Sanitizing syrup system – Scotsman RS160 User Manual
Page 18
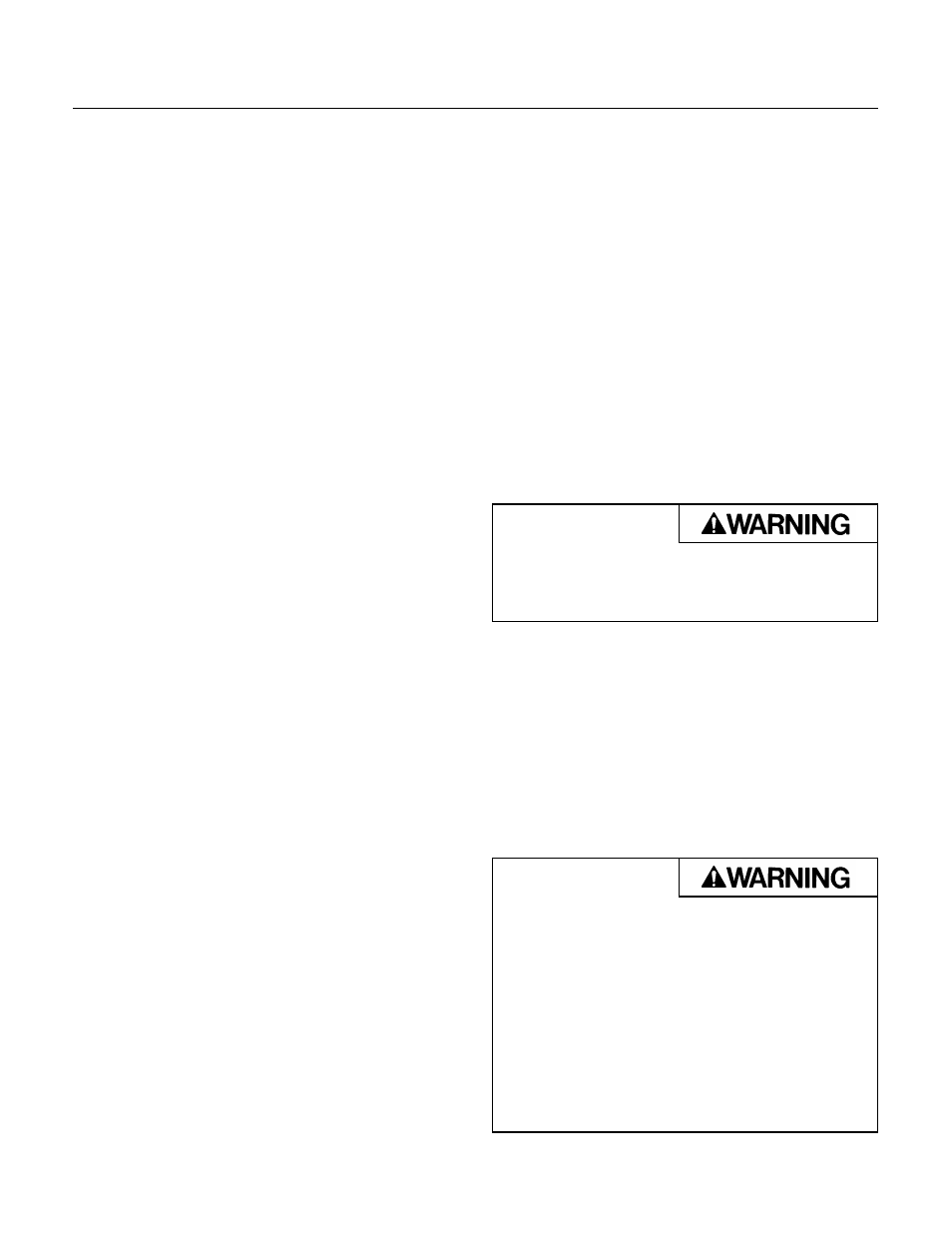
SANITIZING SYRUP SYSTEM
To Be Performed By Qualified Personnel Only
The procedure below is for the sanitation of one
syrup circuit at a time. Repeat to sanitize additional
circuits. These instructions are for a stainless steel
product tank system.
Note: When cleaning a bag-in-box beverage
system disconnect the coupling from the bag and
connect to a coupling cut from an empty bag.
Place the coupling into a stainless steel product
tank and use the procedures below but do not
pressurize the tank.
Materials Required:
••
Sanitizing agent such as “Chlor-tergent” (Oakite
products Co.).
••
Three empty, clean syrup tanks (5 -10 gallon)
••
An open container (1 - 5 gallon)
••
Plastic brush or soft cloth
1. Rinse tank - fill with cold (room temperature) tap
water.
2. Prepare sanitizing tank #1. Prepare the solution
by dissolving the required amount of concentrate
to supply 200 PPM (parts per million) available
chlorine in enough water to flush and sanitize the
number of circuits to be sanitized, usually about 1
gallon per circuit. Water temperature should be
between 125
0
F. and 145
0
F.
3. Prepare sanitizing tank #2. Prepare a solution
by dissolving the required amount of concentrate
to supply 100 PPM (parts per million) available
chlorine for about 1 gallon of solution. Water
temperature should be between 125
0
F. and 145
0
F.
4. Prepare a sanitizing container. Prepare a
solution by dissolving the required amount of
concentrate to supply 100 PPM (parts per million)
available chlorine for about 1 gallon of solution.
Water temperature should be between 125
0
F. and
145
0
F.
5. Disconnect all lines from product tanks.
6. Connect CO
2
cylinder with regulator set at 45 -
50 psi to each tank as needed in steps 8 - 11.
7. Connect sanitizing tank #1 (200 PPM) to
product lines. Actuate each valve to flush sanitizing
solution through the system for 2 minutes. Allow
the solution to remain in the system for a minimum
of 5 minutes.
8. Connect rinse tank to product lines and open
dispensing valves to flush sanitizing solution from
the system.
9. Remove the dispensing valves and quick
connect sockets. Remove nozzle and diffuser of
valves, if applicable. Clean all surfaces with 100
PPM sanitizing solution and cloth, if necessary.
10. Place removed valve parts and quick
disconnect sockets in the sanitizing solution (110
PPM) for fifteen minutes.
11. Reassemble valves and install on dispenser.
Reconnect quick connect sockets.
12. Connect sanitizing tank #2 (100 PPM) to
product lines and draw sanitizing solution through
each valve for two minutes. Allow sanitizing
solution to remain in the system for a minimum of
twenty (20) minutes. Disconnect sanitizing tank.
13. Reconnect all lines.
14. Connect a tank containing clean,
uncontaminated product to product lines. Draw
product through the lines until all sanitizing solution
has been removed from the system.
Flush sanitizing
solution from syrup
system.
Residual sanitizing solution left in the system
could create a health hazard.
To avoid personal injury
or property damage, do
not remove cover from the pressurized tank until
all pressure has been released from the tank.
RS160 and RS220
June 1995
Page 18