Flowserve LPNV Worthington User Manual
Page 14
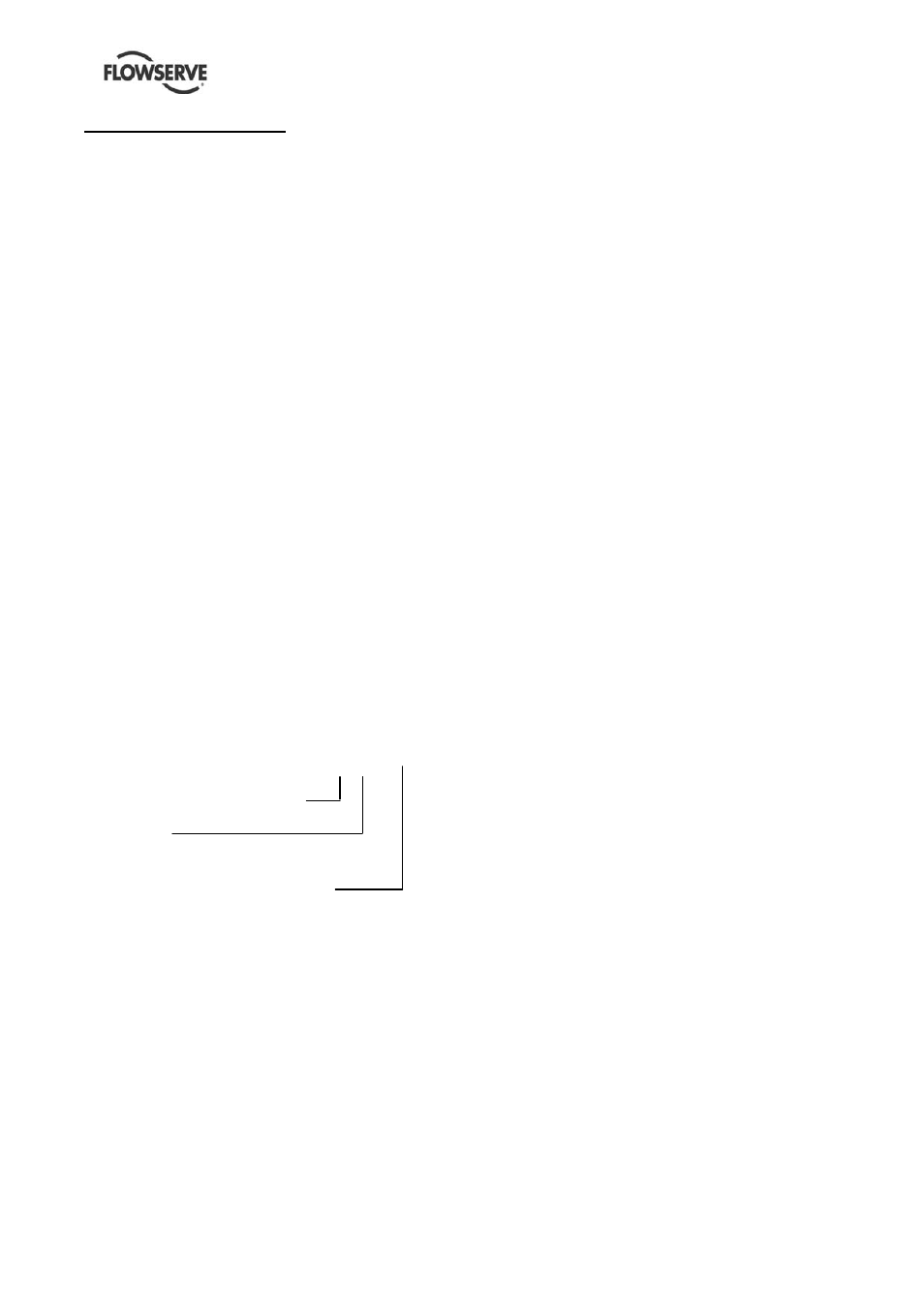
LPNV USER INSTRUCTIONS ENGLISH 87900031 – 06/14
Page 14 of 48
3 PUMP DESCRIPTION
3.1 Configurations
The LPNV pumps are single stage, double suction
impeller, double volute vertically split casing,
vertically mounted on a bottom bracket integrally
casted with the stationary half-casing, with
side/side nozzles, medium pressure pumps,
preferred for water cooling, fluid transfer and
general services.
LPNV pumps are fully compliant with API 610/ISO
13709, latest edition.
The LPNV pumps provide both outstanding
performance and the highest reliability level as
required in the most arduous services of the
process industry.
The different sizes available, combined with the
choice of impellers, ensure optimum efficiency
throughout the range.
Various options of construction materials and
bearing types are available.
Standard Rotation of LPNV pumps is counter
clockwise (CCW) when viewed from the coupling
end. Clockwise (CW) rotation can be supplied on
request.
3.2 Nomenclature
The pump size will be engraved on the nameplate
typically as below:
6 LPNV 18
Nominal discharge branch size
Pump type
Nominal full size impeller diameter
The typical nomenclature above is the general
guide to the LPNV description. Identify the actual
pump size and serial number from the pump
nameplate. Check that this agrees with the
applicable certification provided.
3.3 Design of major parts
3.3.1 Pump casing
The casing is vertically split with suction and
discharge nozzles cast integral with the stationary
half. The removable casing half permits inspection
and/or repair of the rotor without disturbing the
suction and discharge piping.
The double volute casing minimizes the radial
thrust on the pump rotor and gives longer life to
the seals, bearings and wear rings. The casing
halves are sealed by the use of a confined gasket
and are joined together by studs, which are
installed in the lower half casing and fastened with
cap nuts. Confined gasket design allows metal-to-
metal contact for proper gasket compression and
eliminates the risk of corrosion of bolts and nuts.
The casing is provided with vent, drain and seal
connections.
3.3.2 Impeller
The impeller, designed for maximum hydraulic
efficiency, is double suction, closed type.
The double suction design allows minimum NPSH
requirement and provides symmetric pressure
distribution acting on impeller shrouds, for a
complete axial balance of the rotor.
The impeller first, and then the complete rotor, are
dynamically balanced for vibration free operation.
The impeller is keyed to the shaft and secured
against axial movement by means of a threaded
shaft nut on one side, and by means of a split
locating ring and a shaft locking nut on the other
one.
3.3.3 Wearing Rings
Wear rings fitted both on casing and impellers are
smooth depth design.
The diameters of the wear rings are differentiated
to maintain a controlled axial load on the bearing
under all operating conditions.
Both rings are of the renewable type and are held
in place by a press-fit with threaded dowels on the
impellers and by grooves and pins on the casing.
Clearances between wear surfaces are in
compliance with API 610 Standard.
3.3.4 Rotors
Rotors are of the stiff shaft design, with the first dry
critical speed above the maximum rotational
speed.
Shafts are of ample diameter, combined with the
minimum bearing span to minimize shaft deflectors
especially when the pump is operating at off peak
conditions.
Shafts are machined and finished throughout their
length for positive location of the rotating parts
and to ensure minimum runouts. The whole shafts
are protected by sleeves and mounted-on parts
extending up to throat bushing area.
Shafts are designed to meet API 610 Latest
Edition deflection and vibration requirements. Fully
assembled rotors are dynamically balanced can
accommodate a wide variety of single or dual seal
arrangements as standard.