6 noise, 7 maintenance – Flowserve Vogt Forged Steel Gate User Manual
Page 28
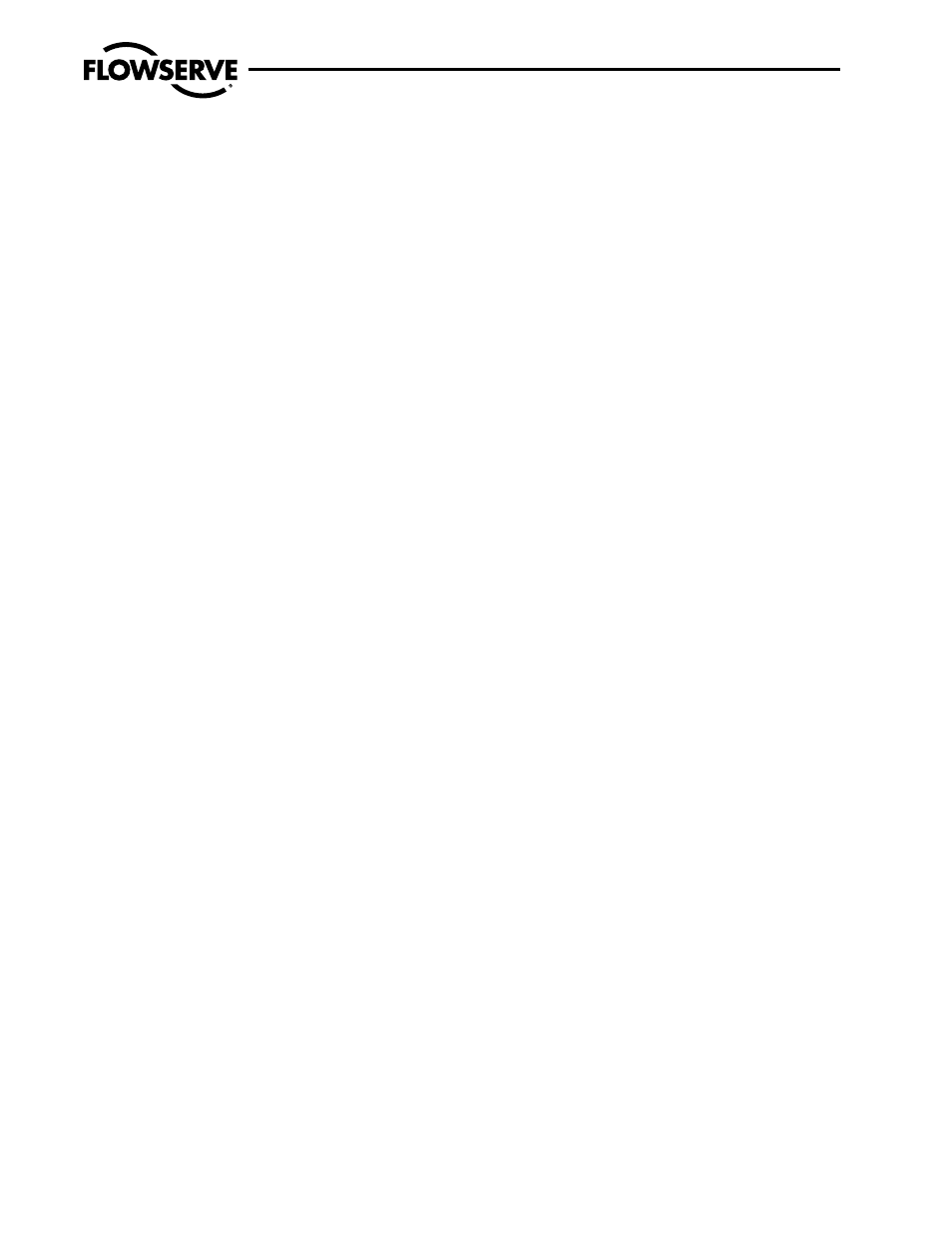
Flow Control
Vogt Valves
28
Forged Steel Gate, Globe and Check Valves
FCD VVENIM2000-02
but special features may be required for certain situations. Careful
systems analysis may be required in complex applications.
