21 check valve maintenance – Flowserve Vogt Forged Steel Gate User Manual
Page 40
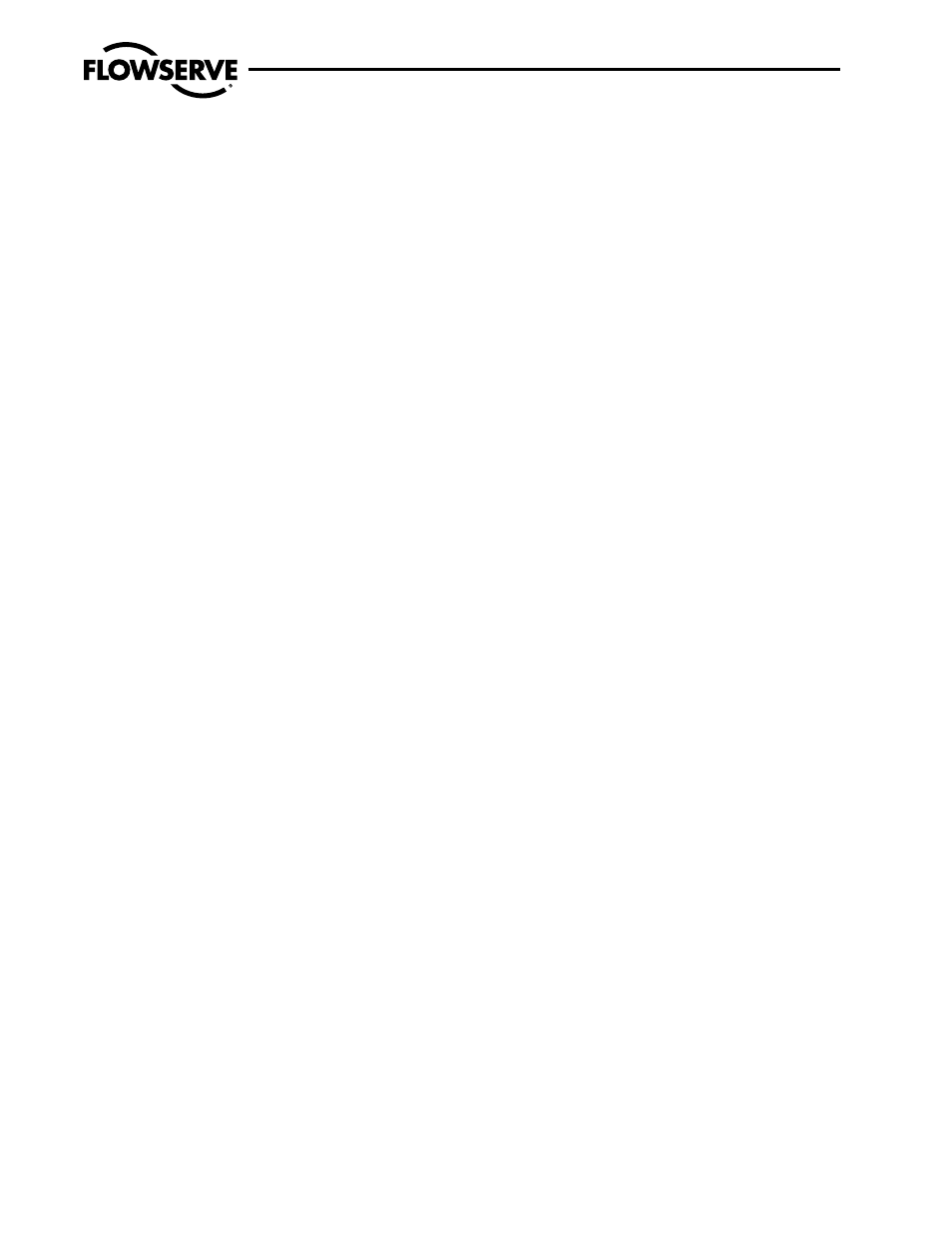
Flow Control
Vogt Valves
40
Forged Steel Gate, Globe and Check Valves
FCD VVENIM2000-02
The final lap should be 3–5 minutes depending on the appear-
ance of the lapping line on the piston. Since Vogt globe valves
have a line contact, a continuous lapped line of width 0.040–
0.050" is normal. The lapped body shall have a similar continu-
ous line. The disc and body that have been lapped to each other
shall be assembled together.
