Clutch replacement, Electrical troubleshooting, Clutch does not engage – AIRLESSCO SS4550 User Manual
Page 25
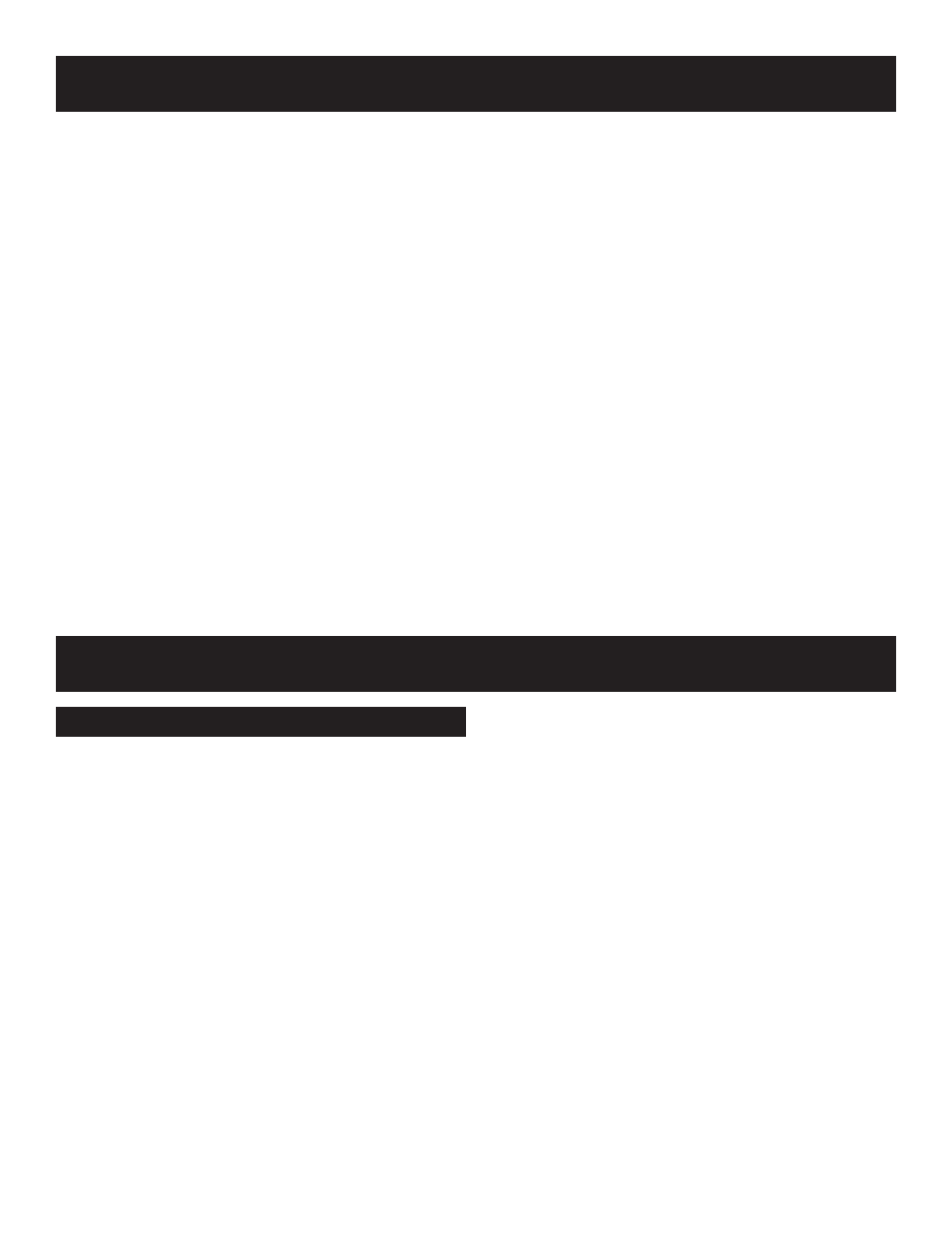
22
23
STEP 1: Ensure that the pressure control knob (POT) is in the maximum (CW) position.
STEP 2: Remove the upper and lower clutch and electrical covers.
STEP 3: Check all electrical connections between the engine magneto, sensor, control board and clutch for loose
connections or damaged leads. See Fig.26.
