Mounting and installation, Air supply requirements, Electrical wiring – Flowserve Logix 1200e LGAIM0044 User Manual
Page 31: Frequently asked questions
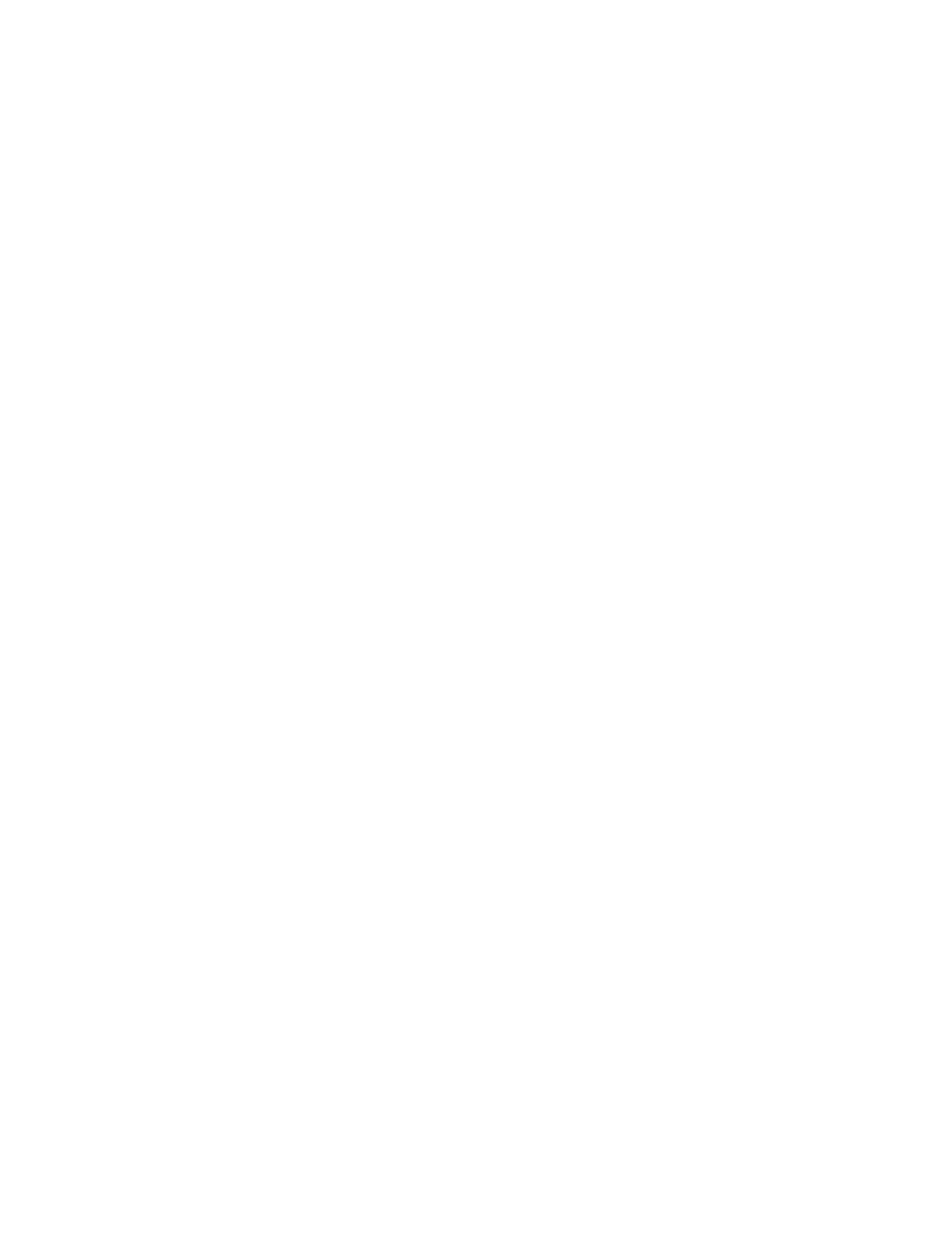
Flowserve Corporation, Valtek Control Products, Tel. USA 801 489 8611
44-31
spool position. At that point, the actuator pressures
change and the stem begins to move. The stem move-
ment reduces the deviation between Control Com-
mand and Stem Position. This process continues until
the deviation goes to zero. The control algorithm is
both proportional and integral. (This algorithm will be
further explained later in this guide.)
