Flowserve 3400IQ User Manual
Page 15
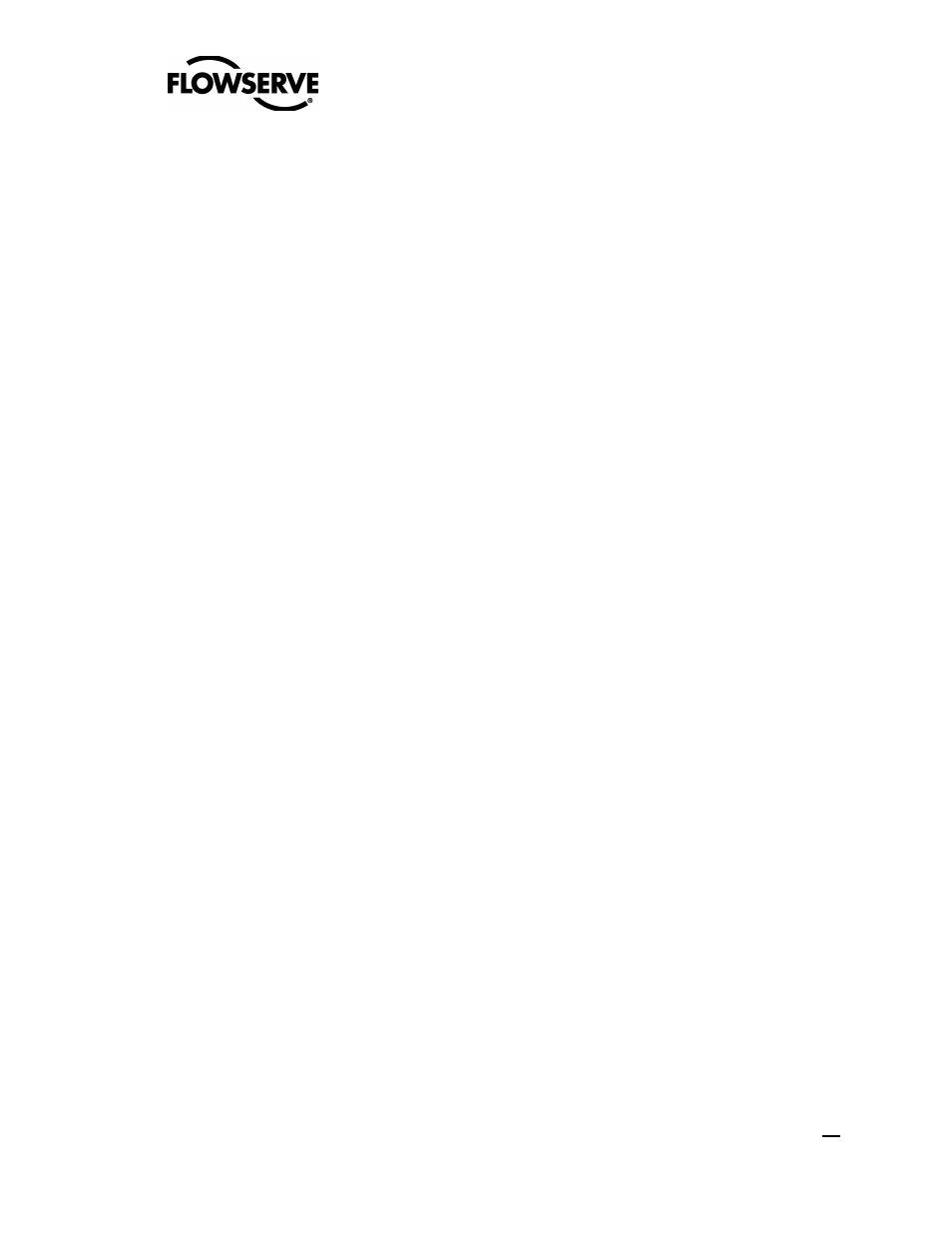
Logix 3400IQ Digital Positioner FCD LGENIM3403-00 – 11/07
•
Actuator Style: Check this box only if the positioner is mounted on a rotary type actuator.
•
Custom Characterization Active: Check this box if the user wishes to have the FINAL_VALUE parameter
characterized. If the Quick Opening or Equal Percent box is also checked the positioner will use a factory
defined curve. If only Custom Characterization Active is checked a user-defined curve will be used. Note
that when this box is checked the curve can not be changed. If the user wishes to use a different curve, or
edit the custom curve, the user must first uncheck this box.
•
Air Action: Check this box only if the actuator is tubed to be ATC (Air-To-Close). After configuring
CONTROL_FLAGS, remember to click the Write button to apply the values.
GAIN_UPPER: The Logix 3400IQ digital positioner uses a special gain algorithm. The proportional gain
increases with a decrease in error. This allows for maximum resolution and speed. GAIN_UPPER is the
upper limit to proportional gain.
GAIN_LOWER: The Logix 3400IQ digital positioner uses a special gain algorithm. The proportional gain
increases with a decrease in error. This allows for maximum resolution and speed. GAIN_LOWER is the
lower limit to proportional gain.
GAIN_MULT: The Logix 3400IQ digital positioner uses a special gain algorithm. The proportional gain
increases with a decrease in error. This allows for maximum resolution and speed. GAIN_MULT adjust the
transition rate between GAIN_UPPER and GAIN_LOWER.
IGAIN: In addition to proportional gain the Logix 3400IQ digital positioner uses integral as well. IGAIN is the
integral gain setting. Typically this is set to 10.
IL_OFFSET: This parameter tells the positioner where the spool valves ‘null’ position is. This value is set
during a stroke calibration procedure, and typically requires no further adjustments.
CMD_USED: This is the set point or command to which the positioner is controlling. After FINAL_VALUE is
acted on by Characterization, Softstops and FINAL_VALUE_CUTOFF, CMD_USED reports the modified or
used command value.
CALIBRATE: This parameter initiates Calibration. Three types of calibration are available: stroke, pressure
sensors (advanced models only) and stroke time test. Stroke time test will measure the stoke speed of the
actuator from a 1 percent to 99 percent position, and from 99 percent to 1 percent. To learn more about
calibration refer, to the Calibration section of this document.
PRESS_CAL: Before doing a pressure sensor calibration, enter the supply pressure being used (in units
expressed by PRESS_UNITS).
SOFTSTOP_HIGH: Software-imposed stroke limit. The positioner will not allow the valve to open beyond
the value shown in this parameter.
SOFTSTOP_LOW: Software-imposed stroke limit. The positioner will not allow the valve to close beyond
the value shown in this parameter.
CYCLE_COUNTER: This parameter counts the number of cycles that have occurred.
CYCLE_DEADBAND: In order for a cycle to be counted, it must be greater than the value in this field.
CYCLE_LIMIT: If CYCLE_COUNTER exceeds this value, the yellow LED will start to blink and a warning
generate in TRAVEL_FLAGS.
TRAVEL_ENG: Total distance the valve traveled.
TRAVEL_DEADBAND: Amount in percent of stroke the valve must move for the movement to be added to
TRAVEL_ENG.
TRAVEL_ALERT: If TRAVEL_ENG exceeds this value, the yellow LED will start to blink and a warning
generated in TRAVEL_FLAGS.
15
flowserve.com