8 valve maintenance, Notice, Warning – Flowserve Vogt Forged Steel Gate User Manual
Page 29
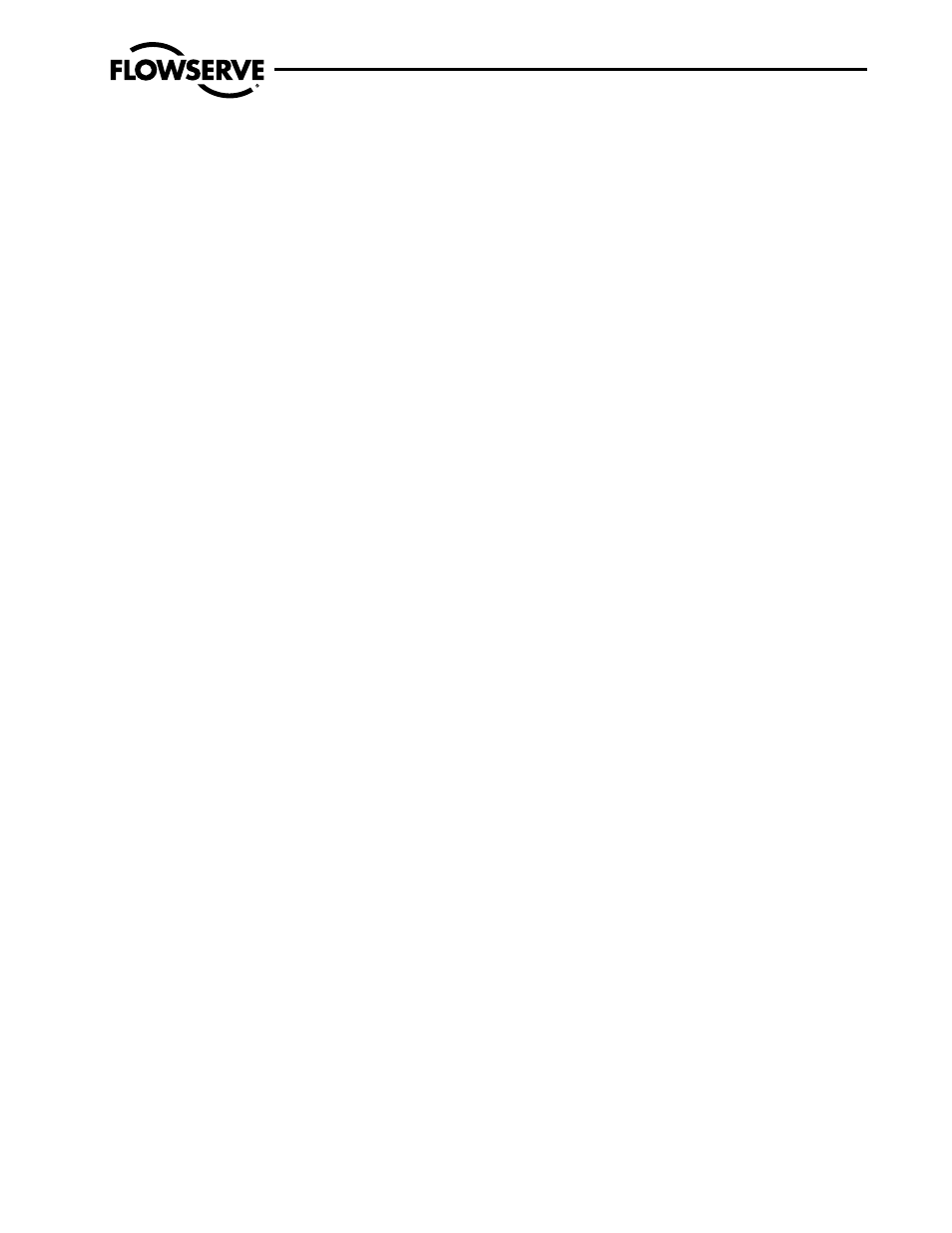
Flow Control
Vogt Valves
FCD VVENIM2000-02
Forged Steel Gate, Globe and Check Valves
29
valves may be advisable, particularly where they are located close to
upstream flow disturbances.
