Flowserve Vogt Forged Steel Gate User Manual
Page 33
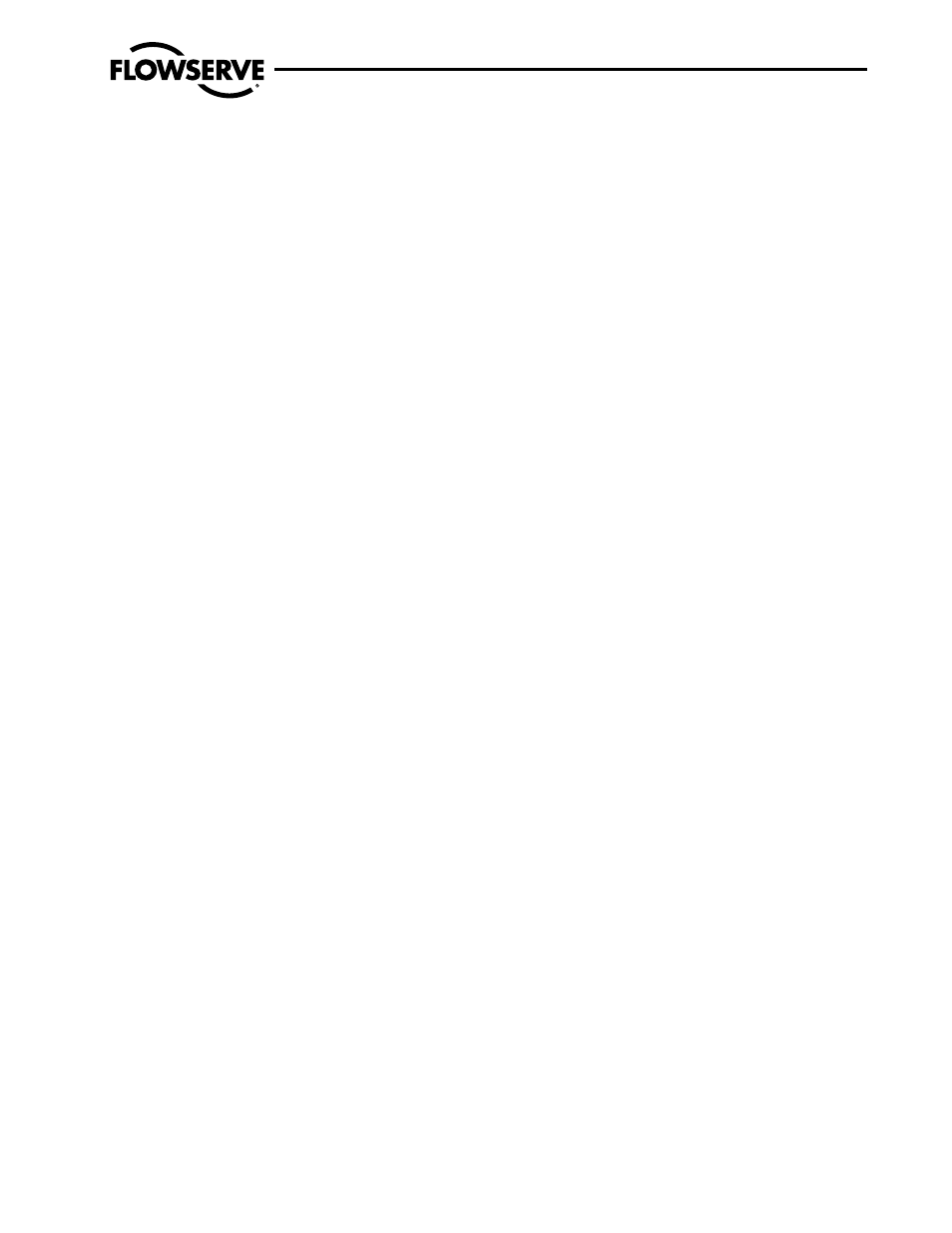
Flow Control
Vogt Valves
FCD VVENIM2000-02
Forged Steel Gate, Globe and Check Valves
33
12. Rotate stem to engage yoke nut thread. Stem should be rotated
until stem broach is visible and the handwheel can be placed on
the stem. Replace nameplate and handwheel nut, tighten nut.
