Flowserve LPNV Worthington User Manual
Page 26
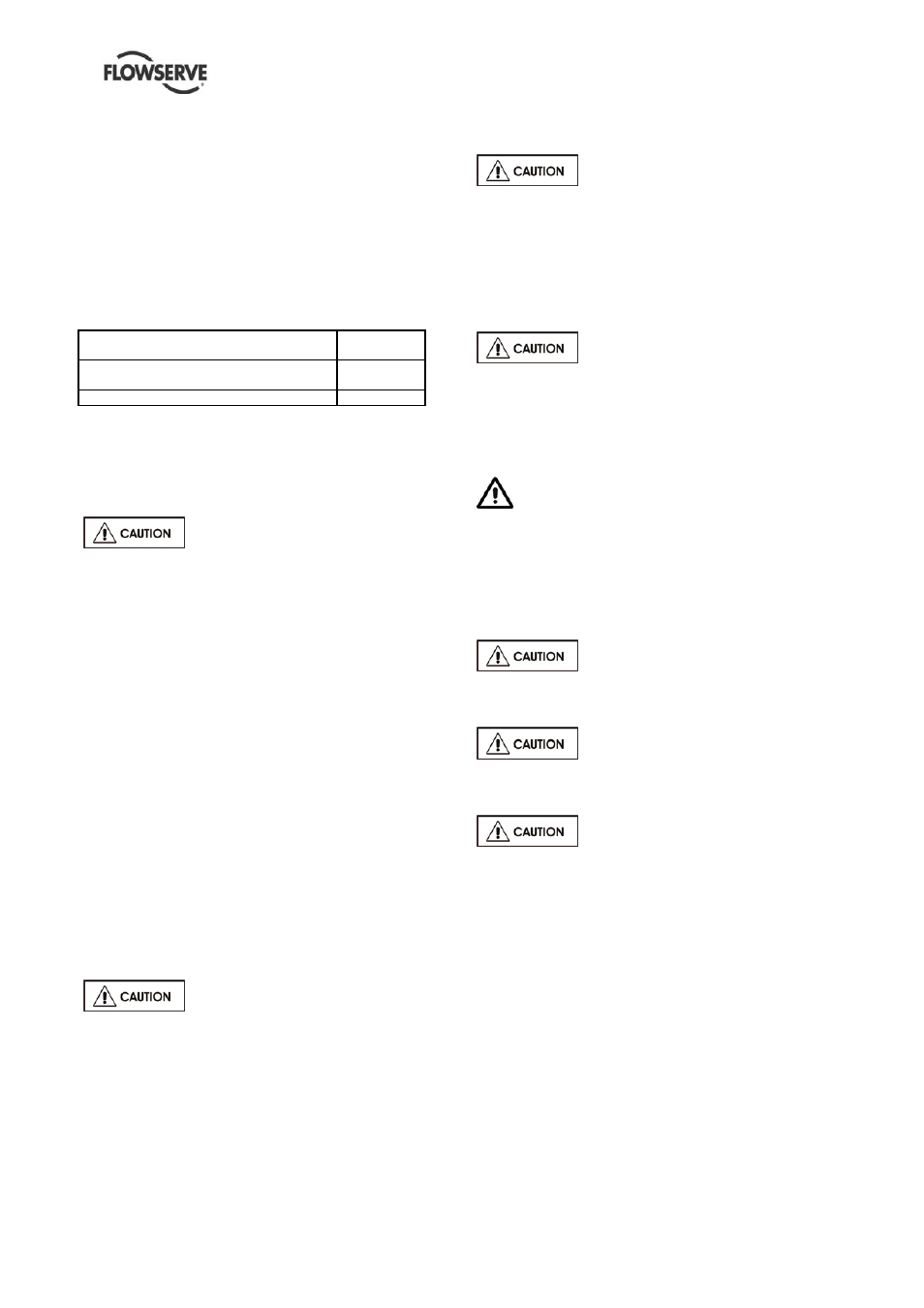
LPNV USER INSTRUCTIONS ENGLISH 87900031 – 06/14
Page 26 of 48
If a synthetic lubricant (fire resistant fluid) is to be
used instead of the normal type oil for the lubrication
of bearings, gears etc., the material of all gaskets
and "O" rings in contact with the lubricant must be
compatible with the lubricant. Normal gasket
materials will usually swell and deteriorate when
immersed in synthetic lubricants: also normal paints
will peel from internal walls of reservoirs and bearing
chambers.
5.2.2 Bearing housing oil limitations
Recommended Oil Temperature At Start Up
15.6 °C
60 °F
Desirable Operating Temperature
60-71 °C
140-160 °F
Oil Level Above Oil Connection Centre line
6 mm
When the starting temperature is below -10 °C (14
°F) for long time it’s suggested to use a synthetic oil.
Other drivers and gearboxes, if appropriate, should
be lubricated in accordance with their manuals.
In the case of product lubricated bearings
the source of product supply should
be checked against
the order. There may be requirements for an
external clean supply, particular supply pressure or
the commencement of lubrication supply before
pump start-up.
5.2.3 Lubrication schedule
Normal oil change intervals are 4000 operating hours
or at least every 6 months. For pumps on hot service
or in severely damp or corrosive atmosphere, the oil
will require changing more frequently. Lubricant and
bearing temperature analysis can be useful in
optimizing lubricant change intervals.
The lubricating oil should be a high quality mineral oil
having foam inhibitors. Synthetic oils may also be
used if checks show that the rubber oil seals will not
be adversely affected.
Based on the specified operating conditions and an
ambient temperature of 43°C (110 F) for ring-oiled or
splash systems, oil sump temperature below 82 C
(180°F) is expected.
A continuously rising temperature, or
an abrupt rise, indicate a fault.
5.3 Direction of rotation
Ensure the pump is given the same
rotation as the pump direction arrow fit on bearing
housing. In any case the direction of rotation must
be checked with the pump disconnected.
To avoid dry running, the pump must either be filled
with liquid or have the flexible coupling disconnected
before driver is switched on.
If maintenance work has been carried
out to the site's electricity supply, the direction of
rotation should be re-checked as above in case the
supply phasing has been altered.
5.4 Guarding
Guarding is supplied fitted to the pump set.
If this has been removed or disturbed ensure
that all the protective guards around the pump
coupling and exposed parts of the shaft are
securely fixed.
5.5 Priming and auxiliary supplies
Ensure all electrical, hydraulic,
pneumatic, sealant and lubrication systems (as
applicable) are connected and operational.
Ensure the inlet pipe and pump
casing are completely full of liquid before starting
continuous duty operation.
Before starting or while operating
the pump, the casing and suction line must be
completely filled with the liquid being pumped.
The rotating parts depend on this liquid for
lubrication and the pump may seize if operated
without liquid.