The following detailed example explains the control
function:
Given:
Unit is in Analog command source
Custom characterization is disabled
(therefore characterization is Linear)
Soft limits and MPC are disabled
Valve has zero deviation with a present input
signal of 12 mA
Loop calibration: 4 mA = 0% command, 20
mA = 100% command
Actuator is tubed ATO (Air-to-Open)
Given these conditions, 12 mA represents a Com-
mand Source of 50 percent. Custom characterization
is disabled, so the Command Source is passed 1:1 to
the Control Command. Since zero deviation exists, the
Stem Position is also at 50 percent. With the stem at
the desired position, the spool valve will be positioned
so that no airflow is allowed to either side of the actua-
tor. This is commonly called the null or balanced spool
position.
At this point, change the input signal from 12 mA to 16
mA. The positioner sees this as a Command Source
of 75 percent. With Linear characterization, the Con-
trol Command becomes 75 percent. Deviation is the
difference between Control Command and Stem Posi-
tion, i.e. Deviation = 75% - 50%= +25%, where 50 per-
cent is the present stem position. With a positive
deviation, the control algorithm sends a signal to move
the spool up from its present position. As the spool
moves up, the supply air is applied to the bottom of the
actuator and air is exhausted from the top of the actu-
ator. This new pressure differential causes the stem to
start moving towards the desired position of 75 per-
cent. As the stem moves, the Deviation begins to
decrease. The control algorithm begins to reduce the
spool opening. This process continues until the Devia-
tion goes to zero. At this point, the spool will return to
its null or balanced position. Stem movement stops
and the desired stem position is now achieved.
One important parameter is now introduced – the
inner loop offset. Referring to Figure 18, a number
designated as the Inner Loop Offset is added to the
output of the control algorithm. For the spool to remain
in its null or balanced position, the control algorithm
must output a non-zero spool command. This is the
purpose of the inner loop offset. The value of this num-
ber is equivalent to the signal that must be sent to the
spool position control to bring it to a null position with
zero deviation. This parameter is important for proper
control and will be discussed further in the Control and
Tuning section.
Mounting and Installation
Air Supply Requirements
NOTE: The Logix 1200 positioner requires an external
air filter (preferably the Valtek coalescing air filter).
The air supply must conform to ISA Standard S7.3 (a
dew point at least 18° F/10° C below ambient tempera-
ture, particle size below 5-microns and oil content not
to exceed one part per million); however, filtering for 1-
micron particle size is recommended. For a model with
advanced diagnostics (Logix 121X), the internal pres-
sure sensors are rated for continuous operation up to
150 psig (10.3 barg).
Electrical Wiring
First, verify the polarity when making the field termina-
tion connection. The Logix 1200 positioner is reverse
polarity protected. With a 4-20 mA source connected,
verify that the positioner’s LED is blinking to determine
if the electronics are running. Only one LED will blink
at any given time. Remember the 4-20 mA input cur-
rent signal must be greater than 3.5 mA to power-up
the Logix 1200 positioner. Never connect a voltage
source directly across the Logix 1200 terminals. The
current must always be limited for 4-20 mA operation.
NOTE: The Logix 1200 positioners carries an intrinsi-
cally safe barrier rating of 125 mA. Currents up to 125
mA will not damage the device.
Frequently Asked Questions
Q: My DCS uses 24 VDC. Can I run a Logix 1200
positioner?
A: A DCS output current card does run from 24 VDC
but the card regulates the actual current output. How-
ever, if the 24 VDC were applied directly across the
terminals, nothing would limit the current and the
Logix 1200 field termination board could be damaged.
The important point to remember is that it does not
matter what the current source voltage supply is as
long as the current is limited in the 4-20 mA range.