A normal appearance of a properly lapped valve would be as
follows:
The disc would have a continuous black line when it is
cleaned of the lapping compound. The lapping compound
above is a water-soluble and can be cleaned with water. The
black line represents the lapped surface.
The body should have a similar continuous black line as
well of similar width. The lapping compound can be cleaned
with water.
Once the body and disc have a continuous lapped line of con-
tact, the O-ring shall be removed from the stem/disc/disc nut
arrangement. The stem/disc/disc nut shall be reassembled. The
disc/disc nut shall be staked per Figure 13, Section 5. This locks
the disc nut to the disc. Once this is complete the valve can be
reassembled, tested, and placed back in service.
Seal Welded Bonnet Globe Valves
The valves in this category include valves with threaded bonnets
that, once assembled, are seal welded. They contain no gaskets.
Valve replacement may be more economical than repair for these
valves.
Bonnet Gasket Leaker
This would be a very unusual event, but if a seal weld leaks, it
should be ground out while the valve is not under pressure, and a
weld repair at the point of leakage shall be performed. See Section
4 for typical weld metal that can be used to weld repair carbon, alloy
and stainless steel valves.
Valve Seat Leaker
1. Remove the seal weld by grinding and/or machining. This will
require removal of the weld metal which will be 1/4" thick at a
minimum.
2. Once the seal weld is totally removed, use a pipe or strap
wrench to remove the bonnet.
3. The lapping of the disc to body seat shall be per the previous
procedure.
4. Reassemble the bonnet to the valve.
5. Test the valve. If acceptable, proceed with replacing the seal
weld.
6. Test the valve for seal weld integrity and, if acceptable, place
valve back in service.
7. Persistent leakage may be the result of “cracked hard facing”
on the valve body seat. If so, the body and/or valve have to be
replaced. Cracked hard facing cannot be repaired.
5.21 Check Valve Maintenance
Bolted Bonnet Piston Lift Check Valves
The repair of Vogt valves with spiral-wound gasket bonnet joints can
be accomplished as follows:
Recommended Spare Parts
1. Bonnet gasket—See Section 1 for part number. Listed gaskets
are available from Flowserve distribution on short notice.
a
CAUTION
1. The system pressure shall be totally isolated and
vented from the valve to ensure the valve is at zero
pressure while being repaired.
2. For small valves, replacement may be more eco-
nomical than repair.
Bonnet Gasket Leaker
1. Remove bonnet subassembly. Four or eight bonnet bolts must
be removed to remove the bonnet subassembly.
2. Clean and inspect gasket recess and gasket surface on the
bonnet. Erosion in the gasket seating area greater than 0.030"
deep will require the valve body and/or bonnet to be replaced. A
machining allowance of 0.030" is allowed to refurbish the gasket
seating area of the bonnet and/or body.
a
CAUTION: Ensure that any metal removed from the
depth of the body gasket recess is duplicated by remov-
ing the same amount from the top of the body. This is
required to ensure that the depth of the gasket recess
(0.095–0.100") in the body is maintained.
The bonnet gasket surface depth can be machined by up to
0.030" without damage to the valve. Bonnet gasket surface
removal shall be across the full surface of the bonnet that
contacts the gasket and body-mating surface when the valve is
assembled. Body or bonnet gasket surface metal removal will
reduce the thickness of body or bonnet thickness by a maxi-
mum acceptable 0.030".
3. Inspect the bonnet bolting to ensure it is proper and bolting is
not damaged or stretched. If bolting is bad it shall be replaced.
Bolting is available from Flowserve distribution on short notice.