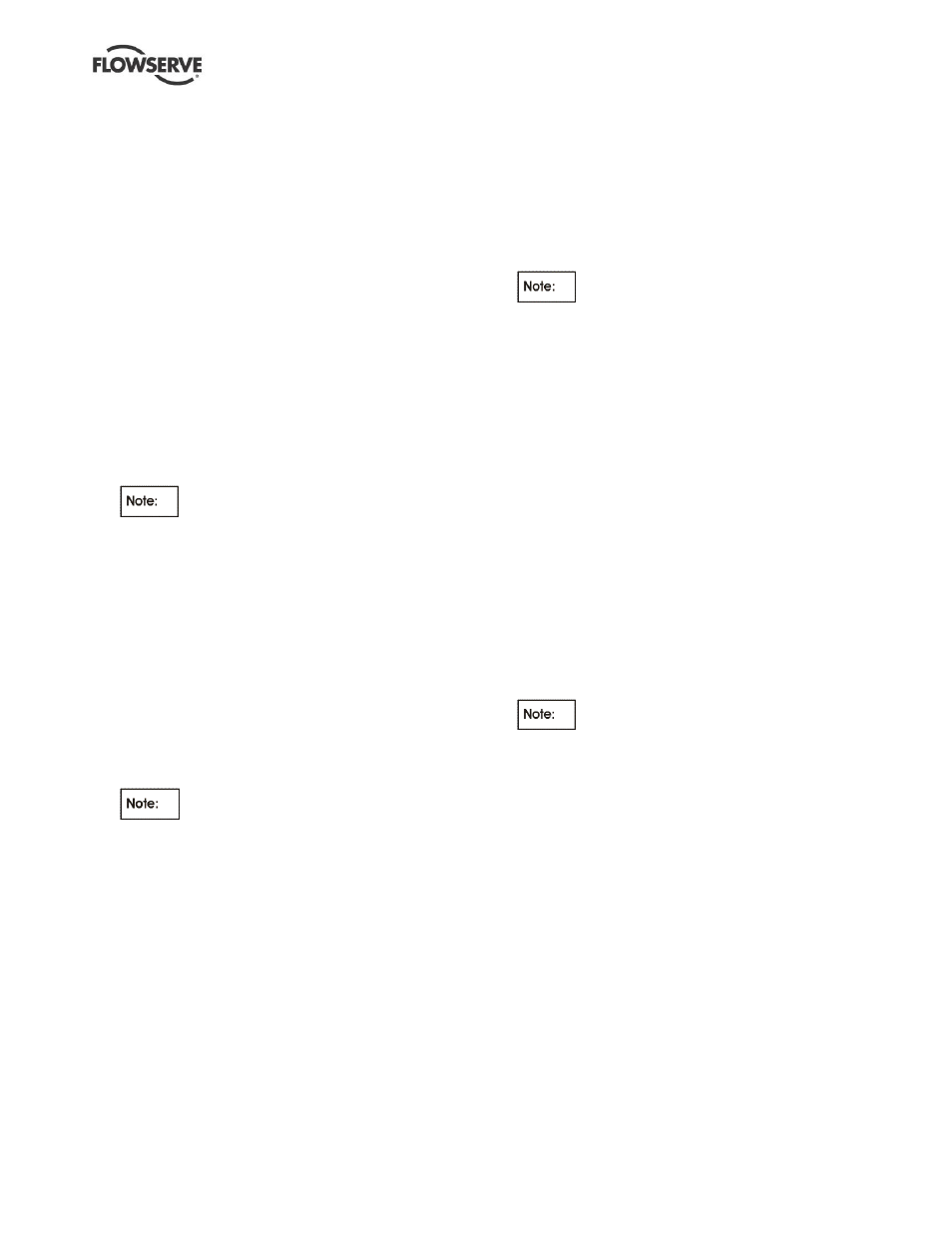
CPXV with Mark 3 ASME hydraulics ENGLISH 71569291 12-14
Page 31 of 44
flowserve.com
c) The bearing carrier retaining ring sub-assembly and
bearing sleeve [2471], applicable on shaft sizes 3
and 4, should now be placed over the shaft before
fitting the thrust bearing. The retaining ring must
have the C spanner slots facing the impeller end.
