4 fluid dynamics of shutoff valve operation, 5 check valves – Flowserve Vogt Forged Steel Gate User Manual
Page 27
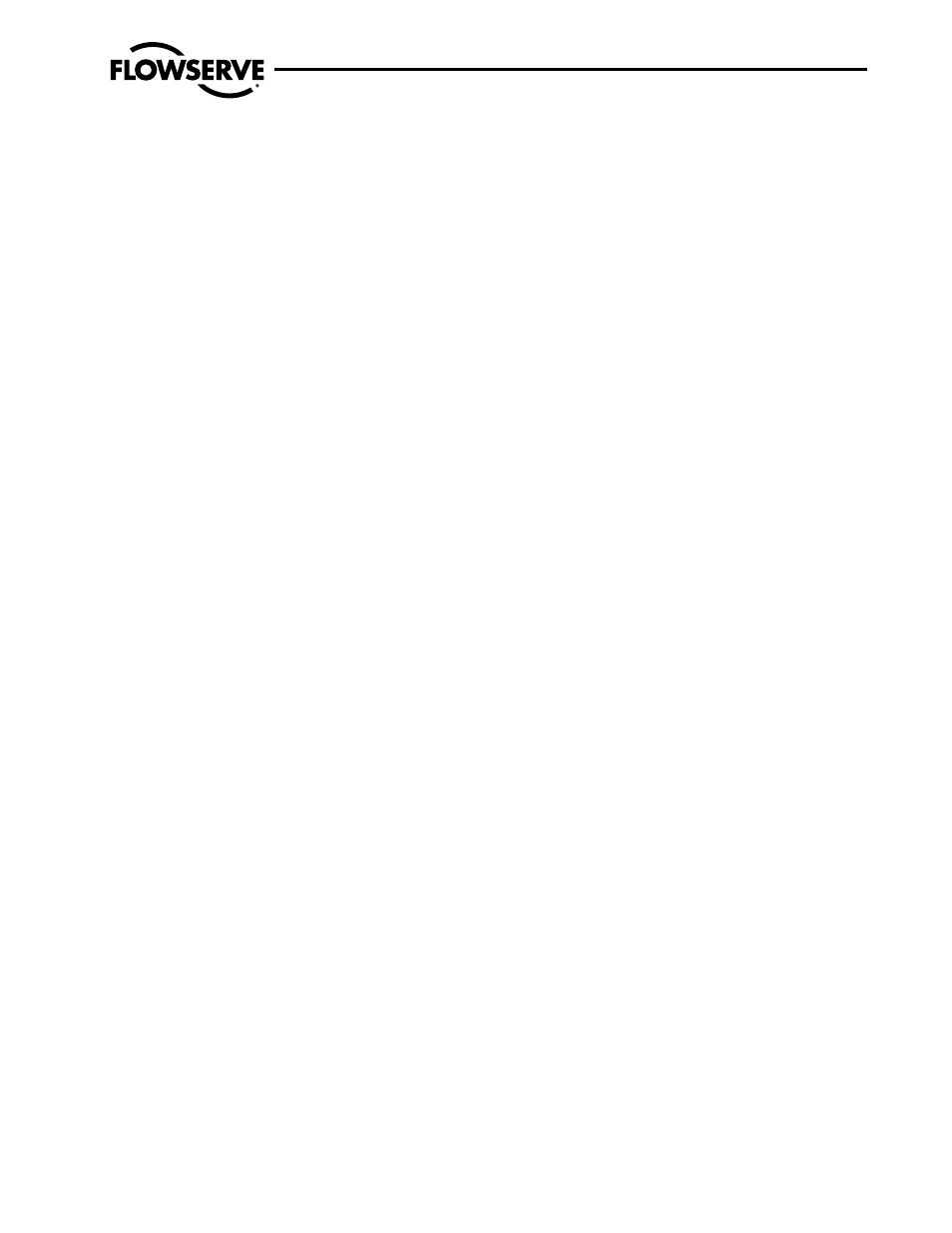
Flow Control
Vogt Valves
FCD VVENIM2000-02
Forged Steel Gate, Globe and Check Valves
27
d) Pneumatic pressure available for pneumatic actuators (cylinders
or diaphragms). Also, specify fail-open, fail-closed, fail-as-is, or
any special requirements.
e) Requirements for position indication signals.
