Board current alarm, Eeprom checksum alarm, Pressure alarms – Flowserve Logix 1200e LGAIM0044 User Manual
Page 38: Alerts, Mpc (minimum position cutoff), Frequently asked questions
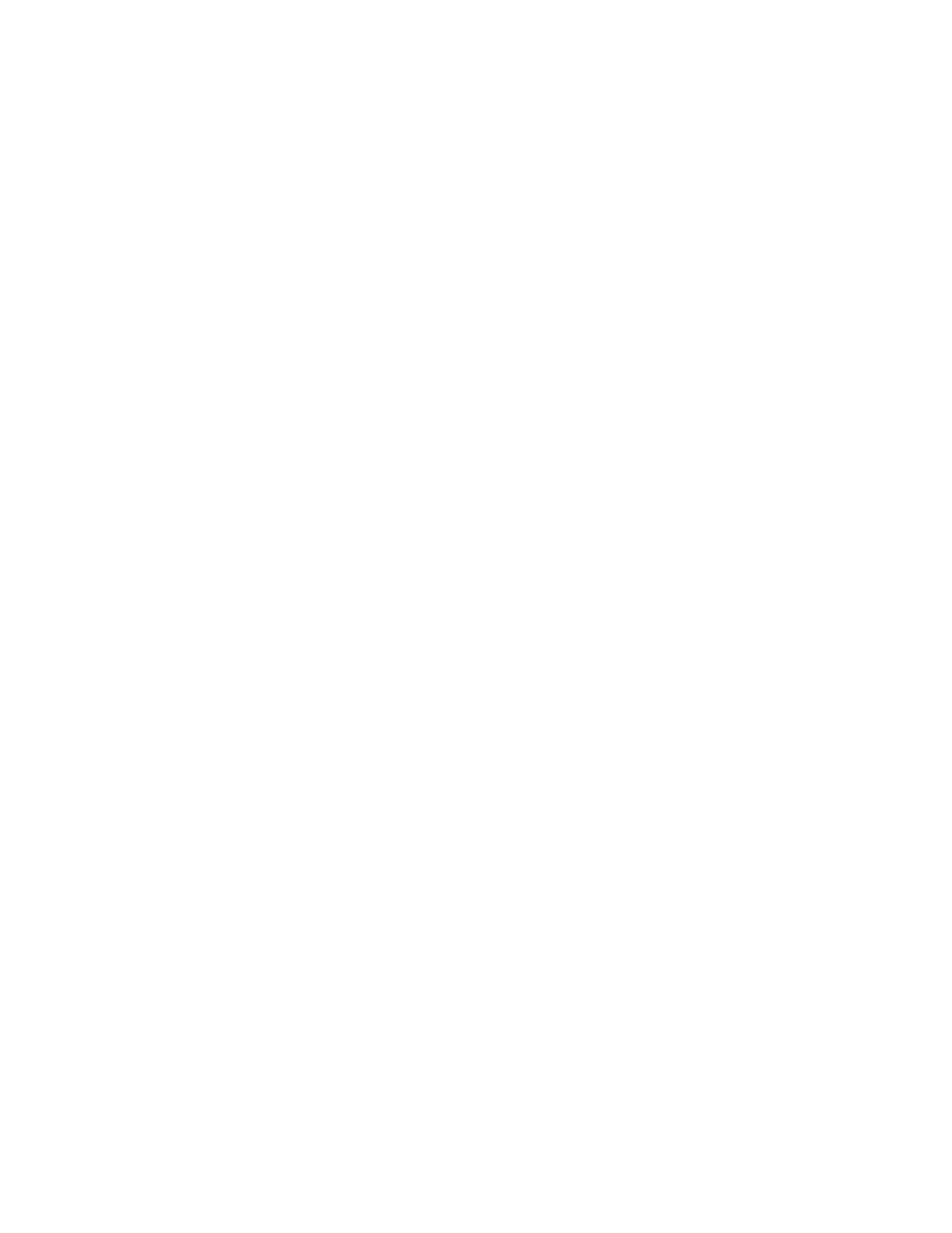
44-38
Flowserve Corporation, Valtek Control Products, Tel. USA 801 489 8611
Board Current Alarm
The Logix 1200 positioner is a loop-powered device,
which must run on very low power. During operation,
the current draw of the electronics is monitored. If cur-
rent draw is excessive and would prevent operation at
3.7 mA, the Board Current Alarm becomes active and
the red LED blinks. The most common cause is a
failed main PCB assembly. If the electronics’ current
draw is excessive, the Logix 1200 positioner will most
likely operate at higher currents (12 mA and above)
but may lose power at lower currents. This error
requires that the main PCB be replaced. Refer to
spare parts kit numbers section.
