Vogt valves – Flowserve Vogt Forged Steel Gate User Manual
Page 39
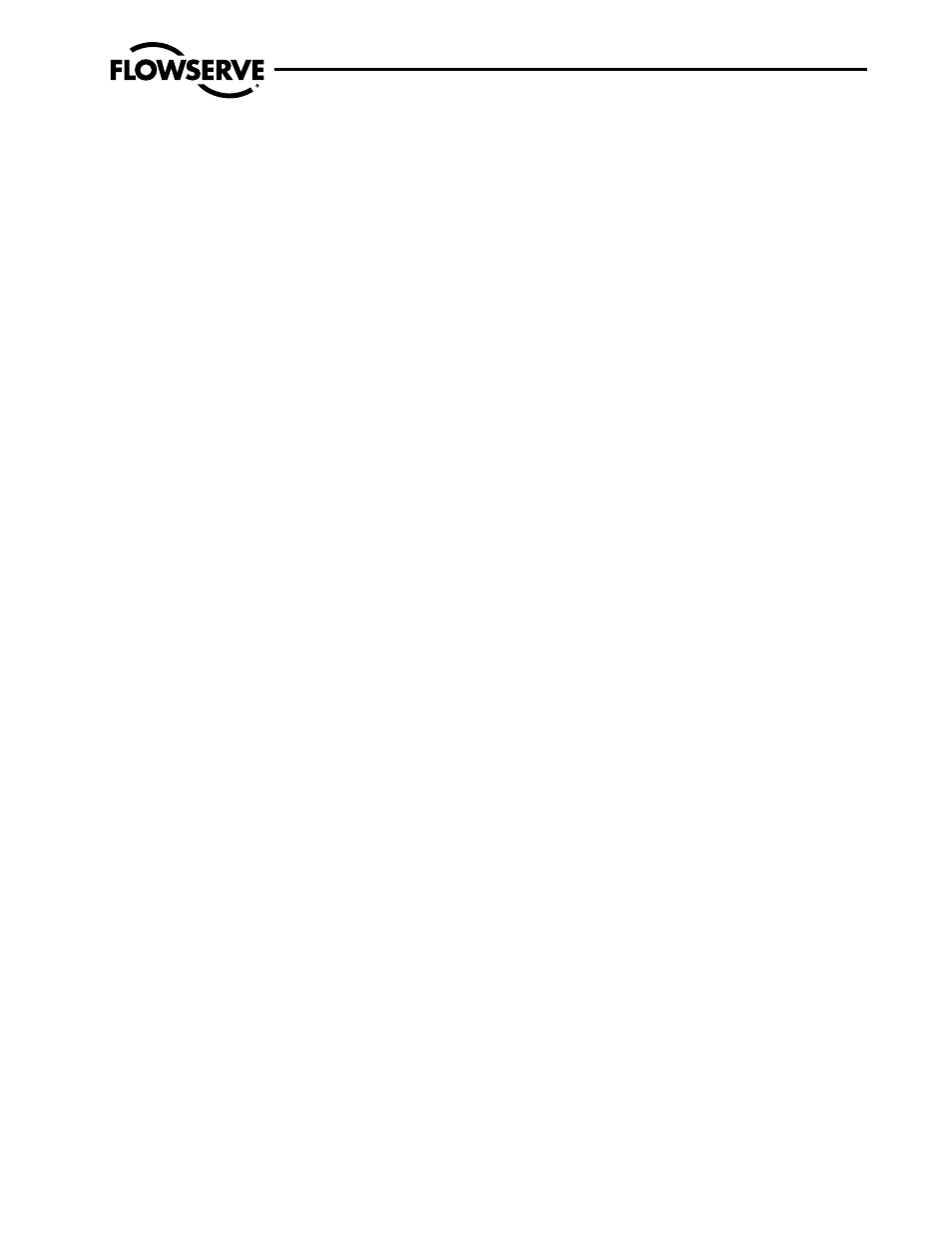
Flow Control
Vogt Valves
FCD VVENIM2000-02
Forged Steel Gate, Globe and Check Valves
39
a
CAUTION
1. The system pressure shall be totally isolated and
vented from the valve to ensure that the valve is at
zero pressure while being repaired.