While a rapid closure of a check valve is normally the best method of
minimizing pressure surges due to flow reversal, some applications
produce flow reversals that are too rapid to prevent excessive reverse
velocity before the closure of a standard check valve could occur.
Such applications may require consideration of special valve
features such as:
a) A spring or method of other loading to provide more rapid
closing.
b) A dashpot or snubber to provide a slower, more controlled
closure in order to reduce reverse flow velocity by a throttling
action, as in a shutoff valve.
5.6 Noise
There are many different valve operating conditions that can result
in noise. Such noise may be “normal” considering the nature of
the fluid and the pressure, temperature and velocity of flow. There
may be a “wind” noise in a flowing gas line. There may be clear
or hoarse whistling sounds resulting from the shape of the flow
passage, including the flow path through a valve. Cavitating condi-
tions in a liquid line can cause a “white noise” that ranges from a
whisper to a sound like rocks and gravel, to a deafening roar. There
may also be mechanical noises as a result of movement of internal
“things” acted on by the flowing fluid. Some of these noises may be
relatively harmless insofar as system integrity and performance are
concerned. Mechanical damage in lines with compressible fluid is
generally limited to points of sonic or supersonic velocity, or where
a vortex resonance with an internal component causes movement
and wear or breakage.
Vortex resonance with an internal component may also cause
problems in liquid service. In addition, noise may be evidence of
cavitation, which has the potential for causing mechanical damage,
including massive erosion of the metal walls of a valve or pipe walls
and/or other internal components.
A full technical discussion of all sound-generating mechanisms is
beyond the scope of this document. Nevertheless, it is recommend-
ed that an evaluation be made of any condition of remarkable noise
in a piping system at least to the point of understanding its cause.
If a valve is involved, a determination should be made as to whether
the valve is the source or just happens to be the location of the
noise. Usually, if the valve is the source, the noise can be “tuned” by
slightly “throttling” the valve.
Mechanical or high-intensity fluid noise in the vicinity of a valve may
be a warning of potentially serious trouble. Expert assistance should
be obtained from system engineers or the valve manufacturer to
determine the cause and evaluate possible need for action.
Noise emitted from a closed valve is a special case that may indicate
seat leakage requiring repair. A whistling sound may indicate severe
erosion of seating surfaces while “gurgling” or “popping” sounds
may signify less severe leakage.
Consult Flowserve Vogt Valves when noise levels are desired for a
Vogt valve. Flowserve will need pressure, temperature, flow rate,
fluid details and pressure drop to determine the noise level.
5.7 Maintenance
Valves are properly considered to be a hybrid structure, a combina-
tion of a pressure vessel and operating machinery. Maintenance pro-
cedures therefore, must reflect the requirements of the occasional
opening or closing of the “machinery” and the predominant operat-
ing condition of the valve where pressure is continuously applied
and nothing is moving. The important performance parameters are
pressure boundary integrity, actuating effort required and internal
leak tightness. Maintenance should logically address the importance
of preserving these performance parameters.
Valves that remain in one position for long periods of time may be
hard to operate and/or not function as well as when originally in-
stalled. This reduction of operability can result from either a loss of
effective lubricants, aging of packing, surface corrosion of moving
parts, or an accumulation of deleterious solids. In some applications
it may be desirable to schedule periodic partial or full cycle exercis-
ing of such valves.
Check valves require special consideration because they normally
have no external stems, actuators, or packings that might indicate
a pending operational problem. Complete internal failure may occur
due to wear with no obvious advance warning. Preventive main-
tenance is recommended particularly where sudden check valve
failure may require expensive plant or system shutdown.
Noise or vibration emitted at or near a closed check valve may be an
indicator of leakage. Distinctive noises may also be produced from
internal motion of the parts of check valves that are not fully open
during forward flowing conditions. “Thumping” or “tapping” may
indicate that the disc is impacting either on the seat or the full-open
stop, or simply “rattling” in its guides. These types of conditions
can lead to rapid wear and failure of the valve. Special non-intrusive
diagnostics systems can be used to augment the evaluation of the
noise. Periodic disassembly and internal inspection of selected