Actuator selection and adjustments should normally be made by
Flowserve based on published literature and/or technical advice
of actuator manufacturer. Flowserve should be consulted when a
manually operated valve must be retrofitted with a power actuator.
a
CAUTION: Some valve actuators, when sized to provide
specified loading, may have much higher output at maxi-
mum switch or control settings and therefore be capable of
damaging valves if misadjusted. Valve and actuator manu-
facturer instructions should be followed closely to prevent
overloading valve stems, backseats and other structural
parts. Successful operation of power-operated valves re-
quires a diligent coordination of the skills and efforts of the
valve specifier, Flowserve and the actuator manufacturer.
Most applications are problem-free, but miscommunication
can lead to unreliable operation at one extreme and possible
valve or actuator damage at the other extreme.
5.4 Fluid Dynamics
of Shutoff Valve Operation
A flowing fluid in a piping system has mass and velocity. Anything
that causes a moving mass to change its velocity will experience a
reacting inertia force in proportion to the magnitude of the mass and
the rate of the imposed velocity change.
However, in the flow of gases the reacting inertia forces are inher-
ently moderated by the compressibility of the fluid that permits the
instantaneous velocity change to be effectively limited to the mass
of fluid in the immediate vicinity. This, in addition to the self-cush-
ioning capacity of the fluid column in the upstream pipe, effectively
precludes any significant problem of pressure surge in rapidly
closed valves in gaseous fluid piping.
In contrast, the inertia of the fluid column in a liquid pipeline is not
so easily overcome. Its relative incompressibility provides no such
cushion or proximity-limiting mechanism. The entire upstream fluid
mass is required to be decelerated at once by the closing valve,
and the resulting pressure surge may be of sufficient magnitude to
cause structural damage.
An additional potential problem can occur downstream from the
closing valve. This may be described as fluid column rupture and
involves the inertia of the fluid column carrying it away from the
closed valve with the proximate space being occupied by a bubble of
the fluid vapor or, simply, a substantial vacuum. If there is sufficient
backpressure in the line, the fluid column will reverse its velocity
and close the void created by the fluid column rupture and cause
another pressure surge when it reaches the valve.
It should be recognized that pressure surge intensity is roughly
proportional to the length and velocity of the fluid column upstream
of the closing valve and inversely proportional to the time taken to
close the valve. Fluid column rupture and return surge intensity is
proportional to the same condition on the other side of the valve in
addition to the back pressure in that section of piping. Therefore,
a slow closing is helpful in limiting the magnitude of the pressure
surge phenomena.
In large, long distance liquid pipelines it is critically important to
evaluate pressure surge possibilities and to establish limits on the
speed of closure of the flow shutoff valves. In operating such valves
or setting the speed of operation of power-actuated valves, design
limits on speed of closure should be conscientiously observed.
Rapid closure of a valve in any flowing liquid pipeline can cause a
substantial pressure surge that may manifest itself in a sharp “bang”
or possibly a series of “bangs.” This is frequently referred to as
water hammer. This phenomenon can occur in any flowing liquid
line and is not limited to waterlines. Rapid closing of a shutoff valve
in a flowing liquid line should be avoided especially during the last
part of the stem travel.
5.5 Check Valves
Check valves are one-way valves that function to automatically stop
a flow reversal in a flowing line. In most applications, the fastest
possible closure is desirable. The speed of closure is understood in
terms of the shortest possible time to achieve closure following the
instant of flow reversal. It follows then, that the shorter that time
interval can be made, the lower the velocity of the reverse flowing
liquid will be.
The pressure surge resulting from a check valve closure is likely
to be more severe than that in the case of the shutoff valve as the
shutoff valve will usually provide a throttling action, while the check
valve closure may be virtually instantaneous with little preliminary
throttling.
A check valve closure can also cause downstream fluid column
rupture just as in the case of shutoff valves. Furthermore, on
fluid column reassembly, the pressure surge may be of sufficient
magnitude to reopen the check valve, starting another sequence of
closure, surge, etc. Under certain conditions a protracted succes-
sion of closure “hammers” may result.
The kinetic energy in flowing fluids present special problems regard-
ing check valve performance. Quick closing is normally desirable,