Air action, Linear vs. rotary, Frequently asked questions – Flowserve Logix 1200e LGAIM0044 User Manual
Page 32
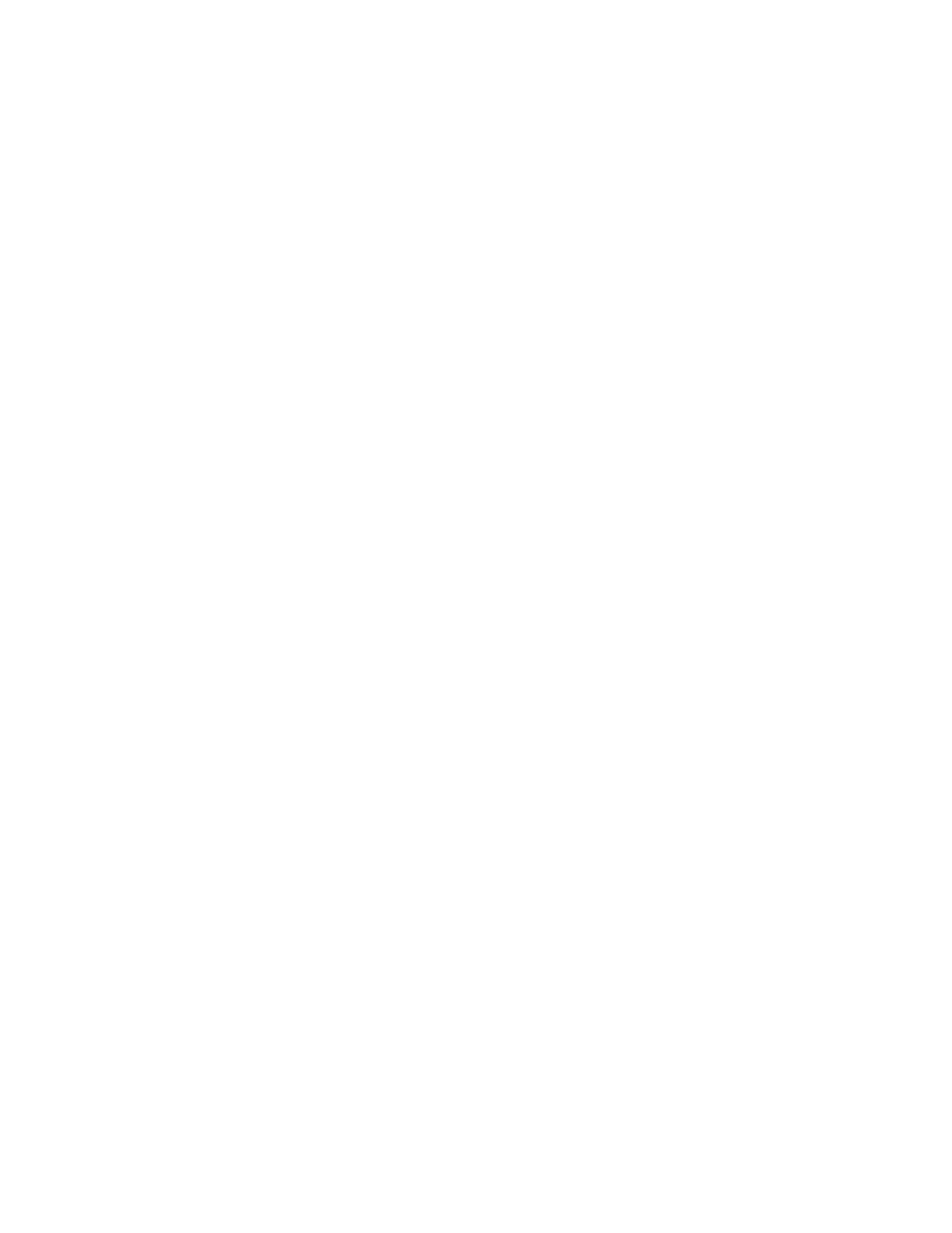
44-32
Flowserve Corporation, Valtek Control Products, Tel. USA 801 489 8611
Q: I accidentally placed a voltage supply across the
Logix 1200 positioner. How do I know if I damaged
something?
