2 gate valve limitations, 3 globe valve limitations, 4 check valve limitations – Flowserve Vogt Forged Steel Gate User Manual
Page 12: 5 pressure/temperature rating, 6 bending strength
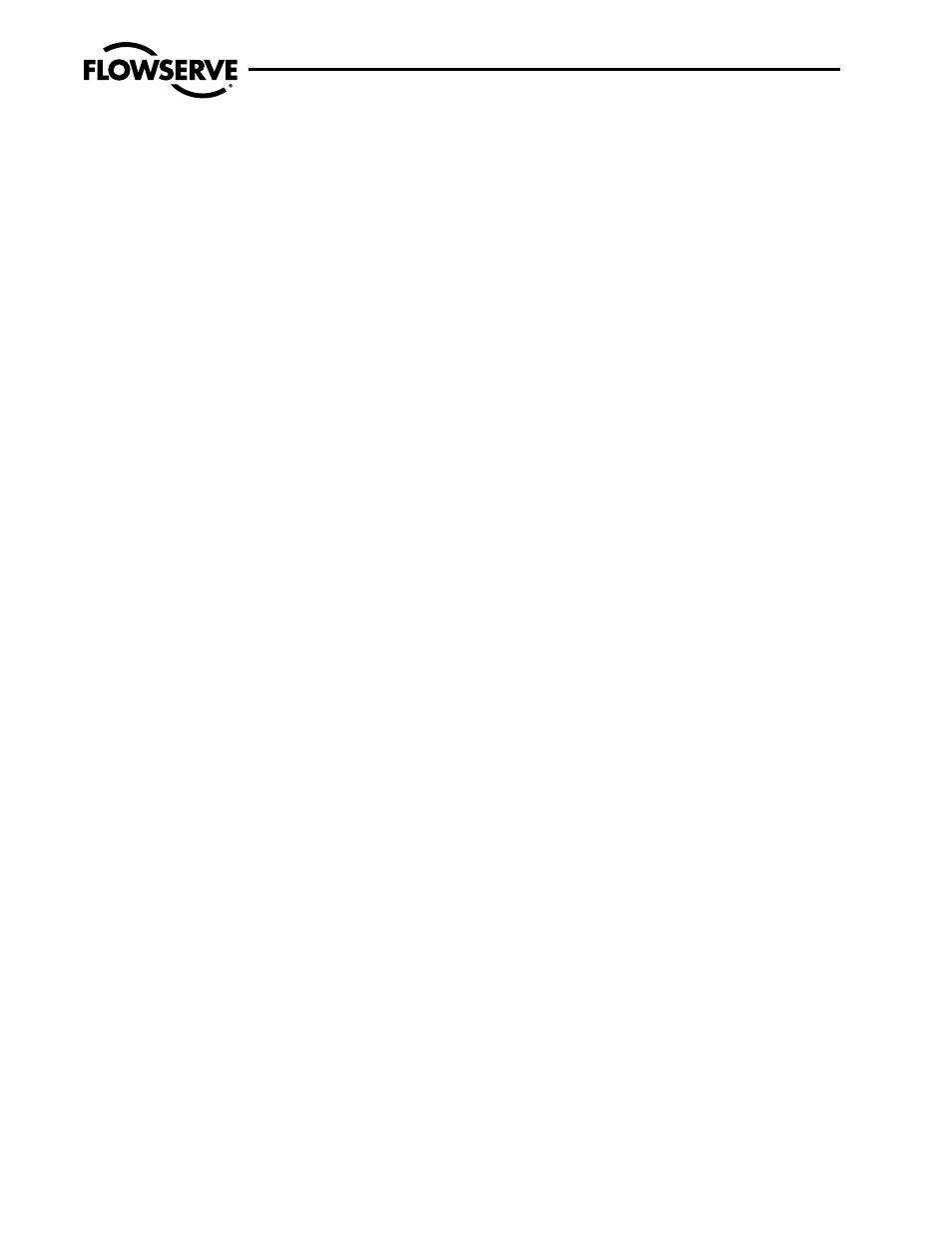
Flow Control
Vogt Valves
12
Forged Steel Gate, Globe and Check Valves
FCD VVENIM2000-02
2.2 Gate Valve Limitations
• Do not use for flow regulation or throttling.
• Do not use if frequent manual operation is required.
• Do not use for slurries or fluids containing solids that can build up
in valve cavities.
• When packed or gasketed with low melting point materials such
as fluoropolymer the full shell pressure/temperature rating and
fire-safe design are sacrificed.
• Locked-in volume when closed.
2.3 Globe Valve Limitations
• Do not use if full flow at minimal pressure drop is required.
• Do not use for slurries or fluids containing solids that can build up
in valve cavities.
• When packed or gasketed with low melting point materials such
as fluoropolymer the full shell pressure/temperature rating and
fire-safe design are sacrificed.
2.4 Check Valve Limitations
• Must be installed to agree with flow arrow on body.
• Zero leakage of metal-to-metal check valves cannot be readily
achieved without an elastomeric element in the seating arrange-
ment.
• Sizing and pressure drop is critical to ensure full lift of valve
piston.
• Use swing check valve design for “boiler feedwater” and other
services where internal rusting may occur in service.
• Use spring-controlled lift check valve for compressor service.
• Size non-spring control lift check valves so that a minimum 2 psi
pressure drop is achieved.
• Size swing check valve so that a minimum 0.5 psi drop is
achieved.
• Use swing check valves when maximum flow at minimal pressure
drop desired.
• Do not use for slurries or fluids containing solids that can build up
in valve cavities.
• When gasketed with low melting point materials such as fluo-
ropolymer the full shell pressure/temperature rating and fire-safe
design are sacrificed.
2.5 Pressure/Temperature Rating
Proper selection of the pressure/temperature rating of the valve
shall meet service requirements. If the valve application involves
temperatures above 100°F (38°C), then the valve pressure rating at
the service temperature must be verified to meet the requirements of
the application.
If system testing will subject the valve to a pressure in excess of
its working pressure rating, then the intended testing pressure and
a statement explaining whether the test pressure is through the
opened valve or a differential across the closed valve, should be
included in the purchase specification.
Source Reference for Vogt valves pressure/temperature ratings
ASME B16.34 Valves, Flanged, Threaded, and Welded End
VVACT0000, Vogt Catalog.
2.6 Bending Strength
Piping systems are subject to mechanical constraints at fixed
support points such as rigid nozzles, anchors, etc. Cold springing
at assembly, system temperature changes, together with gravity,
possible inertia loads, landslides, non-uniform subsidence in buried
lines, etc., all potentially affect the bending moment at various points
in the piping.
(1)
Valves are also subjected to the bending moment occurring in the
adjacent pipe that is in addition to the normal pressure loading.
Bending loads can cause deformation in valve bodies that can be det-
rimental to valve performance. It is therefore a recommended design
practice to avoid locating valves at points of large bending loads.
(1)
Class 150, 300, 600 and 800 Vogt valves have bodies with a nozzle
section modulus (I/C) greater than Schedule 80 pipe. Class 1500
Vogt valve bodies have I/C section modulus greater than that of
Schedule 160 pipe. If the connecting pipe meets the above or has
a lesser wall thickness, it is expected that the piping would be the
weaker element when connected to a Vogt valve and exposed to a
bending load. If the schedule pipe to be used with the Vogt valves are
greater than the above (pipe has a heavier wall thickness), the pur-
chase order shall denote this and Flowserve will provide an I/C sec-
tion modulus calculation for the valve body/adjoining pipe to ensure
the piping is the weaker element, or will advise customer otherwise.
(1)
Paragraph extracted from MSS SP 92.