Super Systems 7EK 31080 User Manual
Page 22
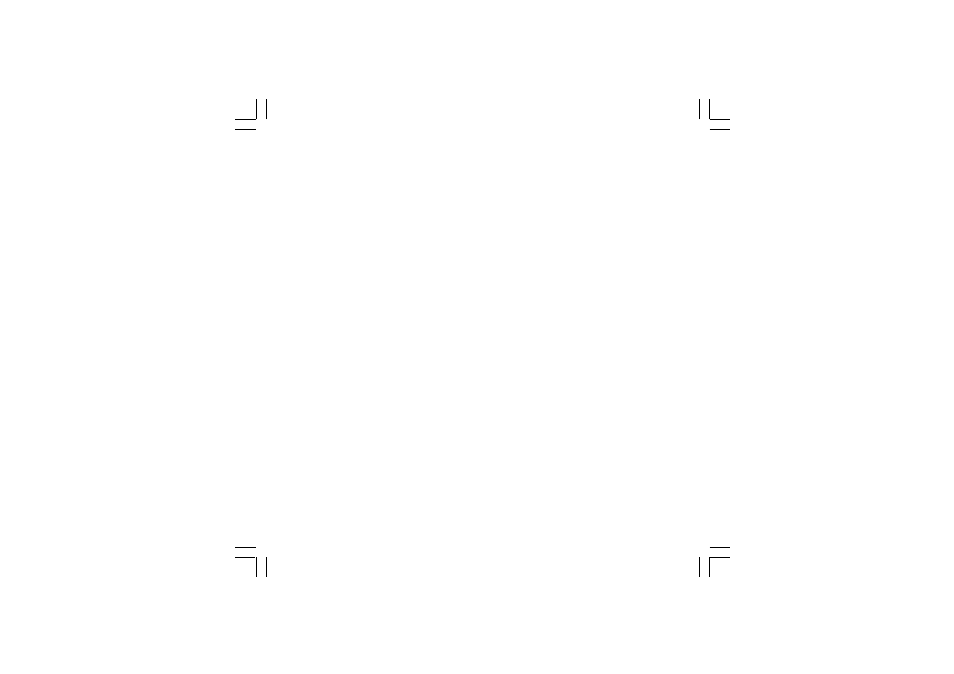
18
The transfer from AUTO to MANUAL and viceversa is
bumpless (this function is not provided if integral action is
excluded).
If transfer from AUTO to MANUAL is performed during the
first part of SMART algorithm (TUNE) when returning in
AUTO the device will be forced automatically to the
second part of the SMART algorithm (ADAPTIVE).
At power up the device will be in the AUTO mode or as it
was left prior to power shut down depending on P37
configuration selection.
Note: When start up occurs in Manual mode the power
output (OUT1 - OUT2) is set to 0.
OUT 1 FAILURE DETECTION FUNCTION
The device is capable (for the load driven by the OUT 1)
to measure and display:
- the current running in the load when the load is
energized
- the leakage current, flowing through the load, when the
load is de-energized.
If the P10 parameter has been correctly set, the
instrument generates an alarm when:
- the current running in the load is lower than the "Hbd"
parameter value (It shows a partial or total break down
of the load, the break down of the actuator or a power
down due to a protection or a fuse intervention);
- the leakage current is higher than the "SCA" parameter
value (It shows a short circuit of the actuator).
The "Display function" paragraph describes how to show
the two current values.
A fault condition is shown by OUT 3 LED flashing and by
OUT 3 relay status.
If the ON or OFF period is lower than 400 ms the relative
measurement couldn't be performed and the instrument
will show flashing the last measured value.
"LOOP BREAK ALARM" FUNCTION
The functioning principle of this alarm is based on the
concept that, with a steady load and steady power output,
the process rate of rise [deviation (P48)/time (P49)] is
steady as well.
Thus, analyzing the process rate of rise of the limit
conditions it is possible to estimate the two rates of rise
which define the correct process behaviour.
The limit conditions are:
3
for one control output: 0% and the value of the "OLH"
parameter or
3
for two control outputs: 100% and the value of the
"OLH" parameter.
The LBA function is automatically activated when the
control algorithm requires the maximum or the minimum
power and, if the process response is slower than the
estimated rate of rise, the instrument generates an alarm
indication in order to show that one or more element of
the control loop is in fault condition.
Deviation: from 0 to 500 units.
Timer: from 1 sec. to 40 min.
Hysteresis: from 1% to 50 % of the output span.
NOTES:
1) The LBA does not operate during the soft start.
2) If the instrument operates with the SMART function, the
LBA may be operating.
3) For this special function the hysteresis is related with
the power output value and not with its rate of rise.
SP/SP2 SELECTION
It is possible to select the operating set point (SP or SP2) only
by a logic input (terminals 7 and 8).
By setting P45, it is possible to display the final or the
operative set point during a ramp execution.
31080-1-00.p65
3/24/00, 11:58 AM
18