A: The typical failure in an over-current situation is a
short circuit. Your loop current will be maintained but
the Logix 1200 control board will receive no power.
With power removed from the Logix 1200 positioner,
use an ohmmeter to measure the ohms across the ter-
minals. If the reading indicates a short (close to zero
ohms), the field termination board must be replaced.
Make sure the positive lead is on the ‘+’ terminal and
negative lead is on the ‘-’ terminal when measuring the
resistance.
Q: What is the input resistance of the Logix 1200
positioner?
A: The Logix 1200 positioner does not have a simple
resistive input. When measuring the voltage across
the Logix 1200 positioner, it only varies slightly when
the current is changed from 4 mA to 20 mA (11.7 VDC
to 12 VDC nominal). This is because the Logix 1200
positioner is an active device. For the Logix 1200 posi-
tioner, effective resistance is commonly referred to.
(Effective resistance is the resistance at a given cur-
rent.) To explain further:
Effective Resistance = (Terminal Voltage)/Current
For example, at 20 mA: Effective resistance = 12
VDC/0.02 A = 600
Ω
The Logix 1200 positioner has a specification of 600
Ω
@
20 mA.
NOTE: One cannot measure across the terminals of
an unpowered Logix 1200 positioner and find the
effective resistance.
Air Action
Air-to-open and air-to-close are determined by the
actuator tubing and not the software. When air-action
selection is chosen during configuration, that selection
tells the control which way the actuator is tubed. Verify
that the actuator tubing is correct prior to a stroke cali-
bration. The top output port is called Output 1. It
should be tubed to the side of the actuator that must
receive air to begin the correct action. For example, for
an air-to-open linear actuator, Output 1 should be
tubed to the bottom of the actuator.
Linear vs. Rotary
The positioner has two configuration settings: Linear
and Rotary. For better resolution, stem position sensor
gains are adjusted based on the linkage angle of rota-
tion. The linear setting allows for linkage rotation up to
65°. The rotary setting allows for linkage rotation up to
95°. These settings only determine the angle of sen-
sor rotation and do not affect control parameters.
If a positioner is set to linear configuration and a red
LED blinks after calibration, the most common cause
is the sensor movement was greater than 65°. This
can occur if the roller pin was placed in the wrong hole
on the follower arm or the stem clamp is placed too
high on the actuator stem. The take-off arm should
always be level with the stem clamp on linear
mountings.
The Logix 1200 positioner has an electrical measure-
ment range of 95°. That is, the electronics will sense
stem position over a 95° range. With a rotary valve,
the typical rotation is 90°. When connecting a Logix
1200 positioner to a rotary valve, the 90° valve rotation
is centered within the 100° electrical range. If mechan-
ical movement falls outside the electrical measure-
ment range, the positioner can have a dead band at
one end of travel in which valve movement cannot be
sensed.
Frequently Asked Questions
Q: How do I know if the rotary linkage is centered
within the 95° electrical range?
A: The slot in the take-off arm has enough clearance
around the roller pin to move the follower arm slightly.
Move the valve to the fully closed position. At this posi-
tion, move the follower arm within the slot clearance. If
the valve does not respond by making an adjustment,
linkage adjustment is necessary. Repeat this test at
the fully open position.
To adjust the stem position linkage, use the Logix vari-
able number 2. This can be viewed as A/D feedback in
the Measured Value screen in ValTalk software or the
Hall pot sensor A/D value in the Condition screen
under View Variables in SoftTools TechCheck. It can
also be viewed from the HART 275 communicator in
the Status/Technician menu. With the valve in its
mechanical fail position (no pressure applied), slightly
move the follower arm while watching variable number
2. If the number does not change, the arm is not cen-
tered in the electrical range. (The number will jump
one or two counts due to noise at a fixed position and
should not be considered a change. It should move
greater than 10 to 20 counts if the linkage is centered
correctly.) If necessary, rotate the take-off arm or feed-
back sensor to bring the linkage in range.
NOTE: Due to the speed of HART communication,
allow two to three seconds for the display to update
after each adjustment.
This procedure is only necessary on a rotary mount-
ing. For linear mountings, the red LED will blink if 65°
travel is exceeded. Refer to the Calibration section for
further information on stroke calibration errors.