STEP 4: Disconnect the two leads from the control board (blue) and the clutch assembly (black). Using a multimeter,
with the engine at maximum RPM, pressure control knob in the maximum position and the prime valve open (priming)
position, test the DC voltage across the boards leads (blue). This voltage must be 13-14 VDC. If the readings are correct,
the board, sensor and magneto are okay and the problem is the clutch assembly. If this is the case, proceed to Step 5. If
the voltage is outside this range go to Step 7.
STEP 5: Measure resistance between the clutch leads (black). This value must be 10-16 ohms. If this reading is out of
specifications the clutch is defective and must be replaced, otherwise continue troubleshooting.
STEP 6: If the clutch resistance readings of Step 5 are correct, check spacing between the clutch field and plate. The gap
should be .012” to .024”. If the gap is greater than .024 the gap is too wide. If this gap is too wide, remove the spacer (Fig.
28, Item 7) from the clutch assembly. Should the clutch still not engage, replace the clutch assembly. See below.
STEP 7: When the DC voltage from the board is not 13-14 VDC, disconnect the control board lead (black) from the
engine magneto lead (pink), located on the side of the engine. With the engine at maximum RPM, pressure control knob
in maximum (CW) position and prime valve open (priming), read the AC voltage from the magneto lead to the sprayer
frame. This reading should be 19-24 VAC. If outside this range, contact your local Honda repair facility for magneto
replacement. If the magneto is producing the proper AC voltage, continue to Step 8.
STEP 8: Test the sensor by reading the resistance between the red and black wires. The resistance runs between 1.5-3
kohms. A defective sensor usually shows no resistance (open). If the reading is outside standards, replace the sensor.
An alternative method to test the sensor, is to plug a new sensor into the board and see if the clutch will engage. Caution!
When using this method, ensure prime/pressure valve is in the prime position. This is important because the sensor
plugged into the board is not measuring pressure in the fluid section.
STEP 9: When Steps 7 & 8 have been completed and the magneto and sensor check good, the electrical control board
is the only item left, replace the board. See page 22.
ELECTRICAL TROUBLESHOOTING
- Clutch Does Not Engage
CLUTCH REPLACEMENT
REMOVING THE CLUTCH
REFER TO FIGURES 26-30
1. Remove the gear box cover (Fig 30, item 1) by
disconnecting fluid hose to the manifold filter and by
unscrewing the four allen head bolts (Fig 30, item 36).
2. Disconnect the fluid pump as described on page 16.
3. Pull off the spacer tubes (Fig 30, item 30) and drop the
sleeve bearing down and off. Slide the connecting rod off
the gear box.
4. Remove the top cover (Fig 30, item 2) by unscrewing the
6 mounting screws. be careful not to lose the 6 matching
grommets.
5. Remove the bottom cover (Fig 30, item 14) by
unscrewing the 2 bolts and nuts.
6. Remove the splash cover (Fig 30, item 12) from the
clutch brackets and spacer tubes.
7. Disconnect the two clutch leads from the electrical
control board leads and the clutch spring (Fig 28, item 9)
from the spacer tube.
8. Loosen (do not remove completely) the block tensioner's
set screws (Fig 27, item 6) to detension the belt.
9. Loosen (do not remove yet) the four plate bolts.
10.Pull the cog belt loose from the engine shaft cog pulley
and let hang loose on the clutch cog pulley.
11.Remove the two vertical bracket screws
(Fig 30, item 20).
12.Remove the four horizontal screws throught the
gearbox plate (Fig 27, item 5) and lift the gear box off the
machine.
13. Place gearbox in vice by gripping the flat part of the
drive crank allowing the clutch assembly to face up. Use
caution and not allow gearbox to swing and damage
casting against vice.
14. Hold coupling screw, with 13/16" wrench, then with
5/16" allen wrench, screw differential screw out of
coupling screw and gearbox shaft.
15.Remove the coupling screw from the clutch bore.
NOTE: AFTER EXTENDED USE THE COUPLING SCREW
CAN HANG UP INSIDE OF THE CLUTCH BORE. TAPPING
ON THE SIDE OF THE COUPLING SCREW AND/OR
THE USE OF A LIGHTWEIGHT OIL OR BREAK FREE
PRODUCT CAN EASE THE REMOVAL PROCESS. IN
EXTREME CASES, SCREW THE DIFFERENTIAL SCREW
LARGE THREAD SIZE IN, THEN PLACE A WASHER AND
NUT ON THE SMALL THREAD SIDE. THIS ALLOWS THE
PULLING OR PRYING ON THE COUPLING SCREW IN
ORDER TO REMOVE IT.
11.The clutch and other components can now be slide off
the gear box shaft.