3 operation – power actuated valves – Flowserve Vogt Forged Steel Gate User Manual
Page 26
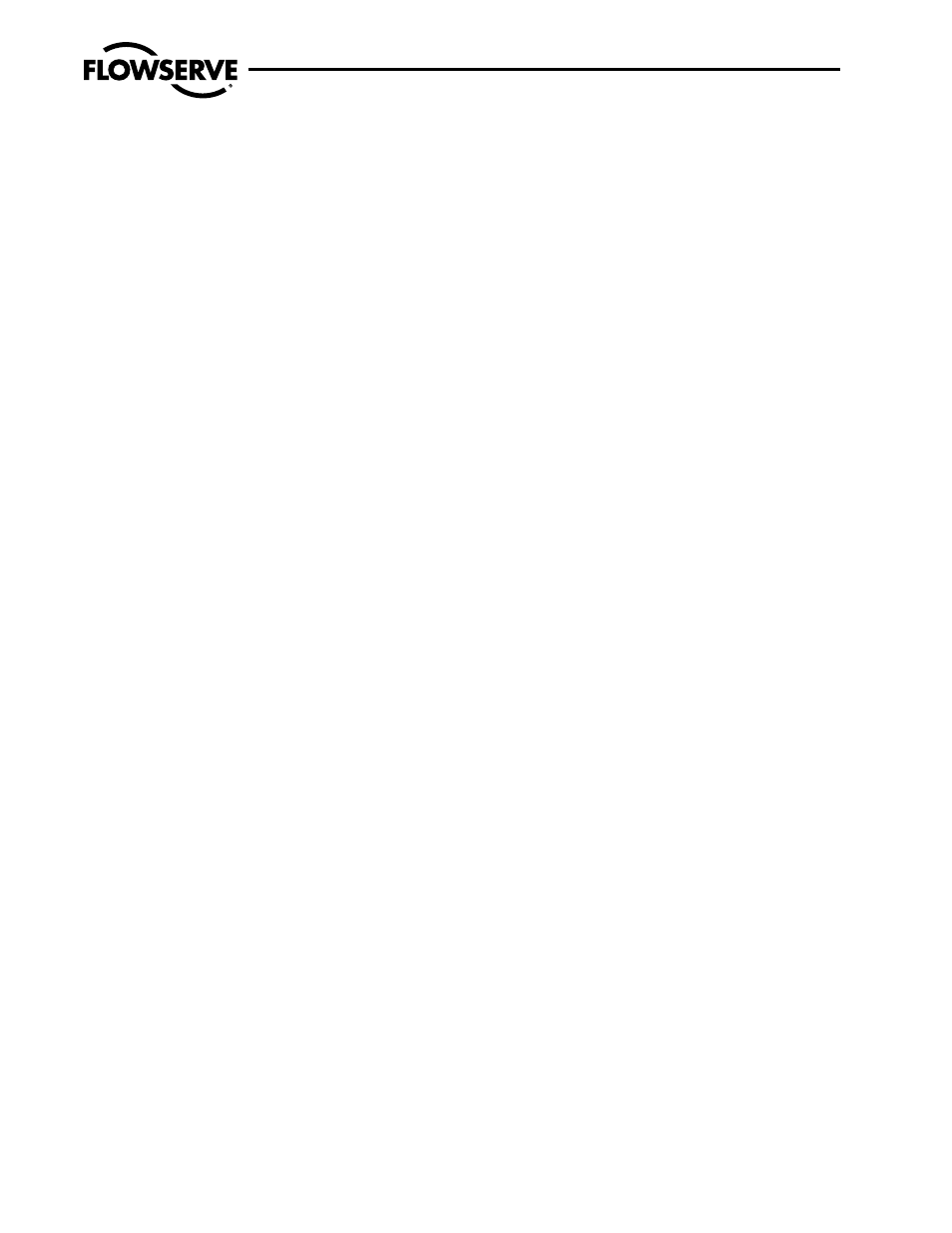
Flow Control
Vogt Valves
26
Forged Steel Gate, Globe and Check Valves
FCD VVENIM2000-02
Globe valves (straight, angle or Y-pattern) and stop check valves
with pressure under the disc, require sufficient stem loading to
balance the line pressure and provide adequate net seat load. The
higher the line pressure, the higher the required stem loading to
achieve a leak-tight seal. Follow the manufacturer’s recommenda-
tions on torque or handwheel rim force for seating of manually
operated valves as well as impacting of impactor-type handles or
handwheels.
a
CAUTION: The use of valve wrenches on handwheels may
lead to valve damage or injury to operators.