EEPROM Checksum Alarm
Configuration data is stored in EEPROM. When power
is lost, configuration information is retrieved from
EEPROM and operation resumes. A check is done by
the micro-controller after a power-up to make sure
data saved in EEPROM has not been corrupted. The
checksum is a number that is calculated based on
configuration data. It is also saved in EEPROM every
time data is stored. After a power-up, if this number
does not match the data in memory, an EEPROM
Checksum Alarm is generated and the red LED blinks.
If this occurs, turn off the power to the Logix 1200
positioner, followed by turning on the power. If the
error does not clear, try saving the configuration data
again using ValTalk or SoftTools software, or a HART
275 handheld communicator. If the previous configura-
tion has not been saved, reset the device and re-con-
figure. If these steps still do not clear the error, the
main PCB assembly must be replaced. Refer to spare
parts kit numbers section.
Pressure Alarms
NOTE: Pressure alarms are only available on models
with advanced diagnostics (Logix 121X).
Advanced diagnostic models add top, bottom and sup-
ply pressure sensors on more current models (Logix
1210e) the supply sensor is not included, instead,
supply is calculated using the other pressure sensors.
These sensor readings and alarms are only accessi-
ble from ValTalk or SoftTools software, or a HART 275
handheld communicator when the configuration has
been set to Advanced.
The Loss of Pressure Alarm becomes active when the
supply pressure is near the minimum positioner oper-
ating pressure of 30 psig (2.1 barg). If the LEDs alter-
nate between red and green, the supply pressure may
be at the limit threshold. This alarm is meant to alert
the user to low supply pressure as well as complete
loss of pressure.
Both the top and bottom sensors are checked during
actuator calibration. If a calibration reading appears to
be out of range, the appropriate alarm will become
active. The pressure sensors are located on the col-
lector board assembly.
Alerts
MPC (Minimum Position Cutoff)
The Minimum Position Cutoff (MPC) or tight shutoff
feature of the Logix 1200 positioner allows the user to
control the level at which the command signal causes
full actuator saturation in the closed position. This fea-
ture can be used to guarantee actuator saturation in
the closed position or prevent throttling around the
seat at small command signal levels. This features
defaults to 1% from the factory (which means it is
enabled).
NOTE: The positioner automatically adds a 1 percent
hysteresis value to the MPC setting to prevent jumping
in and out of saturation when the command is close to
the MPC setting.
Frequently Asked Questions
Q: I set the MPC at 5 percent. How will the positioner
operate?
A: Assume the present command signal is at 50 per-
cent. If the command signal is decreased, the posi-
tioner will follow the command until it reaches 5
percent. At 5 percent, the spool will be driven in order
to provide full actuator saturation. The positioner will
maintain full saturation below 5 percent command sig-
nal. Now, as the command increases, the positioner
will remain saturated until the command reaches 6
percent. (Remember the 1 percent hysteresis value
added by the positioner). At this point, the stem posi-
tion will follow the command signal.
Q: I have MPC set to 3 percent but the valve will not
go below 10 percent.
A: Check to see if the lower soft limit is enabled. The
lower soft limit must be less than or equal to 0 percent
for the MPC to become active. If a positive lower soft
limit is written, this limit will take priority over the MPC
feature.