13. Insert new bonnet gasket.
14. Place yoke/bonnet subassembly on valve and replace bonnet
bolting.
15. Replace bonnet bolts and torque bonnet bolts until bonnet joint
becomes metal-tometal. A .007" feeler gage may be used to
gage joint. A bonnet/body joint that will accept a .007" feeler
gage is not properly torqued and is not metal-to-metal. Ad-
ditional torque should be applied.
a
CAUTION: During the torquing of the bonnet joint, the
valve should be slightly open. This will prevent the bon-
net bolt torque from driving the disc into the valve seat
and will ensure the bonnet joint will go metal-to-metal.
16. Tighten packing gland bolting evenly.
17. Open and close valve to ensure free operation.
18. Place valve back in service.
Alternate Method
(No Major Disassembly Required)
1. Remove packing gland bolting and free up packing gland.
2. Remove top ring of packing. This will be a braided graphite pack-
ing. Prepare chamber to accept new ring or rings of packing.
3. Split a number of packing rings of flexible graphite as required
and place individual rings in packing chamber using the gland to
ram the packing into the chamber. Stagger packing ring’s sepa-
rations by 90° if more than one ring is required. Replace top
ring of braided graphite packing as required. If total replacement
of packing is necessary, a bottom ring of braided packing shall
be used.
4. Tighten packing gland bolting evenly.
5. Open and close valve to ensure free operation.
6. Place valve back in service.
O.S. and Y. Welded Bonnet Gate Valves
(Typical Series 2801)
Preferred Method (Requires Disassembly of
Yoke/Bonnet Subassembly)
1. Loosen packing gland bolting and free up gland.
2. Remove tack weld(s) at yoke/bonnet interface. A hammer and a
sharp chisel should be utilized for this operation.
3. Remove yoke/handwheel assembly from yoke/bonnet
subassembly.
a
CAUTION: The stem should be maintained in a near
open position to ensure that the yoke/bonnet thread
and the stem thread difference do not create a condition
where the stem is locked against the backseat, making
removal of the yoke impossible.
4. Remove top ring of packing. This will be a braided graphite
packing. Remove additional packing as required.
5. Add new rings of flexible graphite packing and one new top ring
of braided graphite packing as required. If total replacement of
packing is necessary, a bottom ring of braided packing shall be
used.
6. Replace yoke/handwheel assembly to bonnet subassembly.
a
CAUTION: When replacing yoke/handwheel assem-
bly, the valve stem should be maintained in an open
position to ensure the yoke thread advance does not
drive the gate into the seats potentially making the yoke
replacement impossible.
7. Tighten packing gland bolting evenly.
8. Tack weld yoke/bonnet subassembly at or near same location
from which tack weld was removed. Tack weld in accordance
with the manufacturer’s recommended procedure.
9. Open and close valve to ensure free operation.
10. Place valve back in service.
Alternate Method
(No Major Disassembly Required)
1. Remove packing gland bolting and free up packing gland.
2. Remove top ring of packing. This will be a braided graphite pack-
ing. Prepare chamber to accept new rings or rings of packing.
3. Split a number of packing rings of flexible graphite as required
and place individual rings in packing chamber using the gland
to ram the packing into the chamber. Stagger packing ring’s
separations by 90° if more than one ring is required. Replace
top ring of braided graphite ring as required. If total replacement
of packing is necessary, a bottom ring of braided packing shall
be used.
4. Tighten packing gland bolting evenly.
5. Open and close valve to ensure free operation.
6. Place valve back in service.