2. For small valves valve replacement may be the most
economical way to facilitate repair.
Bonnet Gasket Leaker
1. Remove bonnet subassembly. Four or eight bonnet bolts must
be removed to remove the bonnet subassembly.
2. Clean and inspect gasket recess and gasket surface on the
bonnet. Erosion in the gasket seating area greater than 0.030"
deep will require the valve body and/or bonnet to be replaced. A
machining allowance of 0.030" is allowed to refurbish the gasket
seating area of the bonnet and/or body.
a
CAUTION: Ensure that any metal removed from the
depth of the body gasket recess is duplicated by remov-
ing the same amount from the top of the body. This is
required to ensure that the depth of the gasket recess
(0.095–0.100") in the body is maintained.
The bonnet gasket surface depth can be machined by up to
0.030" without damage to the valve. Bonnet gasket surface
removal shall be across the full surface of the bonnet that
contacts the gasket and body-mating surface when the valve is
assembled. Body or bonnet gasket surface metal removal will
reduce the thickness of body or bonnet thickness by a maxi-
mum acceptable 0.030".
3. Inspect the bonnet bolting to ensure it is proper and bolting is
not damaged or stretched. If bolting is bad it shall be replaced.
Bolting is available from Flowserve distribution on short notice.
4. If the gasket surface is not damaged and/or has been refur-
bished per the above machining process, replace the gasket
with a gasket part number noted in the Recommended Spare
Parts List of Section 1. Gaskets are available from Flowserve
distribution on short notice.
5. Place the bonnet subassembly back on the valve and install the
bonnet bolting. Torque the bonnet bolting in accordance with
the torque requirements of Bonnet Torque Requirements of
Section 5.
6. Test the valve and, if acceptable, place back in service.
Valve Seat Leaker
1. Remove the bonnet subassembly. Inspect body, disc, and bon-
net bolting.
2. If the disc is badly damaged it can be replaced. Discs are avail-
able from Flowserve distribution on short notice.
3. Note any rust on the body and disc area. Internal rusting may
cause the valve to close improperly.
4. Clean rust from valve.
5. Inspect the valve body seat. If the seat has imperfections deeper
than 0.010", repair may not be economical and may be impos-
sible. A replacement body is readily available from Flowserve
distribution on short notice.
6. If the imperfections are less than 0.010", the valve seating
surfaces can be brought back into like-new seating condition by
lapping the disc to the body seat.
7. No special lapping tools are required. The bonnet subassembly
can be modified to serve as a lapping tool. (See Figure 6, Sec-
tion 5.) The packing shall be removed from the bonnet subas-
sembly and the yoke nut shall also be removed and/or modified.
8. The disc/disc nut arrangement shall be assembled with an
O-ring, or washer as noted in Figure 6, Section 5. This O-ring/
washer fixes the disc to the stem and causes it to rotate when
the stem is rotated.
9. The lapping process requires the disc to be rotated against the
body seat with a lapping compound between the two parts. The
rotation of the disc can be done manually or with a low speed
air tool. Rotation of the piston with an air tool should be on
the order of 40 rpm. Downward force should be limited to the
weight of the tool.
10. For the lapping process, two grades of lapping compounds shall
be used. The first lapping (rough) shall be done with the follow-
ing grade of compound:
Fel Pro
Clover Sharpening Compound
Silicon Carbide
Water Soluble Gel
120 grit Part No. 51846 E
Coarse
This compound removes a considerable amount of metal and
should take 3–5 minutes to refurbish the seating surfaces.
Discontinue when the disc and body have continuous lapping
lines on the seating surfaces.
The final lap shall be done with the following grade of
compound:
Clover Grade 1A
320 Grit
Very Fine
This polishes the seating surface of the disc/body seating
surface.