(Note 1: On units fitted with a proprietary sole
plate mechanical seal, this and any additional
housing should be passed over the shaft before
the thrust bearing outer nut.)
(Note 2: In the case of a proprietary PTFE vapor
seal, this is fitted into the locking ring as a
subassembly. Place the thrust bearing [3013] on
to the shaft. If an optional pair of thrust bearings
is to be fitted, these must be mounted back-to-
back, as described below.)
d)
Press the thrust bearing(s) [3013] onto the shaft
using equipment that can provide a steady, even
load to the inner race.
e)
Oil bath lubricated thrust bearing is an option.
f)
If grease lubrication as standard, use a spatula to fill
sides of the bearing with grease of NLGI 3 grade.
On aggressive solvent/acid vapor service
a special fluoro-silicone grease (Molykote FS3451)
may be required. Pack the bearing fully by hand as
no grease nipple is used in the design.
g)
Fit the self-locking thrust bearing nut [3712.1]
onto the shaft and tighten with a C spanner.
h) Fit O-ring [4610.2] on bearing carrier [3240] and
lubricate bearing carrier bore and O-ring with oil.
i)
Ensure the shaft coupling keyway edges are free of
burrs. If optional proprietary labyrinth type bearing
housing seals [4330] are used the O-rings should
be oiled to assist assembly.
j)
Install the bearing carrier onto the shaft/bearing
assembly and screw the bearing carrier locking
ring into the bearing carrier. Tighten up the
bearing carrier locking ring using a C spanner.
LH thread.
k)
Check shaft [2100] for free rotation.
l)
Units with an oil lubricated bearing housing may be
fitted with shim-packs between the motor pedestal
[3160.1] and motor pedestal spacer [3160.1]. The
shim-packs are factory set to ensure alignment
between pump and motor shafts and should be re-
fitted in their original positions.
m)
To fit an inter bearing shaft sleeve [3400.2], slide
it over the shaft from the impeller end and tighten
up the sleeve drive screw [6570.4].
n)
To fit the pump end sleeve [2400.1], slide it over
the shaft; this is driven by the impeller.
6.11.3 Bearing bushes
a)
If the pit depth and pump speed are such that an
intermediate bearing bush [3300.2] is fitted, this
is pressed into the upper support column. The
pump end bush [3300.1] is fitted into the pump
end bush carrier [3245].
b)
When fitting the intermediate bearing bush or
pump end bearing bush these must be pressed in
so that the chamfered end goes in first.
The orientation must be checked so that
the locking pegs [6570.10] line up correctly.
6.11.3.1 Grease lubricated line bearing bushes
a) The shaft seal ring [4305.4 & 4305.5] is fitted at
each end of the bearing bush [3300]. The curved
lips of the shaft seal ring are assembled to face
outwards from the bearing bush to control the
grease flow.
b) The screws [6570.17 & 6570.16] must be fitted and
torqued up according to section 6.6 to ensure
retaining rings [2530.1 & 2530.2] prevent each shaft
seal ring [4305.4 & 4305.5] from rotating.
6.11.4 Installing the shaft sub-assembly
a) Prior to assembling the shaft sub-assembly into the
sole plate, first fasten on the upper suspension
pipe/bearing bush sub-assembly to the sole plate.
b) If the sump is short there may only be a lower
suspension pipe [1350.4]. In this case, the lower
suspension pipe and the pump end bearing
carrier/bush will need to be fitted to the sole plate
to support the shaft sub-assembly.
If there is an upper suspension pipe
[1350.1], the lower suspension pipe and pump end
bearing bush carrier should only be fitted after the
shaft sub-assembly. Install the shaft assembly
into the motor stool and sole plate until the gap
(above), is approximately 4 mm (0.16 in.).
c)
Install the bearing carrier hexagon screws
[6570.7] and the hexagon screws [6570.8] and
hexagon nuts [6580.5], but do not tighten.
d) Press the flinger [2540.2] onto the shaft, where
applicable. This should be set between 0.5 and
2 mm (0.02 and 0.08 in.) from the bearing carrier.
e)
Turn the shaft [2100] to check for freedom from
rubbing.
f)
Refit the coupling [7000].