Flowserve M Slurry User Manual
Page 34
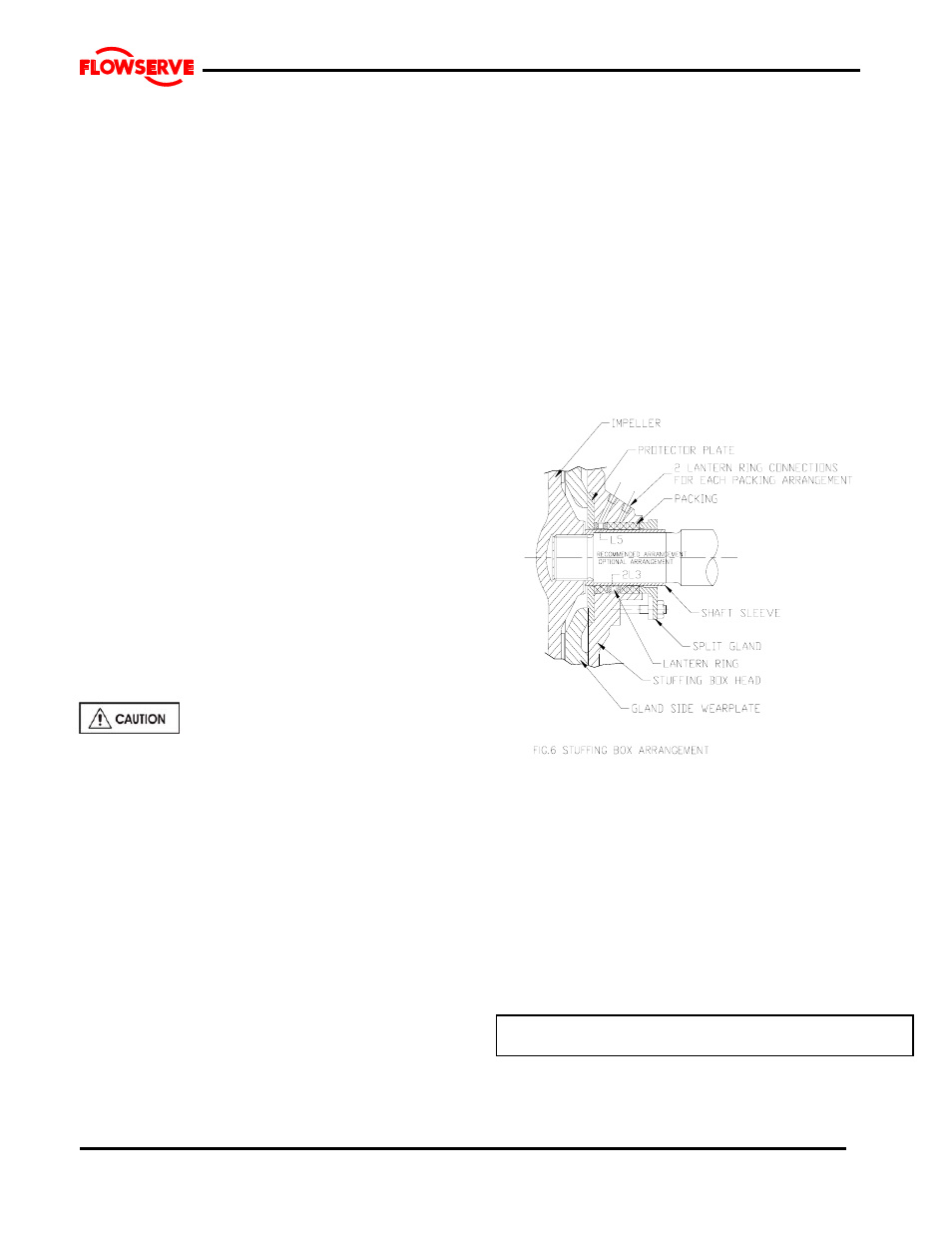
M SLURRY USER INSTRUCTION ENGLISH 71569241 - 02/08
Page 34 of 60
®
a) Remove the bearing housing from the rotor
assembly.
b) Brush the bearing housing with hot kerosene (100
to 115 °C/212 to 240 °F) or other non-toxic
solvent.
c) Clean and flush out the housing with a light
mineral oil.
d) Do not use waste oil to clean the housing.
To clean the bearings:
a) Wipe off as much grease as possible with a clean
lint-free cloth.
b) Brush bearings with hot kerosene (80 to 90 °C/
175 to 195 °F) while gently spinning the outer
bearing ring.
c) Spin each ball to ensure that it is clean.
To remove badly oxidized grease which refuses to
come off:
a) Support the rotor in a vertical position and
immerse the bearing in hot kerosene or a mixture
of alcohol and light mineral solvent.
b) Gently spin the bearing outer ring.
c) Dry and reflush the bearing with clean light oil.
d) It is important not to under or over grease the
bearings as this will lead to over heating and
premature failure. It is recommended that the
bearings be filled with grease using a suitable
spatula. In addition the housings should be no
more than half filled.
6.2.3.2 Oil lubrication
Maintaining the correct oil level is very
important.
If the pump is supplied with a constant level oiler the
oil level will be automatically maintained and as long
as oil is visible in the glass bottle there is no need to
refill. If however a sight glass has been fitted then
regular checks should be made to ensure the level is
maintained at the centre of the glass window.
Refer to section 5.1.1 for methods of oil fill, section
5.2.1 for oil grade recommendations and 5.2.4 for the
schedule and temperature limits.
6.2.4 Mechanical seals
No adjustment is possible. When leakage reaches an
unacceptable level the seal will need replacement.
6.2.5 Gland packing
6.2.5.1 Water Lubricated Packing: The stuffing box
split gland can be completely removed for re-packing
or to enable the addition of extra rings of packing.
The stuffing box is normally supplied with a lantern
ring to enable a clean or pressurised flush to the
centre of the packing. If not required, this can be
replaced by an extra 2 rings of packing.
There must always be a small leakage, normally a
minimum of 120 drops per minute to atmosphere to
lubricate and cool the packing is required. The stuffing
box is provided with 4 lantern ring connections (2 inlet,
2 drain), The packing may be arranged in one of two
ways (See Fig. 6).
(
2200
)
(2445)
(
4132)
)
(
9321)
)
(4120)
(2445)
(4100)
(1915.2)
The recommended arrangement (L5) is preferred to
constantly flush the slurry away from the sleeve and
packing. Generally a flow rate of 2 GPM per inch of
sleeve diameter will be sufficient to flush and lubricate
the stuffing box area. The sight condition will dictate
the actual flow rate required .
To reduce dilution of process liquid or the quantity of
seal water, the optional arrangement (2L3) may be
used.
The pressure of the flushing water may be calculated
as follows:
where y=0.6 for standard duty M pumps and Y=0.8 for
severe duty M pumps (refer to Engineering Data Table,
supply pressure =Y x TDH/2.31 x SG + Suction pressure +
5 psi