Fieldbus basics – Flowserve 3400IQ User Manual
Page 3
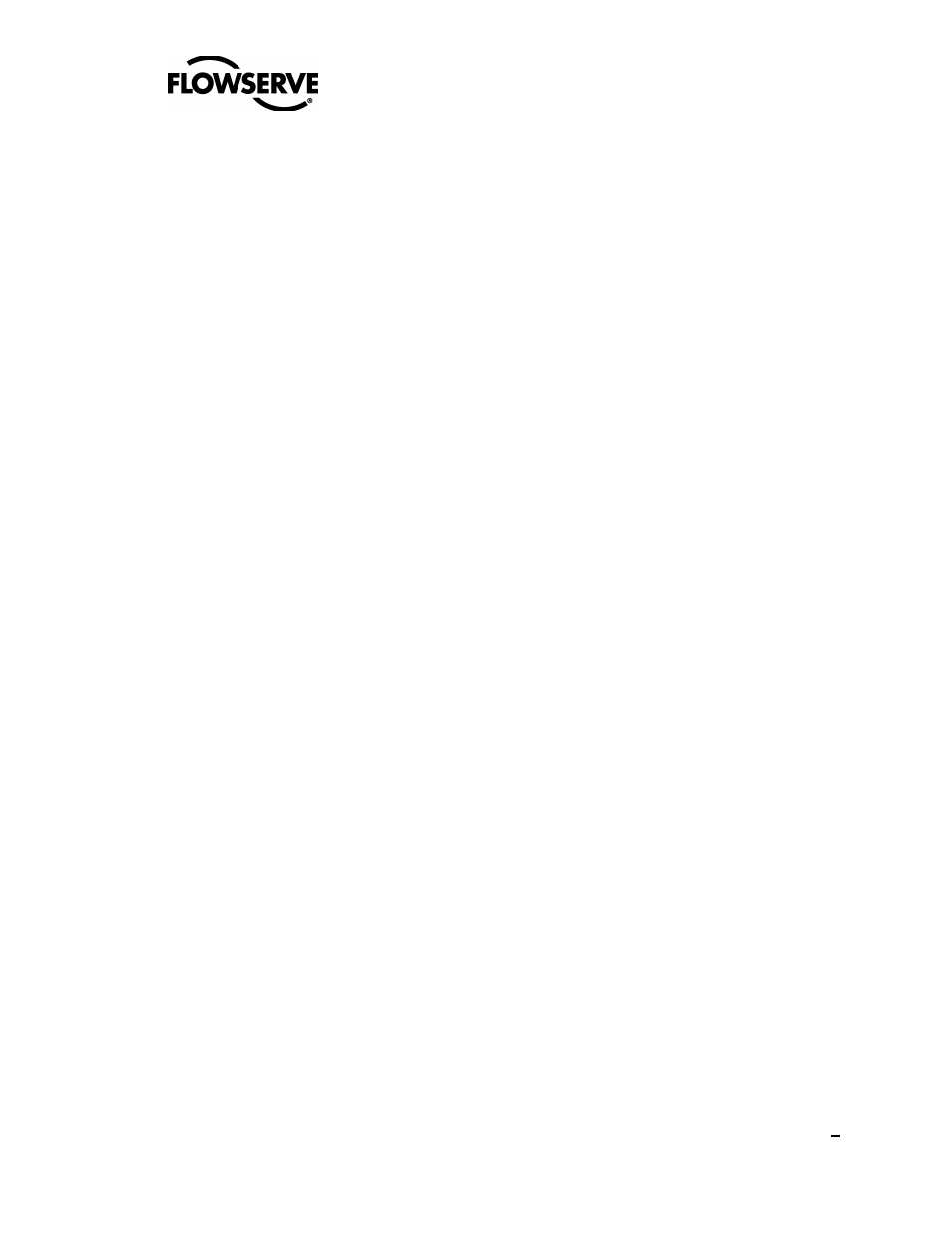
Logix 3400IQ Digital Positioner FCD LGENIM3403-00 – 11/07
F
OUNDATION
fieldbus Basics
The F
OUNDATION
fieldbus protocol is an all-digital, two-wire method of interconnecting field devices. A
traditional 4-20 mA analog loop calibrator cannot be used with a Logix 3400IQ digital positioner. The
positioner always receives its command signal from a digital source. In essence, when configured, a FF loop
becomes a local area network (LAN) and the positioner receives its command over the network.
Because the Logix 3400IQ digital positioner is a two-wire device, existing wiring from a 4-20 mA application
can be used. FF devices require 9-32 VDC power supply, and FF power supply conditioner. (Just because
the same wire can be used, it does not mean the device is powered similar to other 4-20 mA devices.)
The different functions within an FF device are found in virtual function blocks. For example, if a device is
capable of performing PID control, the device will have a PID function block. In an FF network any function
block in one device can have a virtual connection to the function block of another device. This makes it
possible to have any vendor’s transmitter PID function block connected to a Logix 3400IQ digital positioner
analog out function block, thus controlling the valve. Any combination of these virtual function blocks is
possible, regardless of who manufactures the devices. The NI Configurator allows for easy graphical
connection, or ‘wiring’ of the function blocks.
The Logix 3400IQ digital positioner contains four function blocks;
1. Resource block (RB). The RB contains basic FF information.
2. PID control block. This block is capable of performing PID control of a process. Honeywell designed the
Logix 3400IQ digital positioner’s PID. Honeywell should be consulted for assistance in tuning this block.
3. Analog Out (AO). This function sends the command signal to the transducer block. It can receive the
signal from another function block, or be written to directly from the Configurator.
4. Transducer block (FVPTB). This block converts the command signal (FINAL_VALUE) to valve position.
Positioner configuration, calibration and diagnostics are handled in this block. The user should read all
documentation that comes with any FF device. FF documentation can be obtained from the Fieldbus
Foundation. The final section of this document provides FF contact information.
To allow for product differentiation, the FF specification permits manufacturers to add custom features to an
FF device. For the host systems to take advantage of these custom features the manufacturer supplies a
Device Description (DD). The DDs must be installed correctly for the Configurator to take full advantage of a
device’s functionality. A later section details proper DD installation when using the NI Configurator.
3
flowserve.com