Stem seals may be a source of problems, particularly in valves that
are frequently cycled or must operate at high pressures or tempera-
tures. The stem seal must prevent or minimize leakage of line fluid
between a movable stem and a stationary bonnet. While special
mechanical arrangements, elastomers, or proprietary seals are used
in some cases, the normal arrangement includes a cylindrical cham-
ber in the bonnet surrounding the stem, with compression packing
materials retained in the chamber by a gland and associated bolting.
Conventional compression packing requires that the gland bolting
provide sufficient load to eliminate any communication porosity in
the packing material and to compress it into intimate contact with
the stem and bonnet. Clearances between the associated parts must
be close enough to contain the packing material and minimize extru-
sion. Maintenance practices that increase clearances (e.g., machin-
ing of glands and/or bonnets to remove corrosion), may result in
packing extrusion and leakage or “blowout”.
Pressure boundary integrity requires basically sound pressure-
containing parts, a pressure-tight static seal at assembly joints and
in most cases, an effective working seal between a moving stem
and the valve body. Maintenance of pressure boundary parts and
the static seal of assembly joints are not usually considered to be
a problem. However, continuous monitoring is recommended to
confirm that problems do not occur. The need for paint protection
against corrosion of exposed piping should be obvious from normal
observations of the system.
Wear and loss of packing material are normal expectations in
frequently cycled valves. However, current packing materials and
systems will minimize this deterioration particularly in new and
well-maintained valves. Packing gland adjustment may be necessary
from time to time but routine “repacking” should not be required in
most valves that are otherwise well maintained. Packing replace-
ment can usually be deferred until a time when other valve main-
tenance is required as long as the packing gland shows adequate
room for further adjustment. The repacking of a backseated valve
under pressure is not recommended.
Valve manufacturers and packing manufacturers should be con-
sulted regarding the best design features and compression packing
materials available to solve chronic packing problems. Ongoing
developments in valve design and packing technology may offer
improvements that can be implemented by retrofitting a valve
with improved design, materials and installation procedures. For
example, spacers may be used in the deep packing chambers com-
mon in old valves designed for use with old-style asbestos packings
so that new packings/materials may be effectively installed.
Severe throttling service may cause the valve to be subjected to
damage of the seating surfaces and other parts. Severe cavita-
tion can cause gross damage of the internal parts, including the
valve body and downstream piping. Good preventive maintenance
procedures including periodic inspections may prevent serious
failures that require expensive shutdowns. Methods of evaluation
and solutions for maintenance problems are beyond the scope of
this document. Flowserve should be consulted concerning design
features and operating procedures for valves.
External valve mechanisms, actuators and accessories are gener-
ally readily accessible for inspection and maintenance. Reasonable
protection should be provided to prevent mechanical damage and
potentially degrading environmental exposure to such things as
airborne grit, chemicals or moisture. Working surfaces such as
stem threads, bearings, and gears should be lubricated on a reason-
able schedule using the lubricants recommended or approved by the
valve or actuator manufacturers.
Maintenance of valves must involve a good preventive maintenance
program, particularly for check valves and valves in servere throt-
tling service. Stem sealing problems may be alleviated by use of the
newest technology in valve design, packing materials and installa-
tion procedures.
5.8 Valve Maintenance
Notice
This manual is intended as a maintenance guide for Flowserve Vogt
Valves. Before working on any Vogt valves or related products,
the reader should review and fully comply with this manual and its
warnings and with the reader’s company safety procedures.
If anything in this manual is unclear, contact the Flowserve Cus-
tomer Service Department for assistance.
Flowserve and its employees are in no way responsible for dam-
age to property or for personal injury or death which may result
through the use or misuse of any Vogt product, publication, audio
or visual aid.
Warning
Vogt valves described in this manual may have been manufactured
prior to September 1, 1986 and may have been equipped with
gaskets that contained asbestos. When servicing, disassembling,
or disposing of these products, avoid breathing the asbestos fibers
or dust. Dispose of the material in accordance with local, state, and
federal law.