Most valves in which the internal closure elements slide across the
seat as in ball, plug, non-wedging gates, butterfly etc., do not rely on
stem actuating force to provide tight shutoff. However, the correct
position of the closure element in these types of valves is very im-
portant. In some cases, the effort required to move the closure ele-
ment may increase substantially during final approach to the closed
position, giving a false impression of having reached the required
position. Failure to reach and stop at the full-closed position can
result in leakage and consequent damage to the seal elements.
Thermal expansion and contraction can cause solid wedge gate
valves to “lock up” if closed while hot. As the relatively cooler stem
heats up to body temperature, and/or the body cools down toward
the stem temperature, the stem expansion and/or body contraction
will cause stem thrust to increase. If the thrust increases sufficiently,
the wedge may be “locked” between the tapered seats.
Vogt valve stems are provided with a backseat arrangement, that
is, a shoulder on the stem or on another part of the stem-disc as-
sembly, that engages a corresponding seat shoulder on the inner
side of the bonnet.
It has become generally recognized that the use of the stem back-
seat for stem sealing may mask an unsatisfactory condition of the
stem packing. For this reason, the use of the backseat for normal
operational stem sealing is not recommended. It is recommended
that the valve be opened against the backseat as a means of deter-
mining that the full-open position has been reached, and the stem
should then be backed off slightly from the backseat.
If circumstances necessitate use of the backseat for stem sealing to
permit system operation until a shutdown will allow replacement of
the stem packing, it should be recognized that backseats are usually
much smaller than “mainseats” and care should be exercised to
avoid applying excessive stem force in back seating. Impactors,
gears, or similar features provided to assist in main seating valves
should not be used for backseating.
a
CAUTION: Some users consider that backseats are provided
for the purpose of repacking valves, which are under
pressure. When the packing is removed in this situation,
any leakage past the backseat escapes directly to the
atmosphere and constitutes a potential safety hazard to
personnel. The practice of repacking under pressure is
not recommended. Further, if a valve is operated in the
backseated position for any reason, exercise caution when
moving the stem away from the backseat as the packing
may have deteriorated while isolated from the line fluid and
then leak when exposed to pressure.
Purchase specifications requiring restrictive maximum forces to
be applied on levers or handwheel rims may also lead to damag-
ing forces being applied to valves or actuators in actual practice
as larger forces are sometimes applied in the field. Users should
consider this fact in training of operating personnel.
5.3 Operation –
Power Actuated Valves
Functionally, closure performance characteristics and backseat-
ing considerations are associated with all valve types regardless
of the means of operation. Satisfactory valve performance with
power actuation requires appropriate programming of the various
requirements and constraints into the actuator controls. Therefore,
the actuator should be adjusted to deliver an adequate opening,
running and closing force to suit the anticipated service conditions.
For the position-sensitive valve types, the close control should be
position controlled by external stops or limit switches. Be sure to
contact the actuator manufacturer’s operation manual for more
detailed information.
Data required for selection and adjustment of power actuators
should be delineated clearly in purchase specifications for actuated
valves. This data shall include but not necessarily be limited to:
a) Upstream pressure and differential pressure conditions at which
both opening and closing shall be required. Specify direction
if applicable. Additionally, specify if valve operation is required
under high-flow “blow down” conditions.
b) Speed of operation required or the maximum time for opening
and/or closing. Also, specify a minimum time if required due to
fluid dynamics.
c) Electrical power supply available (AC or DC voltage, phase,
frequency) for electrical power actuators or controls. Operating
conditions for reduced voltages should also be considered.